Efficiency
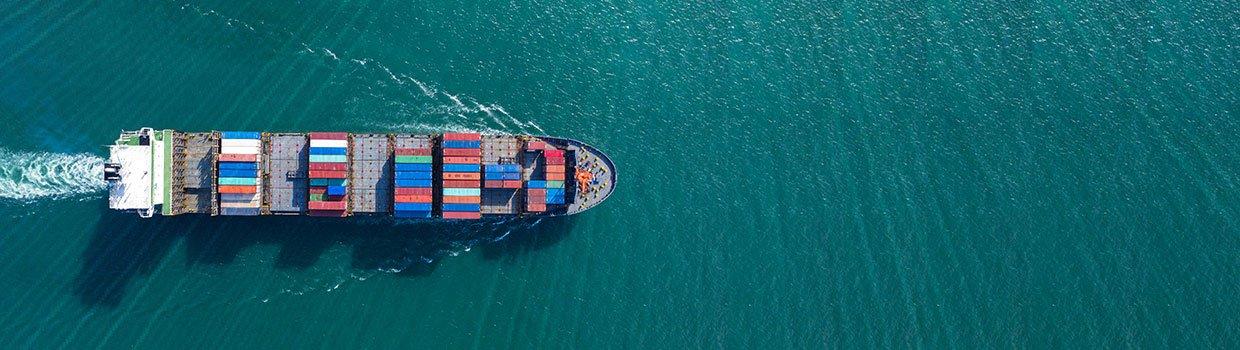
Alfa Laval announces that Martijn Bergink has been appointed President of the Marine Division, effective 1 September 2025. This is in addition to his current roles as President of Business Unit Pumping Systems in the Marine Division and Managing Director of Framo, an Alfa Laval-owned company. Martijn Bergink joined Alfa Laval in 1998 and, since then, he has held multiple senior leadership positions within the company, mostly in the Marine Division. Enhancing energy efficiency Martijn will co...
Watson Farley & Williams (WFW) advised shipping company - MPC Container Ships ASA (MPCC) on two transactions, as part of the implementation of its fleet strategy. The first transaction was the order of four new 4,500 TEU container vessels from Chinese shipyard Taizhou Sanfu Ship Engineering for a total investment of US$228 million. The ships are scheduled for completion and delivery to MPCC in the second half of 2027. Decarbonisation of maritime transport MPC has already signed three-year...
OrbitMI is pleased to announce that it has agreed to acquire Quebec-based AuQub, an artificial intelligence (AI) firm whose suite of AI-driven agents optimises workflows and automates repetitive tasks, helping businesses enhance productivity through more efficient decision-making. By incorporating AuQub’s innovative and accessible SaaS solutions into its platform, OrbitMI continues to advance the adoption of intelligent, connected workflows to help its maritime customers operate profitab...
Marine Masters has successfully completed its offshore scope for the decommissioning of the South Angsi Alpha (SAA) platform, operated by Hibiscus Oil & Gas Malaysia Limited. The campaign marks a major milestone in the repurposing of retired offshore infrastructure, with the platform’s substructure now resting on the seabed as part of Malaysia’s largest rig-to-reef project. Safe removal and partial reefing Topside and substructure were designed for safe removal and reefing in...
ABS enhanced its CLP-V(PARR) lashing notation to include a seasonality factor, which gives additional operational flexibility to container ship operators. Introduced in 2024, the CLP-V(PARR) notation combines the ABS computer lashing program with mandatory parametric roll guidance, allowing operators to optimise stowage and lashing of containers, up to an additional tier of containers on deck, with reduced risk of loss due to parametric rolling. Route splitting approach The new seasonality fa...
The world’s pioneering port and cargo supply chain event series – TOC Worldwide – is proud to announce the second edition of TOC Africa, hosted in Morocco, home to both Africa and the Mediterranean’s largest container port, Tanger Med. This highly anticipated event will bring together industry pioneers, innovators, and stakeholders to explore the transformative potential of Africa’s ports and logistics sector. Energy, innovation, and collaboration Building on the...
News
AdvanTec Marine is pleased to announce a major milestone: both its Canadian manufacturing facility in British Columbia and its Oregon, USA facility are now certified to produce fire-rated marine doors. With the Canadian site receiving MED Wheel Mark certification — making it the only such facility in Canada — AdvanTec now proudly holds fire-rated door certifications on both sides of the border. Commitment to safety and innovation New chapter as AdvanTec strengthens its position as a trusted partner for shipbuilders worldwide This achievement underscores the company's unwavering commitment to safety and innovation, and marks an exciting new chapter as AdvanTec strengthens its position as a trusted partner for shipbuilders worldwide. "This dual certification across both our Canadian and U.S. facilities allows us to better serve our customers with shorter lead times, tariff-free manufacturing, and complete compliance with international safety regulations," said Dean Robinson, Director of Products & Business Systems, AdvanTec Marine. Highest international standards AdvanTec Marine offers A0, A15, A30, and A60 fire-rated doors from both its Canadian and U.S. facilities. These doors are engineered to meet the highest international standards and are available in both Watertight and Weathertight configurations: Watertight fire-rated doors are designed for watertight bulkheads below the freeboard deck and are capable of withstanding static head pressure from either side. Weathertight fire-rated doors offer robust protection against driving rain and washdown, making them ideal for above-deck applications. Key classification society requirements AdvanTec fire-rated doors are built in accordance with the IMO 2010 FTP Code Part 3 and hold MED certification All AdvanTec fire-rated doors are built in accordance with the IMO 2010 FTP Code Part 3 and hold MED certification by DNV, ensuring they offer the same fire resistance as the structural bulkhead into which they are installed. Additionally, the doors meet key classification society requirements, including Lloyd's Register (LR), DNV, Bureau Veritas (BV), and American Bureau of Shipping (ABS). AdvanTec's investment in certification "This dual certification across both our Canadian and U.S. facilities allows us to better serve our customers with shorter lead times, tariff-free manufacturing, and complete compliance with international safety regulations," said Dean Robinson, Director of Products & Business Systems at AdvanTec Marine, adding "We're proud to support shipbuilders with reliable, certified fire-rated doors." With growing global demand for compliant marine safety solutions, AdvanTec's investment in certification and in-house manufacturing reinforces its commitment to innovation, safety, and service across the marine industry.
A strategic collaboration between Icon Gulf Trading DMCC (part of the Dynamic Group) and GeoServe Energy Transport DMCC has enabled the successful shipment of bauxite from Guinea over the past 12 months. During this period, 12 cargo shipments, moving approximately two million tons of bauxite, have been completed. Icon Gulf Trading appointed GeoServe to manage end-to-end shipping operations, through its Commercial Voyage Management as a Service (CVMaaS) covering areas, such as chartering, voyage execution, laytime calculations, port disbursements, regulatory compliance, and financial reporting. Operational discipline to the shipping process This collaboration has brought a high degree of transparency and operational discipline to the shipping process This collaboration has brought a high degree of transparency and operational discipline to the shipping process for Icon Gulf Trading, effectively optimising the bauxite shipping value chain, thereby reinforcing Icon Gulf Trading’s ability to meet customer demand across global markets. GeoServe CVMaaS is a complete pre- and post-fixture offering. This turnkey solution combines skilled professionals, proven processes, and a robust digital ecosystem into one cohesive service allowing traders and operators to focus on their core business and expansion strategies. Complex maritime environment Rajesh Sawana, Deputy General Manager at Icon Gulf Trading, commented, "Appointed as our shipping extended arm, GeoServe has introduced a layer of operational transparency and professionalism that is essential in today’s complex maritime environment." He adds, "The journey has just begun, as Icon Gulf intends to ramp up exports to 10-12 million tons of cargo per annum in a phased manner over the next two years, thereby chartering over 55 Capesize/Newcastlemax vessels per annum." Integrated ecosystem of solutions "We are proud of what we have accomplished together over the past year. Through this engagement, we have seen how a simple and scalable approach to voyage management can deliver real impact," said Alok Srivastava, Head of Shipping at GeoServe. "Despite disruptions and shifting market dynamics, our shared commitment to reliability, regulatory alignment, and long-term sustainability has remained unwavering. By offering an integrated ecosystem of solutions, we look forward to continuing to deliver measurable value to Icon Gulf Trading and the wider supply chain," adds Alok Srivastava. The collaboration now enters its second year. Icon Gulf and GeoServe continue to deliver innovative solutions tailored to the evolving dynamics of global bulk commodity trade.
