Blue economy
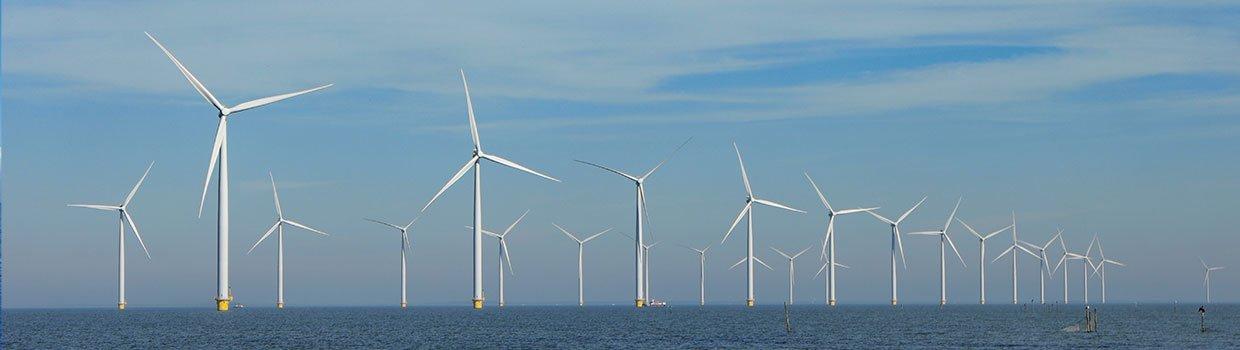
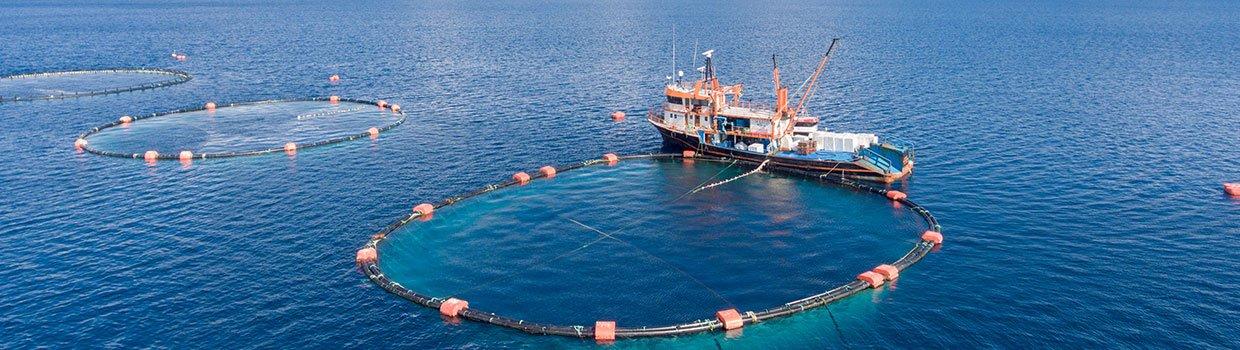
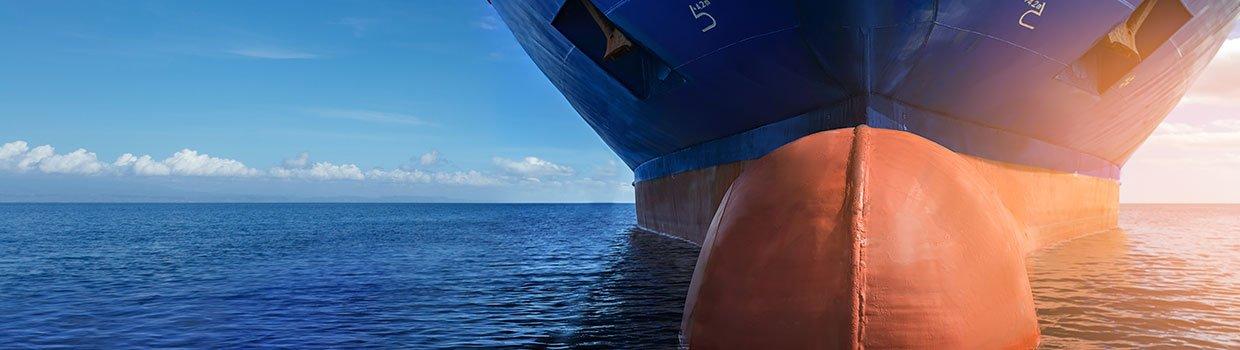
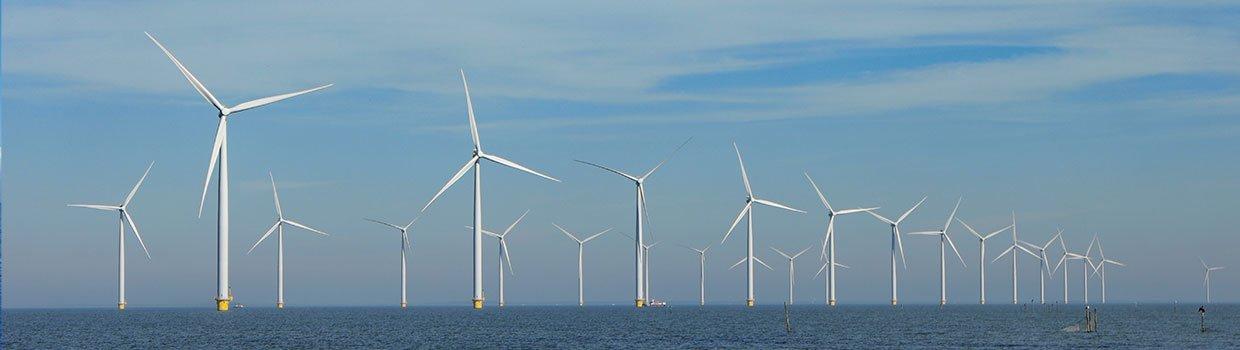
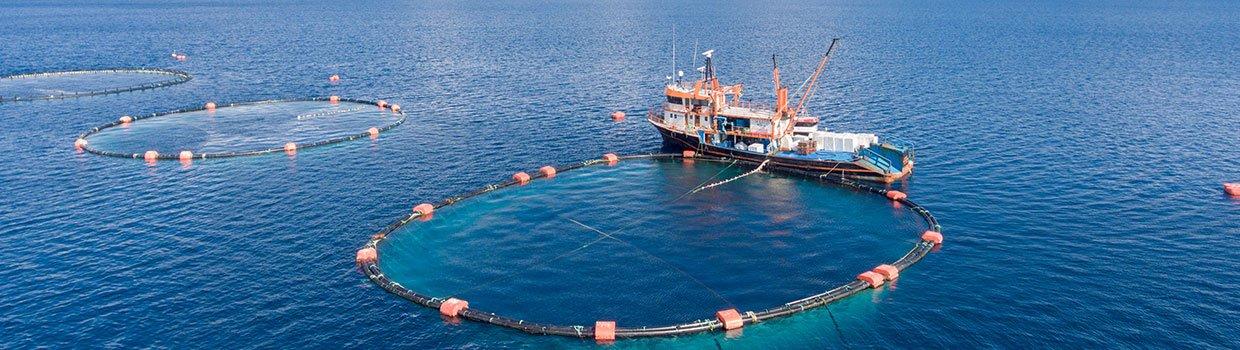
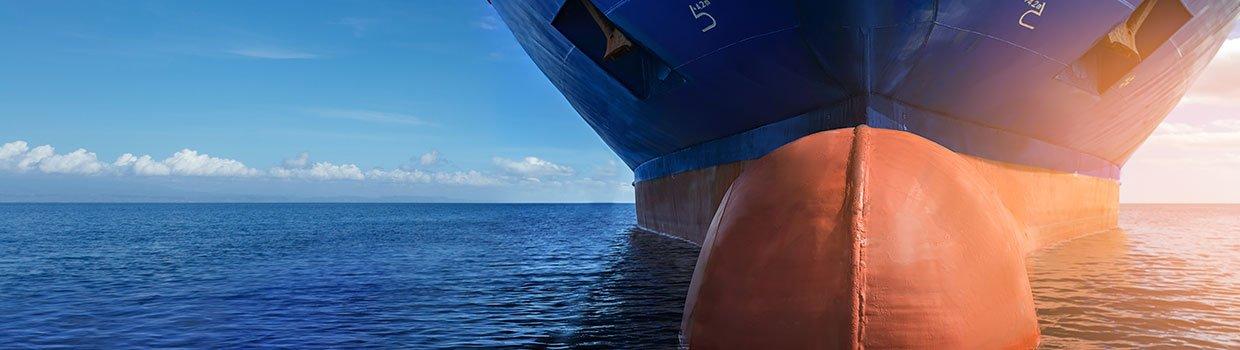
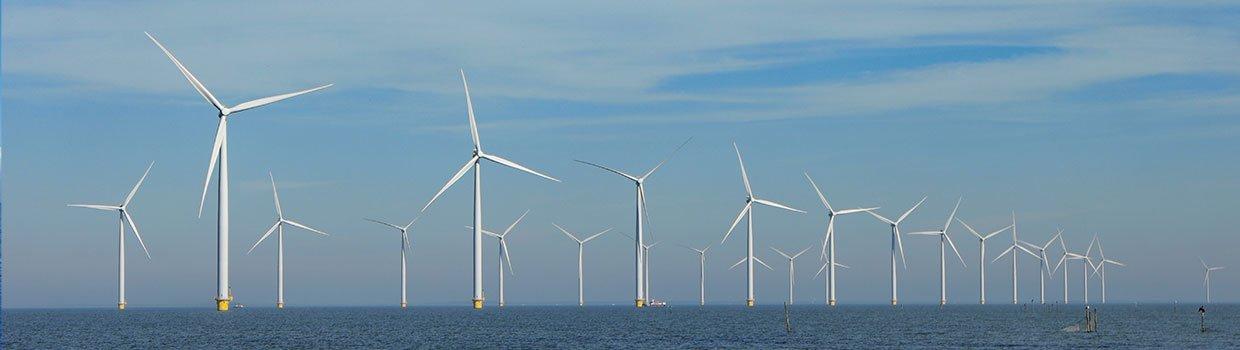


News
The International BoatBuilders’ Exhibition and Conference (IBEX), North America’s premier technical trade event for the recreational marine industry, announced its slate of new presentations, panel discussions, and technical seminars as part of its world-class IBEX Education Conference. With a can’t-miss lineup of opportunities from Tech Talks to Main Stage events, the 2025 IBEX Education Conference features sessions for everyone from leadership to engineers. This year’s IBEX Main Stage will return with a showcase of sessions every day of the Show, with topics ranging from managing tariffs, trade, and supply chain to workforce development, and much more. Featured speakers Featuring speakers like Robyn Boerstling, Senior Vice President, Government Relations at the National Marine Manufacturers Association (NMMA); former NMMA President Dr. Thomas Dammrich; Freedom Boat Club President Cecil Cohn; National Marine Electronics Association (NMEA) President and Executive Director Mark Reedenauer; and many more noteworthy marine industry pioneers, the Main Stage will offer attendees thought-provoking education to bring their businesses into the future. Technical seminar series Conference will include presentations from the industry’s major experts on topics such as AI Afloat The technical seminar series, produced in collaboration with the Show’s education partners – Professional BoatBuilder magazine, the American Boat & Yacht Council (ABYC), the NMEA and IBEX co-owner the NMMA – will dive into a range of topics from fundamental skills to cutting-edge advanced training for the boat building, design, and repair industries. With more than 50 individual Seminars, this year’s Conference will include presentations from the industry’s major experts on topics such as AI Afloat: Assessing the Promise of Intelligent Technology for Safety, Efficiency, and Autonomy at Sea; The Perils of Paint: Creating Consistency in Yacht Coatings; Developing Full Foils for Recreational Boats; How To Conduct an Engineroom Inspection: What To Look for Working in, or Walking Through Engine Compartments; The Latest in Digital Switching: Where ABYC and NMEA Meet; and Outstanding Outsourcing: Integrating Subcontractors Into Your Team. With all paid and verified participation at IBEX seminars, attendees can receive one Continuing Education Unit (CEU) per one hour of training. New catalog of topics The IBEX Education Conference will include free Tech Talk workshops all three days of the show Also returning with a new catalog of topics from brand loyalty building to defending design and much more, the IBEX Education Conference will include free Tech Talk workshops all three days of the show in the popular Tech Talk Theater, located on the third floor exhibit hall. Attendees can also take advantage of getting an early jump on their IBEX educational experience with special Pre-Conference sessions hosted by Show exhibitors. Designed to inspire and prepare the next generation of marine professionals, IBEX and ABYC will host a Student Career Day on October 9, offering students from area technical schools industry exposure, meet and greet opportunities, and access to exhibit halls. Education conference New this year, students can use the Career Day Connections map on the BEX app to meet exhibitors with job openings, hands-on demos or who simply welcome students to the show. The full Education Conference schedule is available on the IBEX website. The Education Conference packages and tickets are available in the registration process, with Early Bird pricing through September 5. Central hub for collaboration “IBEX serves as a central hub for collaboration and real-time problem solving to bring together some of the brightest minds in boatbuilding, with its educational lineup at the cornerstone,” said Mary Velline, IBEX Show Director. “We know that our industry is facing new challenges every day and the best way to face those challenges is by learning and working together. We are very excited to bring educational opportunities to every level of marine business through this year’s expanded schedule.” Registration is open for this year’s IBEX, scheduled to return to the Tampa Convention Center, October 7 – 9, 2025.
The Coast Guard Foundation has been named the official charitable partner of the Chicago International Boat Show, a new event coming to Navy Pier Marina August 22-24, 2025. This partnership gives boaters a unique opportunity to support the Coast Guard Foundation while enjoying the best in boats, gear, and lakefront experiences. The three-day event will feature more than 150 luxury boats and yachts, 70 exhibitors showcasing the latest in marine technology and services, and a full schedule of live demos, workshops, and family-friendly activities. Attendees can enjoy local food, on-water fun, and expert panels that cover a wide range of boating topics. Coast Guard Foundation When purchasing tickets, guests have the option to add a $1 donation to the Coast Guard Foundation “Partnering with the Coast Guard Foundation means more than just putting on a great event,” shared Anthony Trimino, CEO of Revel Republic, the team behind the Chicago International Boat Show. “It’s our way of supporting the Coast Guard community and showing appreciation for their service.” When purchasing tickets, guests have the option to add a $1 donation to the Coast Guard Foundation. Every dollar supports the Coast Guard Foundation’s full mission that includes scholarships and education grants for Coast Guard children and spouses, emergency relief for Coast Guard families when natural disasters strike, and morale and wellness programs that strengthen the entire Coast Guard community. Coast Guard families “Being part of this event means a lot to us,” said Susan Ludwig, president and CEO of the Coast Guard Foundation. “It’s a meaningful way to connect with people who care about life on the water and want to give back to Coast Guard members and families who serve our nation every day.”