RightShip announces the launch of Due Diligence Hub, a new product purpose-built for charterers with in-house vetting or risk assurance teams, who want to stay in full control of their risk management decisions more efficiently. Drawing on more than two decades of expertise in vessel vetting and maritime risk assurance, Due Diligence Hub represents the next step in RightShip’s evolution from a vetting service provider into a technology partner — one that puts powerful tools directly in the hands of those managing their unique risk profiles, delivering intelligence and enabling faster, more confident decisions in an increasingly complex operating environment. Final decision on vessel suitability New product enables users to streamline workflows, reduce manual work, centralise documentation RightShip’s new Due Diligence Hub is a smart, flexible workflow tool that empowers charterers, traders, terminals, and others to stay firmly in control of their vessel evaluation and risk management processes — from setting internal risk criteria to making the final decision on vessel suitability. By combining trusted RightShip data, the new product enables users to streamline workflows, reduce manual work, centralise documentation, and gain full visibility into risk factors — leading to more efficient risk management. RightShip’s use of Agentic AI Its highly customisable workflows and AI-enabled efficiencies make it suitable not only for the dry bulk segment — where RightShip has long been an established pioneer — but also position the company to better serve the chemicals and oil & gas sectors as they look for more efficient risk management. At the heart of Due Diligence Hub is RightShip’s use of Agentic AI — that handles time-consuming, repetitive checks in the background. This frees in-house teams to focus on the complex, high-value decisions where human expertise makes the difference. Close collaboration with stakeholders “The Due Diligence Hub has been shaped through close collaboration with our stakeholders who know exactly where the bottlenecks are,” said Marlon Grech, Chief Technology and Product Officer at RightShip. Marlon Grech adds, “Our goal was to build a product that fits seamlessly into our customers’ workflows, uses AI to take the pain out of repetitive tasks, and ultimately makes day-to-day risk management faster, clearer, and more effective.” RightShip’s trusted data with flexible workflows The tool combines RightShip’s trusted data with flexible workflows that adapt to each customer’s internal policies The tool combines RightShip’s trusted data with flexible workflows that adapt to each customer’s internal policies. Users can build and apply custom risk criteria, automate repetitive tasks, maintain full audit trails, and collaborate seamlessly across teams — all in one place. “Our customers’ needs and workflows are evolving fast, and our solutions must evolve with them,” said Saurabh Dasgupta, Chief Commercial Officer at RightShip. Saurabh Dasgupta adds, “With Due Diligence Hub, we’re giving charterers and terminals — across dry bulk and other segments like chemicals and oil & gas — the flexibility to manage risk their way, while ensuring safety remains at the heart of every decision. It’s about striking the right balance between agility and assurance, so our customers can stay ahead with confidence.” Proactive risk management The result is faster, more transparent decisions without compromising on rigour. The launch marks another milestone in RightShip’s evolution as a pioneer in driving safer, more sustainable, and more efficient risk management. RightShip is harnessing the power of AI and the industry’s richest and trusted data and expertise to enable real-time, proactive risk management — putting customers firmly in the driver’s seat.
The 10th annual Maritime Standard Tanker Conference 2025 will be held on Thursday, 30th October at the iconic Atlantis, The Palm, Dubai. Aimed at key decision makers and opinion formers within the tanker shipping business, the event takes place at an uncertain time for the industry, given economic volatility and a host of geopolitical issues. Tough environmental regulations There is also growing pressure to comply with tough environmental regulations There is also growing pressure to comply with tough environmental regulations, presenting a series of technical and commercial hurdles. While there is long term optimism about the future of the industry, there are certainly short term challenges, and how best to navigate through these will be the core, overarching theme of this year’s conference. Tanker shipping negotiates challenging market headwinds. Session 2 in the afternoon will have the theme of “Boosting operational efficiency while maintaining a focus on green shipping.” This session will focus on the key issues facing tanker shipowners and operators in terms of day-to-day operations, and the solutions available to them. Environmental regulatory changes This will look at how best to accommodate environmental regulatory changes, embrace technology advances in areas such as digitalisation and AI to best effect, and also to address growing seafarer and vessel safety concerns. This session will hear from a range of speakers from various sectors, including ship repair, maritime insurance, law, bunker supply, ship management, security, information technology, as well as tanker owners and operators. Topics proposed for inclusion include: Embracing new generation tanker designs Retrofitting for a green, profitable future Harnessing the power of AI to strengthen commercial and operational resilience Safety at sea - tackling the renewed threat of piracy, cyber security and other safety challenges facing the industry Carbon capture as a viable future option for tanker shipping Developing solid financial foundation to support future growth. Speakers will also examine the importance of creating alternative fuel supply networks and debate which fuel is the best option for dual fuel operations in different market segments.
Strategic Marine, a pioneer in aluminium vessel construction, is proud to announce the successful delivery of a next-generation 27m Crew Transfer Vessel (CTV) to new client Yeosu Ocean Co, Ltd, marking its continued momentum of CTV deliveries into South Korea. This milestone highlights Strategic Marine’s growing global footprint and continued success in winning new clients in emerging offshore wind markets. Efficient FPP propulsion The newly delivered vessel is based on the proven StratCat 27 design, developed in close collaboration with BMT, and is engineered to perform in the rigorous conditions of offshore wind farm operations internationally. It features a distinctive hull form for improved seakeeping, as well as efficient FPP propulsion to enhance fuel efficiency, manoeuvrability, and lower emissions—ideal for operating in South Korea’s dynamic offshore environment. Offshore wind farm development and maintenance The vessel will support crew transfers for offshore wind farm growth and care in South Korea This delivery represents Strategic Marine’s growing presence in South Korea’s rapidly growing offshore renewables sector, as the country accelerates efforts to expand its wind energy capacity. The vessel will support crew transfers for offshore wind farm development and maintenance in South Korean waters, contributing to the nation’s clean energy transition and ambitions. Mr. Chan Eng Yew, CEO of Strategic Marine, stated: “We are delighted to deliver Ventus Camellia to South Korea and to begin a new partnership with Yeosu Ocean. This delivery not only expands our presence in Asia’s offshore wind markets but also reflects our ability to support new clients through reliable quality, innovation, and performance. We are excited to be part of South Korea’s renewable energy journey.” Offshore wind vessel solutions Strategic Marine continues to strengthen its position as a preferred global partner for offshore wind vessel solutions, delivering tailored, high-performance vessels to meet the evolving needs of new and existing clients. Mr. BH Park, VP of Yeosu Ocean Co, Ltd, mentioned: “This delivery marks a meaningful milestone for us in Yeosu Ocean, being able to contribute towards South Korea’s growing offshore wind sector. Ventus Camellia will play a crucial role in supporting our goals and we look forward to seeing her in operations.”
Dry bulk carriers entered with INTERCARGO continue to demonstrate stronger performance than the global fleet average on safety and compliance, according to the Association’s latest Benchmarking Report. The report highlights meaningful differences across the sector, with significant variations in inspection outcomes, operational risk and regulatory performance. Incidence of regulatory deficiencies INTERCARGO-member ships consistently show a lower incidence of regulatory deficiencies and detentions compared with the global fleet. “These results show that quality is measurable,” said John Xylas, Chairman of INTERCARGO. “Responsible, quality operators are delivering safer, more compliant ships, and benchmarking helps identify strengths, highlights areas for improvement and promotes operational integrity throughout the industry.” Ship operations and management Some parts of the global fleet remain consistently linked to higher levels of risk exposure The report also identifies continued disparities in class and flag performance. Some parts of the global fleet remain consistently linked to higher levels of risk exposure and weaker inspection outcomes. These trends reinforce the importance of transparency, strong oversight, and data-informed decision-making in ship operations and management. Benchmarking Report INTERCARGO also notes regional shifts in enforcement activity, with some Port State Control regimes taking a more active approach to inspections and detentions. These developments underline the importance of consistent and equitable Port State Control. The Benchmarking Report draws on a range of public and commercial data sources. By identifying trends and supporting greater transparency, the Association seeks to strengthen safety, compliance and performance across the global dry bulk sector.