Oceanology International, the world’s renowned forum for ocean science, engineering and technology, returns to London’s ExCeL from 10th to 12th March 2026, to connect the global ocean community for three unmissable days of innovation, networking and thought leadership. Welcoming engineering, survey and science professionals from ocean industries including offshore energy, ocean observation and defence, the 2026 edition will spotlight breakthrough solutions driving the future of ocean exploration, environmental monitoring and sustainable marine operations. Attention on the critical coastal sector COAST is launching to increase attention on the critical coastal and shallow water sectors Adding a fresh dimension for 2026, COAST is launching to increase attention on the critical coastal and shallow water sectors. The new focus will ensure that coastal resilience, infrastructure and engineering will be at the heart of an event which once again promises to connect the world’s ocean engineering, technology and science communities from more than 80 countries. Demand for new solutions and collaboration COAST will further enhance the traditionally diverse Oceanology International (Oi) program, across both the exhibition and conference by highlighting breakthrough developments in coastal protection, erosion control, sediment transport analysis, shoreline stabilisation, and climate adaptation that support sustainable coastal development and ecosystem protection. Awarded the title of RX UK Show of the Year in 2024, the next edition in the 55-year history of the biennial event will demonstrate how Oi continues to evolve and adapt in response to the demand for new solutions and collaboration in the energy transition and blue technology markets. Latest topics impacting future ocean technology There will also be a full content program, reflecting the latest topics impacting future ocean technology First-time exhibitors and visitors in coastal fields are invited to join stakeholders, spanning industry, government and academia, from engineers, hydrographers and geotechnics to energy professionals, oceanographers, site investigators, marine surveyors and many more, who will unite across a wide range of sectors, including renewables, offshore oil & gas, defence, maritime security, marine science, ports, aquaculture and subsea. There will also be a full content program, reflecting the latest topics impacting future ocean technology and economic needs and encompassing a range of content aimed at improving strategies for exploring, protecting and sustainably operating in the world’s oceans and waterways. Effective maritime operations David Ince, Oi event Director, said: "We are delighted to announce that plans for another defining, inspirational and highly relevant Oceanology International in 2026 are gathering momentum. Following Oi24, which exceeded all expectations, we remain committed to fulfilling our mission for the global marine science and ocean engineering and technology communities to act as the premier facilitator of ocean connection." He adds, "The launch of COAST at Oi26 is in response to the critical challenges facing our coasts in the face of storms, flooding, erosion and rising sea levels, highlighting the essential engineering developments which are ensuring healthy ecosystems, strong sea defences, effective maritime operations, thriving ports and harbours, and secure offshore energy infrastructure." New opportunities to discover cutting-edge solutions David Ince continues: "COAST is a new gateway for pioneering companies in the field to join the global gathering at Oi and gain access to a highly targeted and engaged audience – to demonstrate their solutions for dynamic nearshore environments and engage with coastal engineers, hydrographic surveyors, geospatial analysts, port and harbour engineers, environmental consultants, marine data specialists and coastal planners." He further states, "For our visitors, there will be new opportunities to discover cutting-edge solutions, connect with global experts and experience live demonstrations that will put them ahead of the curve in marine, coastal and shallow water innovation." Wide range of topics Prospective speakers are invited to submit their proposals by 30th September via the Oi26 website Oi26 has also announced its ‘Call for Content’, encouraging individuals and organisations to contribute to the event’s technical conference program by submitting papers across a wide range of topics. Prospective speakers are invited to submit their proposals by 30th September via the Oi26 website. Submissions will be reviewed by a panel of experts in the field and selected speakers will have the chance to present their ideas, research findings and case studies to a global audience of peers, stakeholders, and potential collaborators. Building on Oi’s commitment Ahead of visitor registration opening in November, there is an opportunity to register interest now by clicking on Take Part on the Oceanology website homepage. Oceanology International returns to London’s ExCeL from 10th to 12th March 2026, uniting more than 8,000 attendees and 500 exhibitors from across the globe. This year, the event expands its horizons with the debut of COAST, building on Oi’s commitment to connect the entire ocean and coastal community.