AdvanTec Marine is pleased to announce a major milestone: both its Canadian manufacturing facility in British Columbia and its Oregon, USA facility are now certified to produce fire-rated marine doors. With the Canadian site receiving MED Wheel Mark certification — making it the only such facility in Canada — AdvanTec now proudly holds fire-rated door certifications on both sides of the border. Commitment to safety and innovation New chapter as AdvanTec strengthens its position as a trusted partner for shipbuilders worldwide This achievement underscores the company's unwavering commitment to safety and innovation, and marks an exciting new chapter as AdvanTec strengthens its position as a trusted partner for shipbuilders worldwide. "This dual certification across both our Canadian and U.S. facilities allows us to better serve our customers with shorter lead times, tariff-free manufacturing, and complete compliance with international safety regulations," said Dean Robinson, Director of Products & Business Systems, AdvanTec Marine. Highest international standards AdvanTec Marine offers A0, A15, A30, and A60 fire-rated doors from both its Canadian and U.S. facilities. These doors are engineered to meet the highest international standards and are available in both Watertight and Weathertight configurations: Watertight fire-rated doors are designed for watertight bulkheads below the freeboard deck and are capable of withstanding static head pressure from either side. Weathertight fire-rated doors offer robust protection against driving rain and washdown, making them ideal for above-deck applications. Key classification society requirements AdvanTec fire-rated doors are built in accordance with the IMO 2010 FTP Code Part 3 and hold MED certification All AdvanTec fire-rated doors are built in accordance with the IMO 2010 FTP Code Part 3 and hold MED certification by DNV, ensuring they offer the same fire resistance as the structural bulkhead into which they are installed. Additionally, the doors meet key classification society requirements, including Lloyd's Register (LR), DNV, Bureau Veritas (BV), and American Bureau of Shipping (ABS). AdvanTec's investment in certification "This dual certification across both our Canadian and U.S. facilities allows us to better serve our customers with shorter lead times, tariff-free manufacturing, and complete compliance with international safety regulations," said Dean Robinson, Director of Products & Business Systems at AdvanTec Marine, adding "We're proud to support shipbuilders with reliable, certified fire-rated doors." With growing global demand for compliant marine safety solutions, AdvanTec's investment in certification and in-house manufacturing reinforces its commitment to innovation, safety, and service across the marine industry.
A strategic collaboration between Icon Gulf Trading DMCC (part of the Dynamic Group) and GeoServe Energy Transport DMCC has enabled the successful shipment of bauxite from Guinea over the past 12 months. During this period, 12 cargo shipments, moving approximately two million tons of bauxite, have been completed. Icon Gulf Trading appointed GeoServe to manage end-to-end shipping operations, through its Commercial Voyage Management as a Service (CVMaaS) covering areas, such as chartering, voyage execution, laytime calculations, port disbursements, regulatory compliance, and financial reporting. Operational discipline to the shipping process This collaboration has brought a high degree of transparency and operational discipline to the shipping process This collaboration has brought a high degree of transparency and operational discipline to the shipping process for Icon Gulf Trading, effectively optimising the bauxite shipping value chain, thereby reinforcing Icon Gulf Trading’s ability to meet customer demand across global markets. GeoServe CVMaaS is a complete pre- and post-fixture offering. This turnkey solution combines skilled professionals, proven processes, and a robust digital ecosystem into one cohesive service allowing traders and operators to focus on their core business and expansion strategies. Complex maritime environment Rajesh Sawana, Deputy General Manager at Icon Gulf Trading, commented, "Appointed as our shipping extended arm, GeoServe has introduced a layer of operational transparency and professionalism that is essential in today’s complex maritime environment." He adds, "The journey has just begun, as Icon Gulf intends to ramp up exports to 10-12 million tons of cargo per annum in a phased manner over the next two years, thereby chartering over 55 Capesize/Newcastlemax vessels per annum." Integrated ecosystem of solutions "We are proud of what we have accomplished together over the past year. Through this engagement, we have seen how a simple and scalable approach to voyage management can deliver real impact," said Alok Srivastava, Head of Shipping at GeoServe. "Despite disruptions and shifting market dynamics, our shared commitment to reliability, regulatory alignment, and long-term sustainability has remained unwavering. By offering an integrated ecosystem of solutions, we look forward to continuing to deliver measurable value to Icon Gulf Trading and the wider supply chain," adds Alok Srivastava. The collaboration now enters its second year. Icon Gulf and GeoServe continue to deliver innovative solutions tailored to the evolving dynamics of global bulk commodity trade.
RightShip announces the launch of Due Diligence Hub, a new product purpose-built for charterers with in-house vetting or risk assurance teams, who want to stay in full control of their risk management decisions more efficiently. Drawing on more than two decades of expertise in vessel vetting and maritime risk assurance, Due Diligence Hub represents the next step in RightShip’s evolution from a vetting service provider into a technology partner — one that puts powerful tools directly in the hands of those managing their unique risk profiles, delivering intelligence and enabling faster, more confident decisions in an increasingly complex operating environment. Final decision on vessel suitability New product enables users to streamline workflows, reduce manual work, centralise documentation RightShip’s new Due Diligence Hub is a smart, flexible workflow tool that empowers charterers, traders, terminals, and others to stay firmly in control of their vessel evaluation and risk management processes — from setting internal risk criteria to making the final decision on vessel suitability. By combining trusted RightShip data, the new product enables users to streamline workflows, reduce manual work, centralise documentation, and gain full visibility into risk factors — leading to more efficient risk management. RightShip’s use of Agentic AI Its highly customisable workflows and AI-enabled efficiencies make it suitable not only for the dry bulk segment — where RightShip has long been an established pioneer — but also position the company to better serve the chemicals and oil & gas sectors as they look for more efficient risk management. At the heart of Due Diligence Hub is RightShip’s use of Agentic AI — that handles time-consuming, repetitive checks in the background. This frees in-house teams to focus on the complex, high-value decisions where human expertise makes the difference. Close collaboration with stakeholders “The Due Diligence Hub has been shaped through close collaboration with our stakeholders who know exactly where the bottlenecks are,” said Marlon Grech, Chief Technology and Product Officer at RightShip. Marlon Grech adds, “Our goal was to build a product that fits seamlessly into our customers’ workflows, uses AI to take the pain out of repetitive tasks, and ultimately makes day-to-day risk management faster, clearer, and more effective.” RightShip’s trusted data with flexible workflows The tool combines RightShip’s trusted data with flexible workflows that adapt to each customer’s internal policies The tool combines RightShip’s trusted data with flexible workflows that adapt to each customer’s internal policies. Users can build and apply custom risk criteria, automate repetitive tasks, maintain full audit trails, and collaborate seamlessly across teams — all in one place. “Our customers’ needs and workflows are evolving fast, and our solutions must evolve with them,” said Saurabh Dasgupta, Chief Commercial Officer at RightShip. Saurabh Dasgupta adds, “With Due Diligence Hub, we’re giving charterers and terminals — across dry bulk and other segments like chemicals and oil & gas — the flexibility to manage risk their way, while ensuring safety remains at the heart of every decision. It’s about striking the right balance between agility and assurance, so our customers can stay ahead with confidence.” Proactive risk management The result is faster, more transparent decisions without compromising on rigour. The launch marks another milestone in RightShip’s evolution as a pioneer in driving safer, more sustainable, and more efficient risk management. RightShip is harnessing the power of AI and the industry’s richest and trusted data and expertise to enable real-time, proactive risk management — putting customers firmly in the driver’s seat.