Sunderland Marine, part of global marine insurer - NorthStandard, has announced its contribution to the release of 'The Lifeboat', a stirring new single by Celtic music icons - Skipinnish, featuring renowned sea shanty group - The Fisherman’s Friends. The song is a tribute to two centuries of bravery by Royal National Lifeboat Institute (RNLI) volunteers, honouring their courageous service saving lives at sea under the most challenging conditions – including the North East shores. Sunderland Marine’s sponsorship Written by Skipinnish Co-Founder, lifelong fisherman and Sunderland Marine member, Angus MacPhail, 'The Lifeboat' reflects the selfless dedication of RNLI crews who are ready to respond to emergencies at a moment’s notice. Sunderland Marine’s sponsorship has been instrumental in supporting the production and promotion of this tribute, which will donate all proceeds to the RNLI. Sunderland’s own RNLI Lifeboat Station The connection is personal for Sunderland Marine, which has deep roots in the North East’s maritime community The connection is personal for Sunderland Marine, which has deep roots in the North East’s maritime community. Sunderland’s own RNLI Lifeboat Station is the oldest operational station in Great Britain, and has protected seafarers for over 200 years. Angus MacPhail said: "Having lived my life around the sea, I know firsthand the extraordinary dedication of lifeboat volunteers. Sunderland Marine’s support has been invaluable in bringing this tribute to life, helping us share the story of the selfless bravery that saves lives every day." Spirit of the maritime community Craig McBurnie, Head of Sunderland Marine, stated: "At Sunderland Marine, we are proud to support a project that celebrates the life-saving work of the RNLI and the spirit of the maritime community. This single reflects values we share, including courage, commitment, and a deep connection to the sea." He adds, "This sponsorship is part of an ongoing commitment to supporting the maritime and fishing industries, and the communities we serve." Regional maritime heritage The North East’s insurer is committed to supporting sustainability and safety in the sector, as demonstrated by its previous initiatives, such as backing the Whitby Lobster Hatchery and funding coastal fishing line recycling schemes, reinforcing its role as a responsible partner in regional maritime heritage. 'The Lifeboat' will be officially released on Thursday, 14th August, accompanied by a music video launch. The single will be performed live by Skipinnish and The Fisherman’s Friends at Skipinnish’s headline concert at Glasgow’s OVO Hydro on 27th September 2025.
Expert commentary
When the Ballast Water Management (BWM) Convention came into force in 2004, it was in response to a crisis we couldn’t afford to ignore—one where invasive aquatic species, carried silently in ships’ ballast tanks, were devastating marine ecosystems. Now, two decades later, compliance with this environmental safeguard is no longer optional—and yet, as recent industry findings reveal, record-keeping failures account for 58% of compliance issues. That’s not a technology problem. That’s a documentation problem —one rooted deeply in data management practices and crew training, where small oversights lead to documentation issues, that may cascade into costly compliance failures. And that’s precisely where digital systems excel, guiding crews clearly to avoid mistakes in the first place. New ballast regulations At the IMO’s 82nd Marine Environment Protection Committee (MEPC 82), new ballast water record-keeping regulations were approved, coming into effect from 1 February 2025. These updates mark a significant tightening of documentation standards—and they could catch unprepared shipowners off guard if not acted on promptly. Why ballast water record-keeping is back in the spotlight These new updates aim to change that—and they’re stricter, smarter, and more detailed than before While MEPC 82 made headlines for advancing decarbonisation policies and ECAs in the Arctic and Norwegian Sea, it also honed in on ballast water—a topic that has quietly regained importance. The committee approved critical updates to how ballast water operations and ballast water management system (BWMS) maintenance are recorded. The goal: Enhance transparency, reduce ambiguity, and reinforce environmental protection by making records more structured, traceable, and actionable. This renewed focus is both a warning and an opportunity. In recent years, too many Port State Control detentions and inspection delays have stemmed not from hardware failures, but from poorly maintained or unclear ballast water records. These new updates aim to change that—and they’re stricter, smarter, and more detailed than before. What’s changing: Bypass scenarios and maintenance logging The revised guidelines introduce two new scenarios for vessels dealing with challenging water quality (CWQ) in ports: Scenario 3: A reactive bypass of the BWMS due to unforeseen poor water quality. Scenario 4: A pre-emptive bypass based on anticipated CWQ conditions. These additions are essential for vessels operating globally, particularly those above 400GT. They ensure that alternative operations—like ballast water exchange plus treatment (BWE + BWT)—are clearly documented. Without accurate records, even legitimate actions can fall short of compliance. Ballast Water Management Plan and OEM manuals MEPC 82 also mandates that BWMS care procedures must now be recorded directly in BWRB MEPC 82 also mandates that BWMS maintenance procedures must now be recorded directly in the Ballast Water Record Book (BWRB), in line with the ship’s Ballast Water Management Plan and Original Equipment Manufacturer (OEM) manuals. Responsible crew members must sign off on these records, ensuring traceability and crew accountability. This step isn’t just regulatory housekeeping—it aligns ballast water maintenance with how other onboard systems are already tracked, from engines to emissions. It’s a logical, overdue move toward consistency across compliance. Paper or digital: The format dilemma While the BWRB can still be maintained on paper or electronically, the burden of new structured data fields and stricter reporting timelines will be felt most by those still tied to manual systems. Each additional layer of documentation increases the chance of human error—and with nearly 6 in 10 compliance failures already stemming from admin issues, that’s a risk many operators can’t afford. This is where digital solutions can offer real relief. At NAPA, we’ve already implemented the latest IMO guidelines into our electronic logbook, so crews can comply with MEPC.369(80) requirements out of the box. With ready-made entry templates and smart input validation, data entry is quick, accurate, and audit-ready. NAPA implemented the latest IMO guidelines into an electronic logbook. Better still, once updated, operators can apply for the BWM Convention Electronic Record Book Declaration from their flag—ensuring that compliance is recognised internationally under MEPC.372(80). Less admin, more assurance Electronic logbooks don’t just streamline compliance—they enable better decision-making. When connected to onboard systems, they automatically pull operational data into the BWRB, reducing manual work and error margins. This frees up the crew to focus on operations and safety, rather than paperwork. From a management perspective, real-time visibility into ballast operations and maintenance records helps shore teams stay ahead of inspections and identify potential compliance gaps early. One logbook, many regulations While ballast water is the focus today, it’s not the only regulation demanding attention While ballast water is the focus today, it’s not the only regulation demanding attention. At NAPA, we’ve designed our logbook to support a wide range of evolving compliance frameworks—including MARPOL, EU-ETS, EU-MRV, CII, and the Garbage Record Book. This unified approach removes silos, reduces duplicated effort, and gives operators a more holistic view of vessel performance and compliance. A smarter way forward With decarbonisation and environmental regulations shifting at breakneck pace, even the most experienced crews and fleet managers can struggle to stay up to date. That’s where technology has a crucial role to play—not to replace expertise, but to support it. At NAPA, we work closely with shipowners and operators to configure regulatory record book templates according to their fleet workflows and each vessel’s specific operational profile. This ensures accuracy, ease of use, and most importantly, continuous compliance—even as the rules keep changing. Because in today’s compliance landscape, staying ahead isn’t just about meeting the minimum. It’s about building systems that help you adapt, respond, and thrive. And that starts with getting the record-keeping and data management right.