The 10th annual Maritime Standard Tanker Conference 2025 will be held on Thursday, 30th October at the iconic Atlantis, The Palm, Dubai. Aimed at key decision makers and opinion formers within the tanker shipping business, the event takes place at an uncertain time for the industry, given economic volatility and a host of geopolitical issues. Tough environmental regulations There is also growing pressure to comply with tough environmental regulations There is also growing pressure to comply with tough environmental regulations, presenting a series of technical and commercial hurdles. While there is long term optimism about the future of the industry, there are certainly short term challenges, and how best to navigate through these will be the core, overarching theme of this year’s conference. Tanker shipping negotiates challenging market headwinds. Session 2 in the afternoon will have the theme of “Boosting operational efficiency while maintaining a focus on green shipping.” This session will focus on the key issues facing tanker shipowners and operators in terms of day-to-day operations, and the solutions available to them. Environmental regulatory changes This will look at how best to accommodate environmental regulatory changes, embrace technology advances in areas such as digitalisation and AI to best effect, and also to address growing seafarer and vessel safety concerns. This session will hear from a range of speakers from various sectors, including ship repair, maritime insurance, law, bunker supply, ship management, security, information technology, as well as tanker owners and operators. Topics proposed for inclusion include: Embracing new generation tanker designs Retrofitting for a green, profitable future Harnessing the power of AI to strengthen commercial and operational resilience Safety at sea - tackling the renewed threat of piracy, cyber security and other safety challenges facing the industry Carbon capture as a viable future option for tanker shipping Developing solid financial foundation to support future growth. Speakers will also examine the importance of creating alternative fuel supply networks and debate which fuel is the best option for dual fuel operations in different market segments.
Strategic Marine, a pioneer in aluminium vessel construction, is proud to announce the successful delivery of a next-generation 27m Crew Transfer Vessel (CTV) to new client Yeosu Ocean Co, Ltd, marking its continued momentum of CTV deliveries into South Korea. This milestone highlights Strategic Marine’s growing global footprint and continued success in winning new clients in emerging offshore wind markets. Efficient FPP propulsion The newly delivered vessel is based on the proven StratCat 27 design, developed in close collaboration with BMT, and is engineered to perform in the rigorous conditions of offshore wind farm operations internationally. It features a distinctive hull form for improved seakeeping, as well as efficient FPP propulsion to enhance fuel efficiency, manoeuvrability, and lower emissions—ideal for operating in South Korea’s dynamic offshore environment. Offshore wind farm development and maintenance The vessel will support crew transfers for offshore wind farm growth and care in South Korea This delivery represents Strategic Marine’s growing presence in South Korea’s rapidly growing offshore renewables sector, as the country accelerates efforts to expand its wind energy capacity. The vessel will support crew transfers for offshore wind farm development and maintenance in South Korean waters, contributing to the nation’s clean energy transition and ambitions. Mr. Chan Eng Yew, CEO of Strategic Marine, stated: “We are delighted to deliver Ventus Camellia to South Korea and to begin a new partnership with Yeosu Ocean. This delivery not only expands our presence in Asia’s offshore wind markets but also reflects our ability to support new clients through reliable quality, innovation, and performance. We are excited to be part of South Korea’s renewable energy journey.” Offshore wind vessel solutions Strategic Marine continues to strengthen its position as a preferred global partner for offshore wind vessel solutions, delivering tailored, high-performance vessels to meet the evolving needs of new and existing clients. Mr. BH Park, VP of Yeosu Ocean Co, Ltd, mentioned: “This delivery marks a meaningful milestone for us in Yeosu Ocean, being able to contribute towards South Korea’s growing offshore wind sector. Ventus Camellia will play a crucial role in supporting our goals and we look forward to seeing her in operations.”
Dry bulk carriers entered with INTERCARGO continue to demonstrate stronger performance than the global fleet average on safety and compliance, according to the Association’s latest Benchmarking Report. The report highlights meaningful differences across the sector, with significant variations in inspection outcomes, operational risk and regulatory performance. Incidence of regulatory deficiencies INTERCARGO-member ships consistently show a lower incidence of regulatory deficiencies and detentions compared with the global fleet. “These results show that quality is measurable,” said John Xylas, Chairman of INTERCARGO. “Responsible, quality operators are delivering safer, more compliant ships, and benchmarking helps identify strengths, highlights areas for improvement and promotes operational integrity throughout the industry.” Ship operations and management Some parts of the global fleet remain consistently linked to higher levels of risk exposure The report also identifies continued disparities in class and flag performance. Some parts of the global fleet remain consistently linked to higher levels of risk exposure and weaker inspection outcomes. These trends reinforce the importance of transparency, strong oversight, and data-informed decision-making in ship operations and management. Benchmarking Report INTERCARGO also notes regional shifts in enforcement activity, with some Port State Control regimes taking a more active approach to inspections and detentions. These developments underline the importance of consistent and equitable Port State Control. The Benchmarking Report draws on a range of public and commercial data sources. By identifying trends and supporting greater transparency, the Association seeks to strengthen safety, compliance and performance across the global dry bulk sector.


Expert commentary
Marine industry pioneers gathered at Nor-Shipping in June, with a focus on the key challenges and opportunities driving the transition to a lower-carbon future. With regulations such as the Carbon Intensity Indicator (CII), FuelEU Maritime, the EU Emissions Trading System (EU ETS) and the upcoming International Maritime Organisation (IMO) carbon levy, fouling control systems continue to play a vital role in the shipping industry as the regulatory bodies chart a course towards net-zero emissions by 2050. Fouling control systems Vessel operators will have to navigate a new challenge on the horizon after a global deal agreement These fouling control systems help reduce fuel consumption and CO₂ emissions, enabling vessels to maintain favourable efficiency ratings and avoid penalties. Vessel operators will have to navigate a new challenge on the horizon after a global deal agreement was passed at the UN's IMO MEPC 83 meeting in April, following almost a decade of negotiations. Carbon-intensive fuels From 2028, owners of large vessels will have to reduce their carbon-intensive fuels or face fines of up to $380 per tonne of carbon dioxide emissions from burning fuel. Shipping has become the first industry in the world with internationally mandated targets to reduce emissions and according to maritime consultancy UMAS, the historic agreement could result in an eight percent reduction in emissions by 2030. Fouling control coatings Vessel operators need to consult coating companies with proven expertise in fouling control coatings The deal is a historic moment for the industry and will further drive home the importance of cutting fuel consumption. Marine coatings and technologies, in isolation, are not enough for shipowners to comply with the regulations. Vessel operators need to consult coating companies with proven expertise in high-performing fouling control coatings and a strong track record of in-service performance, to support data-driven and well-informed investment decisions. Underwater hull schemes We’ve supported customers with their CII ratings and have helped them offset the EU ETS surcharge, which came into effect last year. In 2024, shipowners were responsible for 40% of their emissions costs, increasing to 70% this year and set to reach 100% from 2026. Last year, a record number of customers engaged with us to identify the most suitable underwater hull schemes to aid CII compliance, highlighting the growing demand for tailored fouling control solutions from International® marine coatings. Our solutions not only ensure regulatory compliance but also enhance vessel performance and sustainability. Vessel fuel consumption and CO2 emissions Application of Intercept® 8500 LPP on a trading VLCC vessel led to a removal of carbon emissions For example, the application of Intercept® 8500 LPP on a globally trading VLCC vessel led to a reduction of carbon emissions of approximately 8,500 tonnes over the five years in service. As a result, this vessel maintained a CII ‘A’ grade rating throughout the study, which resulted in the customer achieving both performance and decarbonisation targets. Furthermore, we have seen increased demand for Intertrac® Vision, our big data prediction tool that enables ship owners and operators to assess the impact of fouling control coatings on vessel fuel consumption and CO2 emissions while in transit. This digital tool allows our experts to collaborate closely with vessel operators to assess the return on investment of various coating schemes, tailored to vessel type and operating conditions. It simplifies the coatings selection process and delivers data-driven insights for more informed decision-making. Hull performance expertise and data-driven insights The carbon levy passed at the IMO meeting in April is scheduled for implementation in 2028. With steeper penalties, it is expected to impact global shipping routes if vessel operators do not reduce their reliance on carbon-intensive fuels. However, there are steps that shipowners can take to invest in regulation compliances and minimise penalties. With nearly 150 years of experience serving the marine industry, offering high-performance coatings, hull performance expertise and data-driven insights, we are uniquely positioned to help shipowners achieve regulatory compliance while maintaining operational efficiency.