President Donald Trump has already made plenty of headlines since taking up his second term in the White House, including with the announcement of numerous new tariffs on imports. The 47th United States President issued three executive orders on February 1st 2025, just days after his inauguration, which directed the US to impose an additional 25 percent ad valorem rate of duty on imports from Canada and Mexico, as well as ten percent on imports from China. How Trump’s 2nd term as US President Cleveland Containers has analysed the early reactions to these announcements Excluding Canadian energy resources exports – which instead will be hit with a ten percent tariff – the tariffs have been applied to all imports which are either entered for consumption or withdrawn from warehouse for consumption on or after 12:01 am Eastern Standard Time on February 4th 2025. President Trump also told reporters on February 8th 2025 that a 25 percent tariff on all American steel and aluminium imports was coming into effect across the US during February. Leading 40ft shipping container supplier Cleveland Containers has analysed the early reactions to these announcements and how President Trump’s second term as US President could affect the world’s shipping industry, especially when looking back at his first term. Reaction to President Trump’s tariff announcements Mexico, Canada and China were all quick to react to President Trump’s announcement of tariffs on imports. Mexican President Claudia Sheinbaum said her country would vow for resilience against the measures, while a senior government official in Canada said that their country would challenge the decision by taking legal action through the necessary international bodies. China has also said it would be challenging the tariffs at the World Trade Organisation. According to the country’s finance ministry, as reported on by Geopolitical Intelligence Services, Beijing were moving to place levies of 15 percent on American coal and liquefied natural gas, as well as levies of ten percent on crude oil, certain vehicles and farm equipment. Beginning of making America rich again When it comes to the announcement of the tariff on all American steel and aluminium imports, President Trump told reporters in the Oval Office: "This is a big deal, the beginning of making America rich again. Our nation requires steel and aluminium to be made in America, not in foreign lands.” Francois-Phillippe Champagne, the Minister of Innovation in Canada, stated that the tariffs were "totally unjustified" though, before adding in a post on X: "Canadian steel and aluminium support key industries in the US, from defence, shipbuilding and auto. We will continue to stand up for Canada, our workers, and our industries." How might President Trump’s 2nd term affect shipping sector? Bruce Chan, an analyst in the Transportation and Future Mobility sectors at wealth management and investment banking Just ahead of President Trump taking office for the second time, J. Bruce Chan, an analyst in the Transportation and Future Mobility sectors at wealth management and investment banking firm Stifel, believed that the shipping industry was prepared for the new tariffs. However, he also stated to the Morning Star: "President Trump's Administration promises to usher in a new trade and tariff regime. As such, it's difficult to assess the ultimate impact to the freight transportation industry. Prima facie, we believe tariffs are a drag on freight demand, effectively resulting in higher costs for shippers that are generally passed on to end consumers over time." Attention to the American sanction announcements Mr. Chan went on to note that those involved in shipping containers across continents should be paying particular attention to the American sanction announcements. He commented: "Because almost all trans-Pacific trade moves over the ocean, we believe ocean container shipping will see the largest direct impact. But for shippers and retailers, there is no cheaper way to move goods than over the ocean, so there are few modal alternatives if production remains in Asia. We see the most risk for maritime shipping, with containers and dry bulk being more acute, with more insulation for oil and gas tankers." Shipping news and intelligence service Various sources have looked back on President Trump’s first term to get an idea of what could be expected As President Trump has just become his second term as US president and the American sanctions have only just been announced, it will take time to see what the true impact will be. However, various sources have looked back on President Trump’s first term to get an idea of what could be expected. For example, shipping news and intelligence service Lloyd’s List pointed out that tariffs introduced when President Trump was last in the White House had a noticeable effect on both spot container freight rates and import timing. Cargoes were pulled forward in the second half of 2018 by importers as they looked to beat tariff deadlines, which resulted in higher spot rates temporarily before affecting rates in 2019 because of inventory overhang. Could repeat results be seen across 2025 and 2026? Long-life inputs and goods from the tariff countries Jason Miller, a freight economist and professor of supply chain management at Michigan State University, certainly seemed to think so. Speaking to Lloyd’s List before President Trump’s 2024 presidential victory when the tariffs were only part of campaign proposals at that point, he said: “We will see front-loading like we have never seen before in 2025. There would be a massive pull-forward of demand as everybody rushes to bring in long-life inputs and goods from tariff countries, especially China.” Shipping demand and routes Shipping demand and routes could be affected due to trade uncertainty too Meanwhile, international shipping and forwarding agents Supreme Freight Services reported that increased tariffs may cause disruption to shipping volumes and global supply chains, if trade policies introduced by President Trump during his first term are anything to go by. Shipping demand and routes could be affected due to trade uncertainty too, though the publication also acknowledged that increased investment in ports and inland waterways across the US could improve efficiency for domestic and international trade alike. New American sanctions Cleveland Containers has looked to reassure its customers that any disruption caused by the new American sanctions will be minimised at the firm. Hayley Hedley, the company’s Commercial Director, stated: “Recent history certainly suggests that the new tariffs being introduced by President Trump will have various knock-on effects across the shipping industry." “Fortunately, Cleveland Containers has a continuous supply of shipping containers entering the UK. We work with several agents to ship from various locations, as well as having good stock on the ground, so are confident in our ability to provide for our customers.”
The shipping industry is currently navigating a profound transformation driven by environmental concerns, new emissions targets, and evolving regulations. As vessel owners and operators seek to reduce emissions while remaining competitive, determining the right strategy has become increasingly complex. Factors such as alternative fuel availability, fluctuating prices, and an ever-expanding range of technological solutions have made decision-making anything but straightforward. Lack of motivation Regulations evolve, technologies persist to advance, and can differ greatly from port to port The complexity arises from the many moving parts of the industry. Regulations evolve, technologies continue to advance, and infrastructure can differ greatly from port to port. For vessel owners committed to reducing their environmental impact, the challenge isn’t a lack of motivation, it’s finding the most effective way to navigate the myriad of options available. Hybrid propulsion systems One method gaining traction is data-driven decision-making through digital modelling. Rather than making decisions based on guesswork, digital modelling allows owners and operators to create a detailed representation of a vessel and simulate the performance of different strategies or technologies over its lifetime. That way, they can ‘test’ these approaches before committing large investments—particularly useful when considering new fuels or hybrid propulsion systems that are still maturing. Decarbonisation Modelling Service Digital modelling accounts for variables such as vessel speed, power needs, and route patterns Digital modelling accounts for variables such as vessel speed, power needs, and route patterns, applying machine-learning algorithms to find the most promising design or retrofit. It can also show how ideas might evolve if regulations tighten, or new fuels become more practical. At Wärtsilä, our Decarbonisation Modelling Service is designed to guide shipowners and operators through this maze of choices. In developing this tool, we have observed that shipowners required more than an “off-the-shelf” solution. They needed insights based on their own operational data, combined with practical knowledge of costs and likely regulatory trends. Benefits of digital modelling One of the main benefits of digital modelling is its flexibility. Depending on an owner’s goals, whether that’s meeting today’s regulations or planning for future mandates, they can explore multiple options. A fleet operator might compare installing hybrid batteries versus retrofitting for LNG or consider alternative fuels such as ammonia and methanol, or carbon capture. These simulations can factor in fuel prices, available bunkering infrastructure, and even unexpected events like global supply chain disruptions or future carbon taxes. Ship’s actual operational profile At Wärtsilä we often liken digital modelling as the closest thing to a crystal ball At Wärtsilä we often liken digital modelling as the closest thing to a crystal ball. While it isn’t perfect, it significantly improves our ability to make informed decisions and maintain flexibility as market conditions or regulatory landscapes shift. Consider, for instance, a mid-sized container ship operating in Asia. The owner, eager to lower CO2 emissions, might be unsure whether to retrofit for LNG immediately or wait for ammonia infrastructure to mature. Using a digital model based on the ship’s actual operational profile, we can test both scenarios—evaluating fuel price trends, port facilities, and the vessel’s remaining service life. Adopt an interim strategy If the model indicates that an LNG retrofit offers a promising return on investment along with moderate emissions cuts, the decision becomes clearer. Alternatively, if the potential for ammonia becomes evident sooner, it might be wiser to adopt an interim strategy or consider dual-fuel engines. It’s important to recognise that decarbonisation is not merely a box-ticking exercise to meet current regulations; it is a dynamic, ongoing process. With tightening rules from bodies like the International Maritime Organization (IMO) and the EU on carbon intensity, and with cargo owners increasingly demanding transparency, the need for adaptive, data-driven solutions is more critical than ever. LNG with battery storage Others might make quick retrofits to comply with rules and plan for bigger upgrades later Another strength of data-driven decarbonisation is that it is not a one-off activity. As a vessel operates, new information becomes available. Owners can update their models to reflect these shifts, allowing for continuous refinement. This matters because what is optimal now may only be a temporary measure. Some operators use LNG with battery storage for a few years, then switch to next-generation fuels as they become viable. Others might make quick retrofits to comply with regulations and plan for bigger upgrades later. Raw data into actionable insights There is also a perception that gathering and interpreting data is too complex or costly. However, many modern vessels are already equipped with the necessary sensors and tracking systems, and analytics software has become more accessible. The real value lies in transforming raw data into actionable insights. Digital models not only help in planning for evolving market conditions but also enable us to visualise and execute long-term strategies. Portion of global CO2 emissions The real test is balancing environmental aims with retail realities and regulatory forces Shipping contributes a notable portion of global CO2 emissions, giving the industry strong financial and ethical reasons to embrace cleaner operations. The real test is balancing environmental aims with commercial realities and regulatory pressures. With mounting pressure from regulators, customers, and investors, now is an opportune time to adopt data-driven approaches. A continuously updated model provides a practical way to keep up with changes in the market and policy landscape. By integrating operational data, anticipating possible scenarios, and remaining open to new solutions, the maritime industry can cut emissions without sacrificing competitiveness. Shipowners and operators Shipping is an industry that operates on tight margins and these tools must deliver financial stability as well as ongoing compliance. Digital modelling is not just another technical tool; it’s a forward-looking process that helps shipowners and operators steer a confident course in uncertain waters. As more companies experiment with alternative fuels, hybrid propulsion, and emerging technologies, having a robust method for evaluating these options is absolutely essential.