Maritime digitalisation, decarbonisation and autonomy were the dominant themes at this month's Nor-shipping conference, where mariners from around the world gathered to discuss the industry's future. But beneath these headline topics, a fundamental shift in maritime navigation is quietly underway. S-100, the next generation of maritime data standards, will transform today's static navigation systems into dynamic, real-time communication networks that revolutionise everything from autonomous navigation to sustainable voyage planning. Overcome implementation challenges All vessels will be required to have S-100 compatible ECDIS, but S-57 charts will continue We have been working closely with NAVTOR to develop S-100 compatible Electronic Chart Display and Information System (ECDIS). I spoke alongside Bjørn Kristian Sæstad and John K Klippen at the NAVTOR panel to explore how S-100 builds on the success of S-57 and what is being done in the lead up to 2029, when all vessels will be required to have S-100 compatible ECDIS but S-57 charts will continue to be supported. As the world's pioneering authority in maritime navigation, the UK Hydrographic Office (UKHO) is spearheading industry education and industry adoption of the S-100 framework. This preparation phase is critical. Success will require collaboration between maritime operators, technology providers, port authorities, and regulatory bodies to overcome implementation challenges and establish industry-wide best practices. Building on proven success The maritime industry has successfully navigated major technological transitions before, from GPS adoption to AIS system implementation. S-100 represents the next chapter in this evolution, building on S-57's proven foundation while introducing flexible and extendable capabilities to support safer, more efficient, and more sustainable maritime operations. The S-57 data platform standardised electronic chart data for over 50,000 vessels worldwide The S-57 data platform standardised electronic chart data for over 50,000 vessels worldwide. But where these charts are standalone files requiring periodic updates, S-100 takes this to the next level. As a universal hydrographic data model, S-100 enables vessels to communicate with each other, shore-based systems, and maritime infrastructure in real-time. It collates a range of data such as weather, tides and traffic into one interoperable ECDIS, providing mariners with a complete picture of their surroundings, optimising high-quality data and enhancing situational awareness. Smooth industry transition The transition from S-57 to S-100 is already underway, with many hydrographic offices preparing to produce and distribute S-100-based products by the 2026 IMO milestone. To ensure a smooth and gradual transition for maritime operators, S-100-compatible ECDIS will continue to support existing Electronic Navigational Charts (ENCs) using the current S-57 standard. This dual capability should eliminate concerns about operational disruption during the transition period. It provides time both for companies to develop S-100 compatible ECDIS and mariners to gradually incorporate S-100 enhanced capabilities and customise their displays based on the information they need. By 2029, S-100 technology will be mandatory for all vessels. Dual capability should eliminate concerns about operational disruption during the transition period To further support mariners becoming familiar with S-100 capabilities before widespread implementation, the UKHO has launched Explore S-100, an online platform where maritime professionals can experience the technology firsthand. Users can browse and interact with 'phase 1' S-100 data layers, including S-101 (ENCs), S-102 (bathymetric surface), S-104 (water levels), and S-111 (surface currents). This comprehensive educational tool is designed to make S-100 feel more like reality, allowing mariners to familiarise themselves with its new capabilities. Real-world testing Real-world testing is now moving from theory to practice. At the recent Nor-shipping conference, I spoke with NAVTOR about the first practical demonstrations of S-100 technology, including sea trials that tested the system under challenging maritime conditions. The St Lawrence River in Canada provides an ideal testing ground, featuring tidal influences, varied currents, narrow dredged navigation channels with deep-water sections, seasonal continuous survey activities, bridges, overhead cables and navigational aids. Testing standards in real-world scenarios allows us to gather feedback and make adjustments before full-scale implementation. This enables developers to fine-tune products based on actual operational experience rather than theoretical requirements. Different areas of the maritime community UKHO has partnered with SeaTrade Maritime to launch a comprehensive survey assessing industry Understanding how the technology performs in practice is only part of the picture. Gauging industry readiness for this transition is just as important. The UKHO has partnered with SeaTrade Maritime to launch a comprehensive survey assessing industry understanding of S-100. By identifying knowledge gaps, implementation concerns, and specific training needs across different areas of the maritime community, we’re informing educational programmes that address real industry requirements. Enabling tomorrow's maritime operations We are seeing major social and political change as the maritime sector works to ensure decarbonisation is at the top of the industry’s agenda. While S-100 will not be the silver bullet to facilitating decarbonisation and sustainability efforts, certain features will enable more sustainable operations. Fuel consumption and port area emissions when vessels ultimately need to wait outside congested terminals Route optimisation technology, for example, can help address one of the industry's most pressing environmental challenges: the widespread "sail fast then wait" approach. This increases fuel consumption and port area emissions when vessels ultimately need to wait outside congested terminals. S-100's real-time data sharing capabilities support just-in-time arrival strategies, enabling vessels to receive current information about port conditions, berth availability, and optimal arrival windows. This shift toward efficiency-focused voyage planning becomes increasingly critical as the industry works toward FuelEU Maritime compliance. S-100 common framework with port operators Route optimisation extends beyond individual vessels to support coordinated traffic management. When multiple ships can access the same real-time port and traffic information, the entire system operates more efficiently, reducing delays and environmental impact across the maritime supply chain. Route optimisation extends beyond individual vessels to support coordinated traffic management Sharing data using the S-100 common framework with port operators and charter parties could help to reduce demurrage penalty payments when the agreed-upon time for cargo operations (laytime) is exceeded. Sharing real-time data (ETA, berth availability, weather, cargo readiness, etc.) helps all stakeholders, charterers, shipowners, and terminal operators plan better. The impact is that it reduces idle time and delays caused by poor coordination or unexpected changes. For example, if bad weather is forecasted using S-100-compliant data, cargo operations can be rescheduled in advance, avoiding idle time that counts against laytime. Cross-industry collaboration As the maritime sector approaches the 2026 implementation milestone, the UKHO remains committed to supporting industry readiness through initiatives like Explore S-100 and comprehensive training resources. The transition offers genuine opportunities for improved operational efficiency, enhanced safety, and reduced environmental impact. These benefits require careful planning, comprehensive education, and ongoing collaboration across the maritime community. By hydrographic offices, shipping companies, technology providers, and regulatory authorities all working together, the industry can ensure S-100 delivers its full potential while maintaining the safety and reliability that mariners depend on every day.