Harbour insights
Ballast Water Management Systems (BWMS) prevent the spread of invasive aquatic species, which pose significant ecological, economic, and health threats. The systems treat and purify a ship's ballast water before it is discharged into a new environment. Regulations dictate how ballast water is managed and discharged. The IMO Ballast Water Management Convention was adopted in 2004 and ratified on 8 September 2017. In addition, the U.S. Coast Guard (USCG) has also regulated discharges in the USA through local regulations in conjunction with the EPA. Risk of undesirable bio-invasions All ships of 400 gross tons (300 gt for USCG) or more are required to manage their ballast water All ships of 400 gross tons (300 gt for USCG) or more are required to manage their ballast water. A range of technologies have been Type Approved to purify a ship's ballast water, and treatment methods are dominated by those making use of active substances or UV radiation. Ballast Water Treatment Systems (BWTS) remove or render harmless nonindigenous aquatic species and pathogens before the ballast water is discharged into a new location. Therefore, BWTS provide ships the means to comply to the regulations and reduce the risk of undesirable bio-invasions that harm ecosystems, and cause economic and coastal infrastructure damage, according to Dr. Stelios Kyriacou, Chief Technology Officer (CTO) of ERMA FIRST, a manufacturer of ballast water treatment and other sustainable marine equipment systems. BWTS remove or render harmless nonindigenous aquatic species and pathogens. Leadership in the core product category “We have already achieved leadership in our core product category, the Ballast Water Treatment Systems, and our vision remains for our new chapter, the decarbonisation solutions,” says Kimon Mademlis, Group Marketing and Communications Director, ERMA FIRST. “This is the brand promise to our customers that we will always strive for excellence, innovation and stellar offerings.” Flexible and adaptable ballast water management Use of active substance treatments offers a flexible and adaptable ballast water management system ERMA FIRST has developed a full flow filter electro-chlorination system, ERMA FIRST FIT BWTS, and has further expanded its product offering with the acquisition of complementary chemical injection technologies, oneTANK and Ecochlor, for ballast water management. The use of active substance treatments offers a flexible and adaptable ballast water management system to marine operators, says Kyriacou. Electro-chlorination and chemical injection treatments are single pass on ballasting only, unlike UV where a secondary treatment is required at discharge. Ballast water treatment systems Active substance treatments are not impacted by water clarity (UV transmittance) and adapt to water quality challenges better than UV systems while in general have a lower operating expense and energy footprint. ERMA FIRST ensures operational simplicity and lowers costs with their user-friendly ballast water treatment systems. Designed for easy installation and basic crew training, the systems feature automated operation that reduces manual work and ensures compliance with international regulations. Their flexible design fits all vessel types, minimising downtime and retrofit expenses. ERMA FIRST ensures operational simplicity and lowers costs with its user-friendly BWTS. ERMA FIRST global service ERMA FIRST offers global service and remote support, improving system efficiency With low energy consumption and simple maintenance needs, the systems help shipowners reduce daily operational costs while ensuring reliable long-term performance. In addition, ERMA FIRST offers global service and remote support, improving system efficiency and making vessel operations smoother, more reliable, and cost-effective across the fleet. Combining products and services to support customers ERMA FIRST provides a range of services to support customers from the initial sales to long-term operation. The company offers expert advice, system design, and, when requested, assistance during installation to ensure the best fit for each vessel’s needs. They also provide crew training for safe and straightforward operation. Maintenance services, both scheduled and on demand, keep systems running efficiently. With remote monitoring, 24/7 technical support, and service engineers worldwide, ERMA FIRST responds quickly to any issue. “We supply spare parts upon request or as needed, and we maintain stock in major hubs globally,” says Mademlis. “ERMA FIRST ensures reliable, simple, and cost-effective support at every stage.” ERMA FIRST provides a range of services to support customers from the initial sales. New sustainable and reliable products Customers drive the business, while R&D provides new sustainable and reliable products ERMA FIRST’s vision is to be a pioneer in the industry excellence in all they do. Customers drive the business, while R&D provides new sustainable and reliable products and after-sales service delivers customer support. Here is the brand’s purpose statement: “Saving the oceans to safeguarding the planet.” ERMA FIRST is committed to a greener future, a sustainable world, and a bright tomorrow for the generations to come. Expanding range of decarbonisation solutions ERMA FIRST’s track record in ballast water treatment systems, as well as with other marine equipment such as oily water separators and sewage treatment plants, has critically and crucially delivered towards protecting the oceans. The BWTS ensures optimal protection of the seas, and the company offers an expanding range of decarbonisation solutions. “In the maritime sector, technological advancement is driving a major transformation across operations, sustainability, and competitiveness,” says Kyriacou. “We are responding to growing environmental concerns and regulatory pressures, particularly from the International Maritime Organization (IMO), for greenhouse gas (GHG) reduction, decarbonisation and net-zero.” Environmental policy developments ERMA FIRST maintains active R&D programs and invests in energy efficiency measures ERMA FIRST monitors environmental policy developments and adapts and leverages their resources to the develop practical and cost-effective solutions for global shipping. “Our core strategic objectives include sustainability and environmental respectability with a strong desire to maximise our customers’ benefit and support their strategies to achieve carbon neutrality,” says Mademlis. To this end, ERMA FIRST maintains active R&D programs and invests in energy efficiency measures, air lubrication systems (AL) and wind-assisted propulsion systems (WAPS), ship-to-shore power interface, advanced data analytics, and artificial intelligence (AI) to optimise ship operations, performance, and emissions in real-time. ERMA FIRST maintains active R&D programs and invests in energy efficiency measures. Use of diesel electric generators and boilers Decarbonisation measures target ship propulsion with fuel and energy efficiency improvements Decarbonisation measures mainly target ship propulsion with fuel and energy efficiency improvements. Ships, however, also spend time in port where they engage in passenger and cargo operations, while the energy requirements are significantly lower than when in transit. The use of diesel electric generators and boilers in port is responsible for the continued emission of GHG and particulate matter (PM) in the atmosphere and is a major cause of noise pollution. The health and wellbeing of residents in the vicinity of ports is impacted by ship operations. Reducing carbon footprint, lowering costs The use of Alternative Maritime Power systems, like BLUE CONNECT from ERMA FIRST, enables ships to stop running their generators in port and utilise shore power for their needs, thus saving fuel, reducing the environmental and carbon footprint of cargo operations. “The adoption of energy-efficiency measures targets reduction of GHG emissions, optimisation of fuel use, and correcting the energy performance of suboptimal ship designs,” says Kyriacou. ERMA FIRST’s energy-saving devices (ESDs) maximise the propulsive effectiveness of the propeller. ERMA FIRST’s ESDs maximise the propulsive effectiveness of the propeller. Combinations of ESDs FLEXCAP eliminates the hub vortex, while converting some of the rotational energy to thrust FLEXCAP, a propeller cap, eliminates the hub vortex, while converting some of the rotational energy to thrust. FLEXFINS are attached to the hull to correct the flow around the stern preventing boundary layer separation thus reducing drag and losses. FLEXRING is a duct fitted upstream of the propeller that homogenises the axial wake component, while the duct contributes to the thrust by virtue of the lift generated by the accelerating flow over the surfaces. Combinations of ESDs can deliver significant performance gains, lower fuel consumption, reduce GHG emissions and improve a ship’s carbon intensity indicator (CII), says Kyriacou. Embracing carbon capture and storage Carbon capture and storage systems have an important role to play during the transition away from fossil fuels to achieve net-zero. Fossil fuels will be the energy source for ships’ propulsion in the near term because the shift to alternative fuels cannot be implemented instantly due to availability and capacity constraints. ERMA FIRST recognises the need to provide a bridge solution between continued fossil fuel use and the necessity to reduce GHG emissions radically. ERMA FIRST recognises the need to provide a bridge solution. Development of a regulatory framework The ERMA FIRST CARBON FIT post-combustion on-board carbon capture and storage (OCCS) system provides a technically practical solution to achieve GHG emissions reduction, paving the pathway to carbon neutrality. At IMO MEPC.83, a work plan on the development of a regulatory framework for the use of OCCS was agreed. With a scheduled completion by 2028, it is projected that broad technology implementation will follow. ERMA FIRST CARBON FIT post-combustion on-board carbon capture and storage. Maritime and environmental awards As a technology provider with a global reach, ERMA FIRST sets high standards of quality on both equipment and services. ERMA FIRST has won multiple maritime and environmental awards over the years, including: Technical Achievement Award 2013, Lloyd's List Greek Shipping Awards Technology Excellence 2013, Made in Greece Technology Award 2016, GREEN4SEA Bronze Award 2022, HR Awards Technical Achievement Award 2023, Lloyd's List Greek Shipping Awards Sustainability Award 2023, GREEN4SEA Bronze Award 2023, HR Awards Greek Business Champion 2023, Protagonistes Business External Focus 2023, Protagonistes Great Place to Work 2023 R&D expertise of ERMA FIRST A milestone for the company and a proud achievement is the fact that ERMA FIRST belongs to a very small group of companies having won the Technical Achievement Award by Lloyd's List more than once. This reflects the solid R&D expertise of ERMA FIRST and the long-standing and ongoing efforts towards technological excellence and impactful innovations.
FuelEU Maritime came into effect on Jan. 1, 2025. It is part of the European Union’s Fit for 55 package and applies to commercial vessels of 5000GT (gross tonnage) and over used for the transport of cargo or passengers and calling at EU ports. Vessels are required to achieve a greenhouse gas (GHG) intensity of energy below a particular level. That level reduces over time and by 2050 the reduction target is 80% compared to 2020 reference levels. GHG intensity of energy obligations “FuelEU is designed to reduce the energy intensity of fuel used by ships and to drive the uptake of alternative fuels,” says Helen Barden, Director – External Affairs, NorthStandard, an insurer providing Protection and Indemnity (P&I) coverage. She adds, “For vessels that do not meet the GHG intensity of energy obligations, there are options for borrowing compliance from future years, pooling the vessel with better-performing vessel(s) or paying a penalty. For container and passenger ships there are requirements to connect to shore power from 2030.” Ship’s energy intensity FuelEU Maritime measures a ship’s energy intensity over a full reporting year on a well-to-wake basis FuelEU Maritime measures a ship’s energy intensity over a full reporting year on a well-to-wake basis. Well-to-wake therefore includes emissions from well (i.e., production) to tank (i.e., on the ship) plus tank-to-wake (i.e., it propels the ship). Assessing the energy intensity on a well-to-wake basis, rather than simply tank-to-wake, provides a better reflection of the emissions created during the lifecycle of a marine fuel. Wind-assisted propulsion systems “There are many energy efficiency technologies on the market, such as improving the efficiency of hull coatings, or making changes to the bulbous bow or propeller, but these go to improving the energy efficiency and are not included in the calculation to improve the energy intensity of the fuel used,” says Helen Barden. However, wind-assisted propulsion systems receive a Wind Reward Factor in the regulation, which means this technology does impact the vessel’s GHG intensity rating. Of course, zero or near zero fuels and renewable fuels of non-biological origin also go to the GHG intensity rating. Compliance of FuelEU The compliance of FuelEU rests with the DOC holder under the ISM code While the compliance of FuelEU rests with the Document of Compliance (DOC) holder under the International Safety Management (ISM) code, which may well be the ship manager rather than the registered owner, the ship manager will in reality want to pass the liability for compliance on to the ship owner, says Barden. The ship owner (and indeed possibly together with the charterer depending on the length of the charter party and nature of the commercial relationship) will need to produce a strategy for compliance with FuelEU Maritime given there are different options for compliance available, she says. Lower energy intensity fuels and energy sources Helen Barden says payment of the penalty should be the last resort. “Not only is this likely to be the most expensive option, but it also comes with implications for future years in the form of a multiplication factor,” she states. Helen Barden adds, “Whether pooling, using lower energy intensity fuels and energy sources, or borrowing compliance from future years as part of a strategy will depend on many variables and, therefore, a compliance strategy should be given considered thought. This will also impact on the terms of any contracts.” Respect of GHG energy intensity Financial penalties apply to any company that does not meet its compliance obligations There are pooling platforms on the market now, such as Bettersea, which is currently offered to NorthStandard members at a preferential rate. Financial penalties apply to any company that does not meet its compliance obligations in respect of GHG energy intensity. Failing to comply for two or more consecutive years will see the penalty factor multiplied, while failure to present a FuelEU Maritime certificate of compliance for two or more consecutive reporting periods could result in a ship being banned from EU ports. Vessel’s compliance balance If a vessel exceeds the compliance requirements and so has a positive compliance balance for a reporting period, this “surplus” can either be pooled or can be banked for compliance in future years. Parties will need to consider whether charterers will get the full benefit of compliance pooling, banking or borrowing, and how this will work where the charter party does not cover the full reporting year. A vessel’s compliance balance may not be included in more than one pool in the same reporting period, but the vessel may be switched to a different pool in a different reporting period. Responsibility for FuelEU compliance rests The ultimate responsibility for FuelEU compliance rests with the ISM company The ultimate responsibility for FuelEU compliance rests with the ISM company (i.e., the Document of Compliance holder under the ISM Code) and, therefore, careful consideration must be given to the contractual implications of FuelEU Maritime. The Baltic and International Maritime Council (BIMCO) has produced a FuelEU Maritime Clause for Time Charter Parties and a Clause for ship management agreements, too, to help support owners, charterers, and ship managers in this regard. However, these clauses cannot just be inserted without consideration. As mentioned earlier, things like the compliance strategy should be thought through as this will impact the wording used in the clause, says Barden. Advice on the BIMCO clause “The BIMCO clauses are certainly a helpful starting point, but ship managers, ship owners and charterers must consider the terms carefully and, if necessary, make amendments,” says Helen Barden. She adds, “We have been assisting a number of our members with advice on the BIMCO clause in their particular circumstances, and indeed non-industry clauses that have also been proposed.”