When the Ballast Water Management (BWM) Convention came into force in 2004, it was in response to a crisis we couldn’t afford to ignore—one where invasive aquatic species, carried silently in ships’ ballast tanks, were devastating marine ecosystems. Now, two decades later, compliance with this environmental safeguard is no longer optional—and yet, as recent industry findings reveal, record-keeping failures account for 58% of compliance issues. That’s not a technology problem. That’s a documentation problem —one rooted deeply in data management practices and crew training, where small oversights lead to documentation issues, that may cascade into costly compliance failures. And that’s precisely where digital systems excel, guiding crews clearly to avoid mistakes in the first place. New ballast regulations At the IMO’s 82nd Marine Environment Protection Committee (MEPC 82), new ballast water record-keeping regulations were approved, coming into effect from 1 February 2025. These updates mark a significant tightening of documentation standards—and they could catch unprepared shipowners off guard if not acted on promptly. Why ballast water record-keeping is back in the spotlight These new updates aim to change that—and they’re stricter, smarter, and more detailed than before While MEPC 82 made headlines for advancing decarbonisation policies and ECAs in the Arctic and Norwegian Sea, it also honed in on ballast water—a topic that has quietly regained importance. The committee approved critical updates to how ballast water operations and ballast water management system (BWMS) maintenance are recorded. The goal: Enhance transparency, reduce ambiguity, and reinforce environmental protection by making records more structured, traceable, and actionable. This renewed focus is both a warning and an opportunity. In recent years, too many Port State Control detentions and inspection delays have stemmed not from hardware failures, but from poorly maintained or unclear ballast water records. These new updates aim to change that—and they’re stricter, smarter, and more detailed than before. What’s changing: Bypass scenarios and maintenance logging The revised guidelines introduce two new scenarios for vessels dealing with challenging water quality (CWQ) in ports: Scenario 3: A reactive bypass of the BWMS due to unforeseen poor water quality. Scenario 4: A pre-emptive bypass based on anticipated CWQ conditions. These additions are essential for vessels operating globally, particularly those above 400GT. They ensure that alternative operations—like ballast water exchange plus treatment (BWE + BWT)—are clearly documented. Without accurate records, even legitimate actions can fall short of compliance. Ballast Water Management Plan and OEM manuals MEPC 82 also mandates that BWMS care procedures must now be recorded directly in BWRB MEPC 82 also mandates that BWMS maintenance procedures must now be recorded directly in the Ballast Water Record Book (BWRB), in line with the ship’s Ballast Water Management Plan and Original Equipment Manufacturer (OEM) manuals. Responsible crew members must sign off on these records, ensuring traceability and crew accountability. This step isn’t just regulatory housekeeping—it aligns ballast water maintenance with how other onboard systems are already tracked, from engines to emissions. It’s a logical, overdue move toward consistency across compliance. Paper or digital: The format dilemma While the BWRB can still be maintained on paper or electronically, the burden of new structured data fields and stricter reporting timelines will be felt most by those still tied to manual systems. Each additional layer of documentation increases the chance of human error—and with nearly 6 in 10 compliance failures already stemming from admin issues, that’s a risk many operators can’t afford. This is where digital solutions can offer real relief. At NAPA, we’ve already implemented the latest IMO guidelines into our electronic logbook, so crews can comply with MEPC.369(80) requirements out of the box. With ready-made entry templates and smart input validation, data entry is quick, accurate, and audit-ready. NAPA implemented the latest IMO guidelines into an electronic logbook. Better still, once updated, operators can apply for the BWM Convention Electronic Record Book Declaration from their flag—ensuring that compliance is recognised internationally under MEPC.372(80). Less admin, more assurance Electronic logbooks don’t just streamline compliance—they enable better decision-making. When connected to onboard systems, they automatically pull operational data into the BWRB, reducing manual work and error margins. This frees up the crew to focus on operations and safety, rather than paperwork. From a management perspective, real-time visibility into ballast operations and maintenance records helps shore teams stay ahead of inspections and identify potential compliance gaps early. One logbook, many regulations While ballast water is the focus today, it’s not the only regulation demanding attention While ballast water is the focus today, it’s not the only regulation demanding attention. At NAPA, we’ve designed our logbook to support a wide range of evolving compliance frameworks—including MARPOL, EU-ETS, EU-MRV, CII, and the Garbage Record Book. This unified approach removes silos, reduces duplicated effort, and gives operators a more holistic view of vessel performance and compliance. A smarter way forward With decarbonisation and environmental regulations shifting at breakneck pace, even the most experienced crews and fleet managers can struggle to stay up to date. That’s where technology has a crucial role to play—not to replace expertise, but to support it. At NAPA, we work closely with shipowners and operators to configure regulatory record book templates according to their fleet workflows and each vessel’s specific operational profile. This ensures accuracy, ease of use, and most importantly, continuous compliance—even as the rules keep changing. Because in today’s compliance landscape, staying ahead isn’t just about meeting the minimum. It’s about building systems that help you adapt, respond, and thrive. And that starts with getting the record-keeping and data management right.
Harbour insights
Electrification plays an important role in addressing the environmental challenges facing the maritime sector, and electric propulsion is the key component in this transition. Energy-efficient propulsion, which encompasses both efficient drivetrain and less weight, will contribute to meeting environmental challenges, while providing unwavering reliability for the operators. Cleaner propulsion solutions Ease of integration and maintenance helps streamline system design and installation, crucial factors in speeding up the adoption of cleaner propulsion solutions across the maritime sector. ABB promotes the adoption of advanced motor technologies in the rail, marine, and eMobility sectors through the Traction & Mobile e-Power Motors business unit. The team designs and delivers both components and complete propulsion systems for railway as well as off-highway machines and marine markets. IMO’s 2050 net-zero goals ABB helps the IMO’s 2050 net-zero goals by advancing marine electrification via innovations “The energy-efficient solutions we've developed are enabling compact, reliable electric propulsion in marine applications exemplified by our new AMXE Marine Motor, engineered specifically to meet the harsh demands and specific requirements of the marine market and environment,” says Henrik T. Nilsson, Global Sales Manager for Traction & Mobile e-Power Motors. ABB supports the IMO’s 2050 net-zero goals by advancing marine electrification through innovations like the AMXE Marine Motor and advanced motor control technologies. Conventional propulsion systems This compact, high-power-density AMXE Marine Motor is designed for small to mid-sized electric and hybrid vessels and open deck applications, offering high efficiency, low weight and excellent performance in a durable frame designed to sustain marine environments. By replacing conventional propulsion systems, the AMXE enables cleaner, more sustainable vessel operations. ABB’s global expertise, service network, and complementary technologies further enhance marine efficiency and decarbonisation, says Nilsson. These solutions help shipbuilders and operators meet sustainability targets and transition toward low emission. ABB’s expertise in the marine industry AMXE Marine Motor, which ABB gave at Nor-Shipping in June, uses technologies set for off-highway equipment “ABB is pioneering the way in developing cutting-edge solutions to help the marine transport industry achieve net-zero goals,” says Nilsson. “By consistently innovating and working closely with industry partners, ABB is delivering the technologies and expertise needed to steer the industry towards a cleaner and more sustainable future.” The AMXE Marine Motor, which ABB presented at Nor-Shipping in June, uses technologies developed for off-highway equipment, such as mining trucks or electric buses, combined with a durable design that encompasses ABB’s expertise in the marine industry. ABB’s motor portfolio This resulted in a motor with the highest power density in ABB’s motor portfolio, delivering more power with less weight and space. It is housed in a frame that is compliant with industry standards, including corrosion protection to withstand tough environments. Pairing the motor with ABB inverters like the HES880 Mobile Inverter creates efficient, responsive propulsion systems designed to meet the demands of the next generation of electric and hybrid vessels. ABB’s HES880 Mobile Designed for harsh climates, ABB’s HES880 Mobile rugged, liquid-cooled inverter offers high efficiency The new AMXE Marine Motor offers the highest power density in ABB’s motor portfolio. Its lightweight, compact design makes it more energy-efficient than traditional combustion systems. When paired with ABB drives, it helps to lower energy consumption, boost performance, and reduce operational costs. Designed for harsh environments, ABB’s HES880 Mobile rugged, liquid-cooled inverter offers high efficiency, IP67 protection and a corrosion-resistant enclosure. Its multifunctional use, maintenance-free build, and compact design make it suitable for electrifying heavy-duty applications like vessels. ABB’s experience in marine applications Drawing on ABB’s experience in mining, rail, and marine applications, the AMXE Marine Motor is built to deliver long-lasting, high-performance operation in tough maritime environments. It's fully enclosed water-cooled design reduces noise while enhancing comfort and reliability. Engineered with a robust well-proven insulation system, and a design that supports the installation needs of the marine industry, it ensures a long lifetime and ease of installation in most marine applications as well as machine rooms with limited space. AMXE Marine Motor Key stakeholders in transitioning to electrical marine applications include shipbuilders, vessel operators The AMXE Marine Motor has undertaken extensive validation testing, including IP, shock and vibration, corrosion resistant and validated the insulation system to comply with IVIC Class C. Key stakeholders in transitioning to electrical marine applications include shipbuilders, vessel operators, technology providers like ABB, and regulatory bodies such as the International Maritime Organization (IMO) together with the harbours that need to provide the primary charging infrastructure. Electric propulsion systems Shipbuilders integrate electric propulsion systems into vessel designs, while operators adopt and manage these technologies to improve efficiency and reduce emissions. Regulators drive industry adoption by setting the decarbonisation targets, like the IMO’s 2050 net-zero goal, driving industry adoption. Possibly the biggest challenge for companies looking to decarbonise is uncertainty around the availability and cost of alternative future energy modes. This is probably less of an issue with electrification than other alternative fuels. Availability of electricity Transitioning to electric drivetrains can help lower operating costs, increase efficiency and performance Transitioning to electric drivetrains can help lower operating costs, increase efficiency and performance, and reduce environmental impact. In general, the availability of electricity is more stable, even if work remains in the charging infrastructure for the marine market. The technologies for electric drivetrain on ships are already available and proven effective. Through continue collaboration with the stakeholders in the marine industry, a more sustainable future is possible. Decarbonisation objectives “It was great to be able to meet our customers, engage at Nor-Shipping in meaningful conversations and showcase ABB’s solutions for the marine industry,” says Nilsson. “The event theme ‘Future-Proof’ focused on sustainable solutions and innovations for the future of the maritime sector." Nilsson added: "The theme aligned with the launch of ABB’s AMXE Marine Motor. We are thrilled to provide future-proof solutions that help customers meet their decarbonisation objectives. Being relatively new in the marine industry myself, I was impressed at Nor-Shipping by the openness to new technologies and the deep understanding in the industry of how these new technologies can address current and future challenges.”