Traditionally, bulk cargo unloading has faced challenges around operational efficiency, safety risks, environmental impacts, and high operational costs. Rough discharges, equipment wear, vibration damage, and limited weather operating windows have all constrained vessel utilisation and performance. Moreover, older unloading systems are energy-intensive and labour-dependent, increasing both costs and environmental footprint. Cargo unloading systems Many bulk cargo unloading systems depend on steep slope angles, which limit the types of materials that can be carried efficiently. MacGregor’s GravityVibe directly addresses this factor by allowing efficient discharge with significantly lower slope angles, thus broadening the range of cargo that can be handled. Many bulk cargo unloading systems depend on steep slope angles. Ship structures and unloading equipment “GravityVibe reduces reliance on gravity alone by augmenting the flow with controlled vibration,” says Mikael Hägglund, Senior Manager, Cranes at MacGregor. “This approach improves operational efficiency, enhances safety through more predictable material flow, and reduces wear on ship structures and unloading equipment.” Challenges of space utilisation and cargo versatility MacGregor is a provider of cargo and load handling solutions to maximise efficiency Additionally, the GravityVibe system will, in most cases, require only one hold conveyor and no cross conveyor in the hold, making the operations both cost-effective and sustainable, says Hägglund. MacGregor, based in Helsinki, Finland, is a provider of cargo and load handling solutions to maximise efficiency of maritime operations. As an augmented gravity self-unloading system, GravityVibe enhances cargo flow using vibration, enabling bulk materials to be discharged efficiently at lower slope angles (15–20 degrees). It reduces material blockages and optimises discharge without requiring steep holds, addressing the challenges of space utilisation and cargo versatility. Mechanical strain on vessel structures The system lessens mechanical strain on vessel structures, and supports safer, smoother, and more efficient operations across different cargo types. “Using lower slope angles allows ships to maximise cargo hold volume and transport a wider variety of bulk materials, including those that would not flow well with conventional systems,” says Hägglund. “It improves operational flexibility.” Integrity of the vessel Vessels benefit from a more compact and efficient hold design, optimising stability and construction Structurally, vessels benefit from a more compact and efficient hold design, optimising stability and potentially lowering construction and maintenance costs, adds Hägglund. “Managing vibration and sound levels is critical for maintaining the structural integrity of the vessel and ensuring crew safety and comfort,” he says. “Excessive vibration can lead to accelerated wear on ship components and fatigue damage over time.” GravityVibe’s design GravityVibe’s design ensures that both vibration and sound levels stay well below class-defined thresholds, preserving vessel longevity and reducing long-term maintenance and repair costs. Bulk cargoes have widely varying properties such as particle size, cohesiveness, moisture content, and chemical reactivity, all of which impact flow behaviour. Sticky, wet, or coarse materials require different unloading strategies to avoid blockages, segregation, or structural strain. Bulk cargoes have widely varying properties like particle size and cohesiveness. Broader spectrum of cargo types Key elements to achieve automation include fine-tuning self-optimisation algorithms GravityVibe’s vibration-driven approach adapts to these material differences, maintaining consistent discharge rates and ensuring operational reliability across a broader spectrum of cargo types without manual intervention or excessive mechanical modification, says Hägglund. More automated systems are on the horizon. Fully automated discharge is rapidly approaching reality, thanks to intelligent unloading systems like GravityVibe. Key remaining elements to achieve automation include fine-tuning self-optimisation algorithms, integrating predictive maintenance solutions, and standardising automation interfaces between vessels and ports. GravityVibe features MacGregor is actively working to refine onboard software, improve material recognition capabilities, and enhance real-time adjustment features. Wider industry adoption and regulatory frameworks are also crucial for achieving fully autonomous and seamless bulk unloading. GravityVibe features a built-in self-optimisation system that uses sensors to monitor material flow characteristics during discharge. Based on live data, it automatically adjusts vibration frequency and intensity to match the properties of each specific cargo, ensuring optimal unloading performance without manual recalibration. MacGregor is working to refine onboard software and improve material recognition. GravityVibe’s performance GravityVibe’s performance has been verified through a combination of laboratory studies MacGregor is fine-tuning this system by gathering real-world data from full-scale test rigs, analysing operational performance across various cargo types, and incorporating feedback loops to continually improve discharge efficiency and system responsiveness. Real-world validation is essential to prove that unloading systems perform reliably under operational conditions. GravityVibe’s performance has been verified through a combination of laboratory studies and full-scale rig testing. In-house tests and studies For example, validation by bulk solids researcher TUNRA showed efficient unloading across diverse materials such as wood chips, manufacturing sand, and gravel. In-house tests and studies with external specialists like KTH have confirmed low vibration levels, consistent discharge flow, and high operational reliability, providing strong evidence for commercial deployment. TUNRA showed efficient unloading across diverse materials such as sand. GravityVibe’s system design GravityVibe’s system design is based on long-lasting parts and improved cargo flow High maintenance requirements traditionally have led to significant downtime and increased operational costs. GravityVibe’s system design is based on long-lasting components and improved cargo flow that reduce risks for failures and needed service, thereby lowering maintenance costs/needs. “With real-time monitoring and smart diagnostics, potential issues can be detected and addressed before they escalate, minimising service interruptions,” says Hägglund. “This proactive approach enhances equipment availability and ensures better operational continuity for vessel operators.” MacGregor GravityVibe system When unloading standard bulk carriers, there is a need to clean the holds with manpower and external machines as the port cranes or the vessel cranes will not be able to empty the holds. The weather could also be a factor for delay in cases where the cargo is sensitive to water. For the MacGregor GravityVibe system, all material will be removed from the hold without any extra efforts. GravityVibe demonstrates that with intelligent use of vibration and lower slope angles can achieve the same — or even better — results. This approach not only enables broader cargo flexibility but also reduces structural stress, energy consumption, and environmental footprint.
Case studies
Höegh Autoliners has revolutionised maritime transport with its Aurora Class vessels, marking significant progress toward sustainable deep-sea shipping. These Pure Car and Truck Carriers (PCTCs) are designed to be the largest and most environmentally friendly in their class. Notably, the final four ships in this 12-vessel series are set to operate on sustainable ammonia, a zero-carbon fuel, upon their delivery in 2027. Aurora Class vessels Aurora Class vessels are initially running on LNG with the flexibility to transition to ammonia and methanol The Aurora Class vessels are initially running on liquefied natural gas (LNG) with the flexibility to transition to ammonia and methanol as these fuels become more accessible. This adaptability is emphasised by the ships’ receipt of DNV’s ammonia- and methanol-ready notations, a first in the PCTC segment. The final four vessels will feature MAN Energy Solutions’ two-stroke engines capable of being fuelled by ammonia, positioning them as pioneers in zero-GHG emission maritime transport. TGE Marine’s expertise A key enabler of this technological leap is TGE Marine, whose advanced tank designs and fuel gas handling solutions are at the core of the vessels’ ammonia propulsion capabilities. TGE Marine’s expertise in designing and engineering maritime gas systems has made them a global pioneer in gas containment and fuel supply technologies. Their tanks are specifically developed to safely store ammonia in maritime conditions, while their fuel gas systems are among the most advanced in the industry ensuring reliable fuel management, safe operations, and seamless engine integration. These solutions exceed the stringent safety and performance standards required for ammonia as a marine fuel. New ammonia fuel supply system TGE Marine has already supplied tanks and fuel gas systems to the first eight Aurora class vessels TGE Marine has already supplied tanks and fuel gas systems to the first eight Aurora class vessels, and within the final four vessels, the fuel supply system is intended to handle ammonia fuel which allow for the vessels to be an engineering front runner in the industry. The new ammonia fuel supply system comes among others with a reliquefaction system, a gas combustion unit (GCU) and an ammonia release and mitigation systems (ARMS). Aspects of TGE Marine’s contribution The following expands on the specific aspects of TGE Marine’s contribution to the vessels: Fuel Supply System: The fuel supply system is streamlined to support the main engine operation in an optimum manner allowing a reliable and stable operation with ammonia as fuel. The design of the system is addressing the demand to increase ammonia integrity and to allow safe operation incl. maintenance. Key design features are the utilisation of sealless pumps, high integrity equipment and automation resp. remote operation. Boil-off Gas (BOG) Treatment: The heat ingress into the ammonia storage tank will lead to evapouration of ammonia. To keep the tank pressure within allowable limit the vapour, the BOG, is routed from the type-c tank’s vapour space to the BOG Treatment System. The BOG Treatment system consists of two fully independent methods to manage the tank pressure, i.e., the Reliquefaction System and the Gas Combustion Unit (GCU). Reliquefaction System: Onboard reliquefaction systems are engineered to recondense the ammonia vapour that results from heat ingress into the storage tanks and system operation. Gas Combustion Unit: As with all systems, TGE Marine also ensure that in an unlikely event that the reliquefaction system would fail, a secondary ‘back up’ system would kick in. The method chosen for this set up a gas combustion unit (GCU). This method burns the boil off gas, and this allows the tank temperature and tank pressure to remain within the limits. The gas combustion unit can support also the treatment of nitrogen ammonia mixtures and non-standard operations, such as gas-freeing of systems for maintenance preventing the release of ammonia to the atmosphere. Safety Systems: Key for operating a vessel with ammonia as fuel is the safe operation taking the toxicity of ammonia into consideration. TGE Marine has implemented safety systems and measures into the design of the system. Risk assessments accompany the design and execution of the project at every stage. Ammonia recovery: A key element of the safe operation is the handling of potential operational and emergency releases originating from the fuel supply system and engine purge operations. For this purpose, an ammonia recovery system is applied to reduce the ammonia quantities being routed to the ammonia release mitigation system. Ammonia Release Mitigation System: The ammonia release mitigation system developed by TGE Marine, is reducing the ammonia quantity released to the atmosphere and ensures that ammonia concentrations are below health and safety limits. Primary benefits of configuration To underline the benefits of the system, these following can be listed as primary benefits of using such configuration: Fuel Efficiency: By applying an efficient ammonia fuel supply system and ammonia engine Environmental Compliance: Minimising emissions of ammonia gas into the atmosphere reduces the vessel’s environmental footprint and helps comply with stringent emissions regulations Safety and Stability: The system ensures stable operation, reducing the risk to personnel and enhancing onboard safety Operational Flexibility: This technology supports extended voyages without fuel losses and allows better management of varying fuel demands during different operational profiles New standard for sustainability in maritime transport Beyond propulsion, the Aurora Class vessels incorporate several eco-friendly features, some include 1,500 square metres of solar panels and the capability to connect to electric shore power, enabling emissions-free port operations. With these advancements, Höegh Autoliners, together with key partners like TGE Marine, is not only reducing its carbon footprint but also setting a new standard for sustainability in maritime transport, steering the industry toward a greener future.
Team Electric rose to some special challenges in its successful completion of electrical installation and refit work during Royal Caribbean’s recent high profile drydocking and ‘amplification’ of Allure of the Seas. Despite heavy weather, tight deadlines, and complex coordination across multiple contractors and workstreams, Team Electric showcased its hallmark adaptability and technical expertise to deliver the full scope of work on schedule. Three turnkey suppliers With a total workforce of 60 skilled electricians on site, Team Electric was engaged separately by three turnkey suppliers — Almaco, Makinen, and LMG — to execute electrical works across hotel areas, galleys, and public spaces on board the cruise ship. The project marked a return to familiar territory for Team Electric, which was also involved in the original construction of Allure of the Seas in Turku Shipyard in 2009. Project highlights Team Electric delivered full electrical works for the new Mason Jar restaurant and bar Achievements included the installation of 121 kilometres of electrical cabling and 4,500 metres of cable trays, across a project involving key technical areas as well as substantial hotel work. Among tasks that extended to 600 individual material line items, Team Electric fitted nearly 2,000 lights. The company’s hotel-side scope covered 61 new cabins on decks 11, 12, and 14 that were built within a prefabricated aluminium block and craned onto the ship. These new spaces included corridors, AC rooms, and associated technical infrastructure. In addition, Team Electric delivered full electrical works for the new Mason Jar restaurant and bar, as well as several refurbished galley spaces and three public areas including a Crown Lounge and a teens’ gaming zone. On the technical side, Team Electric upgraded a substantial portion of the ship’s navigation and communication systems, including the full cabling of the bridge with 9 kilometres of new wiring. A turnkey delivery of Fugro’s OceanStar system included not just cabling but also installation, commissioning, and user training, led by certified Team Electric engineers. Rising to the challenge “The weather was brutal. 30 days of torrential rain in a 40-day dry dock,” said Daniel Brown, Project Manager at Team Electric. “It had a knock-on effect on every trade, but we managed to push through and keep the program on track.” Meticulous planning and on-the-ground flexibility, Team Electric met all critical deadlines High winds frequently delayed crane operations and other key activities. Yet, through meticulous planning and on-the-ground flexibility, Team Electric met all critical deadlines. The project’s compressed dry dock period presented a further challenge. As Caj Persson, Technical Project Lead, explained: “They cut the dry dock time compared to the sister vessel Oasis of the Seas by over 10 days. That meant everything had to be done faster, with no compromise on quality.” Reliability pays Team Electric’s proven reputation in cruise ship refits was a key factor in securing the contract. “We’re well known in the industry for delivering complex and multi-faceted electrical refits, especially cabins and public areas,” said Daniel Brown. “We’re not always the cheapest, but clients know we get the job done on time and to the highest standards.” Fourth contractor with no onboard electrical team asked Team Electric to step in and support their work That reliability also paid off during the refit, when a fourth contractor with no onboard electrical team asked Team Electric to step in and support their work, sparking another relationship that is set to continue beyond this project. The working relationship with Royal Caribbean also proved crucial. “We know the fleet, we’ve been with them since these keels were laid,” said Persson. “That familiarity, and our long-standing relationship with partners like Foreship, made the coordination smoother, even under pressure.” Integrated installation Unlike newbuilds, refits present constantly shifting priorities and constraints. As Daniel Brown explained: “In public areas especially, we can’t even install light fittings until the ceiling is in. It takes extreme coordination. Every task affects the next.” From cabin design to bridge cabling, and from substations to galleys, the Allure of the Seas project exemplifies Team Electric’s full-spectrum capabilities. By blending technical know-how with practical execution, the company once again proved why it's the preferred electrical partner for cruise ship refits worldwide.
San Francisco-based maritime technology company - Sofar Ocean announces a partnership with the U.S. Naval Meteorology and Oceanography Command’s (CNMOC) Fleet Weather centres in Norfolk (FWC-N) and San Diego (FWC-SD). Wayfinder platform FWC-N and FWC-SD, the Navy’s two primary weather forecasting centres, are piloting Sofar’s Wayfinder platform to support the routing of naval vessels at sea. The FWCs are utilising Wayfinder to identify safe and efficient route options powered by real-time ocean weather data for Military Sealift Command (MSC) ships. Situational awareness Tim Janssen, Co-Dounder and CEO of Sofar, said, "Wayfinder will empower the Navy to enhance situational awareness at sea and leverage data-driven optimisation to continuously identify safe and efficient routing strategies." He adds, "Powered by our real-time ocean weather sensor network, Wayfinder will help the Navy scale its routing operations to support a heterogeneous fleet operating in conditions made more extreme by the effects of climate change." CRADA The platform displays real-time observational data from Sofar’s global network of Spotter buoys The Navy is evaluating Wayfinder under CNMOC and Sofar’s five-year Cooperative Research and Development Agreement (CRADA) signed in July 2023. Wayfinder reduces manual tasks for forecasters and routers by automatically generating a forecast along a vessel’s route. The platform displays real-time observational data from Sofar’s global network of Spotter buoys to reduce weather uncertainty for route optimisation, and predict unwanted vessel motions during a voyage. Real-time wave and weather observations The availability of accurate real-time wave and weather observations helps Captains and shoreside personnel validate forecast models and examine multiple route options more efficiently, streamlining a historically complex and arduous process. Lea Locke-Wynn, Undersea Warfare Technical Lead for CNMOC’s Future Capabilities Department, said, "A key focus area for the Naval Oceanography enterprise is fostering a culture of innovation through collaboration with our commercial partners." Vessel-specific guidance Lea Locke-Wynn adds, "Our ongoing CRADA with Sofar Ocean is a perfect example of how our partnerships can leverage the leading edge in industry to further Department of Defence operations." As the number of naval vessels at sea, including experimental and autonomous ships, continues to increase, forecasters and routers will have less time to spend manually producing vessel-specific guidance. Automated forecast-on-route guidance More efficient routing empowers FWC personnel to focus on challenging, mission-critical tasks Wayfinder helps fill this operational gap, enabling FWC-N and FWC-SD to more efficiently support a large fleet in real-time with automated forecast-on-route guidance. More efficient routing empowers FWC personnel to focus on challenging, mission-critical tasks that require their unique expertise. Streamlined decisions Captain Erin Ceschini, Commanding Officer, FWC-SD, stated, "By using Wayfinder, we’re able to better visualise our ships’ routes, and make safer and more streamlined decisions on route, speed, and heading." Captain Erin Ceschini adds, "Wayfinder has the potential to be a critical component of our day-to-day operations and a key driver of safe routing as we contend with an increasingly unpredictable weather landscape."
Strengthening trade relations and promoting collaboration between Valenciaport and China. This is the objective with which the Port Authority of València has traveled to China to participate in the 8th edition of the Maritime Silk Road Port International Cooperation Forum 2024, held from June 26 to 28, 2024 in Ningbo (China). The value proposition of the Valencian enclosure as a green, intelligent and innovative HUB of the Mediterranean has been the common thread of the presentation of the PAV in this forum. Advantages of Valenciaport as a strategic port Mar Chao has also described the strategic importance of Valenciaport for the Chinese market During the event, Mar Chao, President of the PAV, had the opportunity to present the competitive advantages of Valenciaport as a strategic port in the center of the Mediterranean (through which 40% of Spanish import/export is channeled) at the service of the business fabric of its area of influence and a link in the logistics chain. Mar Chao has also described the strategic importance of Valenciaport for the Chinese market as a key point of direct connection with Europe that promotes a green growth, market-oriented, with maximum efficiency in services and a complete logistic and multimodal integration. Commercial capacity of Valenciaport During her conference, the President also highlighted the commercial capacity of Valenciaport, with an area of influence of more than 2,000 kilometres that maintains a direct relationship with the main international ports. Cristina Rodríguez, Head of Containers of Valenciaport, accompanies Chao in the forum. Both have held business meetings with Asian companies and institutions, including the new president of the Port of Ningbo, Tao Chengbo. In the framework of this meeting, the representatives of Valenciaport and the Port of Ningbo have signed a memorandum of understanding (MOU) with the aim of strengthening their commercial collaboration. Silk Road Port and Maritime Cooperation Forum The Silk Road Port and Maritime Cooperation Forum of Ningbo (China) in which Valenciaport participates is a platform for open exchange and mutual learning in port development and maritime transport, within the framework of the Belt and Road Initiative. From a respect for the uniqueness of each participating port, the Forum is seen as a tool to foster collaboration in various fields to build bridges between supply and demand in business, investment, technology, talent, information, ports and cultural exchange.
Round table discussion
Given the diverse stakeholders in the maritime industry, it is understandable that collaboration is a challenge. However, the interconnected ecosystem of maritime makes collaboration essential. From ship owners and operators to port authorities, from shippers to shipbuilders, from classification societies to marine service providers and others, there are vast opportunities to work together and cooperate. To gain insight, we asked our Expert Panel Roundtable: How can the maritime industry increase collaboration, and what are the benefits?
Achieving optimal return on investment (ROI) for a maritime company involves a strategic combination of operational efficiency, revenue enhancement, cost control, careful financial management, attention to sustainability and regulatory compliance, and other factors. Given all the variables in play, profitability can be elusive, but our Expert Panel Roundtable has some ideas. We asked: How can maritime companies maximise return on investment (ROI)?