Ballast Water Management Systems (BWMS) prevent the spread of invasive aquatic species, which pose significant ecological, economic, and health threats. The systems treat and purify a ship's ballast water before it is discharged into a new environment. Regulations dictate how ballast water is managed and discharged. The IMO Ballast Water Management Convention was adopted in 2004 and ratified on 8 September 2017. In addition, the U.S. Coast Guard (USCG) has also regulated discharges in the USA through local regulations in conjunction with the EPA. Risk of undesirable bio-invasions All ships of 400 gross tons (300 gt for USCG) or more are required to manage their ballast water All ships of 400 gross tons (300 gt for USCG) or more are required to manage their ballast water. A range of technologies have been Type Approved to purify a ship's ballast water, and treatment methods are dominated by those making use of active substances or UV radiation. Ballast Water Treatment Systems (BWTS) remove or render harmless nonindigenous aquatic species and pathogens before the ballast water is discharged into a new location. Therefore, BWTS provide ships the means to comply to the regulations and reduce the risk of undesirable bio-invasions that harm ecosystems, and cause economic and coastal infrastructure damage, according to Dr. Stelios Kyriacou, Chief Technology Officer (CTO) of ERMA FIRST, a manufacturer of ballast water treatment and other sustainable marine equipment systems. BWTS remove or render harmless nonindigenous aquatic species and pathogens. Leadership in the core product category “We have already achieved leadership in our core product category, the Ballast Water Treatment Systems, and our vision remains for our new chapter, the decarbonisation solutions,” says Kimon Mademlis, Group Marketing and Communications Director, ERMA FIRST. “This is the brand promise to our customers that we will always strive for excellence, innovation and stellar offerings.” Flexible and adaptable ballast water management Use of active substance treatments offers a flexible and adaptable ballast water management system ERMA FIRST has developed a full flow filter electro-chlorination system, ERMA FIRST FIT BWTS, and has further expanded its product offering with the acquisition of complementary chemical injection technologies, oneTANK and Ecochlor, for ballast water management. The use of active substance treatments offers a flexible and adaptable ballast water management system to marine operators, says Kyriacou. Electro-chlorination and chemical injection treatments are single pass on ballasting only, unlike UV where a secondary treatment is required at discharge. Ballast water treatment systems Active substance treatments are not impacted by water clarity (UV transmittance) and adapt to water quality challenges better than UV systems while in general have a lower operating expense and energy footprint. ERMA FIRST ensures operational simplicity and lowers costs with their user-friendly ballast water treatment systems. Designed for easy installation and basic crew training, the systems feature automated operation that reduces manual work and ensures compliance with international regulations. Their flexible design fits all vessel types, minimising downtime and retrofit expenses. ERMA FIRST ensures operational simplicity and lowers costs with its user-friendly BWTS. ERMA FIRST global service ERMA FIRST offers global service and remote support, improving system efficiency With low energy consumption and simple maintenance needs, the systems help shipowners reduce daily operational costs while ensuring reliable long-term performance. In addition, ERMA FIRST offers global service and remote support, improving system efficiency and making vessel operations smoother, more reliable, and cost-effective across the fleet. Combining products and services to support customers ERMA FIRST provides a range of services to support customers from the initial sales to long-term operation. The company offers expert advice, system design, and, when requested, assistance during installation to ensure the best fit for each vessel’s needs. They also provide crew training for safe and straightforward operation. Maintenance services, both scheduled and on demand, keep systems running efficiently. With remote monitoring, 24/7 technical support, and service engineers worldwide, ERMA FIRST responds quickly to any issue. “We supply spare parts upon request or as needed, and we maintain stock in major hubs globally,” says Mademlis. “ERMA FIRST ensures reliable, simple, and cost-effective support at every stage.” ERMA FIRST provides a range of services to support customers from the initial sales. New sustainable and reliable products Customers drive the business, while R&D provides new sustainable and reliable products ERMA FIRST’s vision is to be a pioneer in the industry excellence in all they do. Customers drive the business, while R&D provides new sustainable and reliable products and after-sales service delivers customer support. Here is the brand’s purpose statement: “Saving the oceans to safeguarding the planet.” ERMA FIRST is committed to a greener future, a sustainable world, and a bright tomorrow for the generations to come. Expanding range of decarbonisation solutions ERMA FIRST’s track record in ballast water treatment systems, as well as with other marine equipment such as oily water separators and sewage treatment plants, has critically and crucially delivered towards protecting the oceans. The BWTS ensures optimal protection of the seas, and the company offers an expanding range of decarbonisation solutions. “In the maritime sector, technological advancement is driving a major transformation across operations, sustainability, and competitiveness,” says Kyriacou. “We are responding to growing environmental concerns and regulatory pressures, particularly from the International Maritime Organization (IMO), for greenhouse gas (GHG) reduction, decarbonisation and net-zero.” Environmental policy developments ERMA FIRST maintains active R&D programs and invests in energy efficiency measures ERMA FIRST monitors environmental policy developments and adapts and leverages their resources to the develop practical and cost-effective solutions for global shipping. “Our core strategic objectives include sustainability and environmental respectability with a strong desire to maximise our customers’ benefit and support their strategies to achieve carbon neutrality,” says Mademlis. To this end, ERMA FIRST maintains active R&D programs and invests in energy efficiency measures, air lubrication systems (AL) and wind-assisted propulsion systems (WAPS), ship-to-shore power interface, advanced data analytics, and artificial intelligence (AI) to optimise ship operations, performance, and emissions in real-time. ERMA FIRST maintains active R&D programs and invests in energy efficiency measures. Use of diesel electric generators and boilers Decarbonisation measures target ship propulsion with fuel and energy efficiency improvements Decarbonisation measures mainly target ship propulsion with fuel and energy efficiency improvements. Ships, however, also spend time in port where they engage in passenger and cargo operations, while the energy requirements are significantly lower than when in transit. The use of diesel electric generators and boilers in port is responsible for the continued emission of GHG and particulate matter (PM) in the atmosphere and is a major cause of noise pollution. The health and wellbeing of residents in the vicinity of ports is impacted by ship operations. Reducing carbon footprint, lowering costs The use of Alternative Maritime Power systems, like BLUE CONNECT from ERMA FIRST, enables ships to stop running their generators in port and utilise shore power for their needs, thus saving fuel, reducing the environmental and carbon footprint of cargo operations. “The adoption of energy-efficiency measures targets reduction of GHG emissions, optimisation of fuel use, and correcting the energy performance of suboptimal ship designs,” says Kyriacou. ERMA FIRST’s energy-saving devices (ESDs) maximise the propulsive effectiveness of the propeller. ERMA FIRST’s ESDs maximise the propulsive effectiveness of the propeller. Combinations of ESDs FLEXCAP eliminates the hub vortex, while converting some of the rotational energy to thrust FLEXCAP, a propeller cap, eliminates the hub vortex, while converting some of the rotational energy to thrust. FLEXFINS are attached to the hull to correct the flow around the stern preventing boundary layer separation thus reducing drag and losses. FLEXRING is a duct fitted upstream of the propeller that homogenises the axial wake component, while the duct contributes to the thrust by virtue of the lift generated by the accelerating flow over the surfaces. Combinations of ESDs can deliver significant performance gains, lower fuel consumption, reduce GHG emissions and improve a ship’s carbon intensity indicator (CII), says Kyriacou. Embracing carbon capture and storage Carbon capture and storage systems have an important role to play during the transition away from fossil fuels to achieve net-zero. Fossil fuels will be the energy source for ships’ propulsion in the near term because the shift to alternative fuels cannot be implemented instantly due to availability and capacity constraints. ERMA FIRST recognises the need to provide a bridge solution between continued fossil fuel use and the necessity to reduce GHG emissions radically. ERMA FIRST recognises the need to provide a bridge solution. Development of a regulatory framework The ERMA FIRST CARBON FIT post-combustion on-board carbon capture and storage (OCCS) system provides a technically practical solution to achieve GHG emissions reduction, paving the pathway to carbon neutrality. At IMO MEPC.83, a work plan on the development of a regulatory framework for the use of OCCS was agreed. With a scheduled completion by 2028, it is projected that broad technology implementation will follow. ERMA FIRST CARBON FIT post-combustion on-board carbon capture and storage. Maritime and environmental awards As a technology provider with a global reach, ERMA FIRST sets high standards of quality on both equipment and services. ERMA FIRST has won multiple maritime and environmental awards over the years, including: Technical Achievement Award 2013, Lloyd's List Greek Shipping Awards Technology Excellence 2013, Made in Greece Technology Award 2016, GREEN4SEA Bronze Award 2022, HR Awards Technical Achievement Award 2023, Lloyd's List Greek Shipping Awards Sustainability Award 2023, GREEN4SEA Bronze Award 2023, HR Awards Greek Business Champion 2023, Protagonistes Business External Focus 2023, Protagonistes Great Place to Work 2023 R&D expertise of ERMA FIRST A milestone for the company and a proud achievement is the fact that ERMA FIRST belongs to a very small group of companies having won the Technical Achievement Award by Lloyd's List more than once. This reflects the solid R&D expertise of ERMA FIRST and the long-standing and ongoing efforts towards technological excellence and impactful innovations.
FuelEU Maritime came into effect on Jan. 1, 2025. It is part of the European Union’s Fit for 55 package and applies to commercial vessels of 5000GT (gross tonnage) and over used for the transport of cargo or passengers and calling at EU ports. Vessels are required to achieve a greenhouse gas (GHG) intensity of energy below a particular level. That level reduces over time and by 2050 the reduction target is 80% compared to 2020 reference levels. GHG intensity of energy obligations “FuelEU is designed to reduce the energy intensity of fuel used by ships and to drive the uptake of alternative fuels,” says Helen Barden, Director – External Affairs, NorthStandard, an insurer providing Protection and Indemnity (P&I) coverage. She adds, “For vessels that do not meet the GHG intensity of energy obligations, there are options for borrowing compliance from future years, pooling the vessel with better-performing vessel(s) or paying a penalty. For container and passenger ships there are requirements to connect to shore power from 2030.” Ship’s energy intensity FuelEU Maritime measures a ship’s energy intensity over a full reporting year on a well-to-wake basis FuelEU Maritime measures a ship’s energy intensity over a full reporting year on a well-to-wake basis. Well-to-wake therefore includes emissions from well (i.e., production) to tank (i.e., on the ship) plus tank-to-wake (i.e., it propels the ship). Assessing the energy intensity on a well-to-wake basis, rather than simply tank-to-wake, provides a better reflection of the emissions created during the lifecycle of a marine fuel. Wind-assisted propulsion systems “There are many energy efficiency technologies on the market, such as improving the efficiency of hull coatings, or making changes to the bulbous bow or propeller, but these go to improving the energy efficiency and are not included in the calculation to improve the energy intensity of the fuel used,” says Helen Barden. However, wind-assisted propulsion systems receive a Wind Reward Factor in the regulation, which means this technology does impact the vessel’s GHG intensity rating. Of course, zero or near zero fuels and renewable fuels of non-biological origin also go to the GHG intensity rating. Compliance of FuelEU The compliance of FuelEU rests with the DOC holder under the ISM code While the compliance of FuelEU rests with the Document of Compliance (DOC) holder under the International Safety Management (ISM) code, which may well be the ship manager rather than the registered owner, the ship manager will in reality want to pass the liability for compliance on to the ship owner, says Barden. The ship owner (and indeed possibly together with the charterer depending on the length of the charter party and nature of the commercial relationship) will need to produce a strategy for compliance with FuelEU Maritime given there are different options for compliance available, she says. Lower energy intensity fuels and energy sources Helen Barden says payment of the penalty should be the last resort. “Not only is this likely to be the most expensive option, but it also comes with implications for future years in the form of a multiplication factor,” she states. Helen Barden adds, “Whether pooling, using lower energy intensity fuels and energy sources, or borrowing compliance from future years as part of a strategy will depend on many variables and, therefore, a compliance strategy should be given considered thought. This will also impact on the terms of any contracts.” Respect of GHG energy intensity Financial penalties apply to any company that does not meet its compliance obligations There are pooling platforms on the market now, such as Bettersea, which is currently offered to NorthStandard members at a preferential rate. Financial penalties apply to any company that does not meet its compliance obligations in respect of GHG energy intensity. Failing to comply for two or more consecutive years will see the penalty factor multiplied, while failure to present a FuelEU Maritime certificate of compliance for two or more consecutive reporting periods could result in a ship being banned from EU ports. Vessel’s compliance balance If a vessel exceeds the compliance requirements and so has a positive compliance balance for a reporting period, this “surplus” can either be pooled or can be banked for compliance in future years. Parties will need to consider whether charterers will get the full benefit of compliance pooling, banking or borrowing, and how this will work where the charter party does not cover the full reporting year. A vessel’s compliance balance may not be included in more than one pool in the same reporting period, but the vessel may be switched to a different pool in a different reporting period. Responsibility for FuelEU compliance rests The ultimate responsibility for FuelEU compliance rests with the ISM company The ultimate responsibility for FuelEU compliance rests with the ISM company (i.e., the Document of Compliance holder under the ISM Code) and, therefore, careful consideration must be given to the contractual implications of FuelEU Maritime. The Baltic and International Maritime Council (BIMCO) has produced a FuelEU Maritime Clause for Time Charter Parties and a Clause for ship management agreements, too, to help support owners, charterers, and ship managers in this regard. However, these clauses cannot just be inserted without consideration. As mentioned earlier, things like the compliance strategy should be thought through as this will impact the wording used in the clause, says Barden. Advice on the BIMCO clause “The BIMCO clauses are certainly a helpful starting point, but ship managers, ship owners and charterers must consider the terms carefully and, if necessary, make amendments,” says Helen Barden. She adds, “We have been assisting a number of our members with advice on the BIMCO clause in their particular circumstances, and indeed non-industry clauses that have also been proposed.”
Case studies
The accuracy of AIS data used to track ship movements is vital for the analysis of vessel performance in areas such as fuel consumption. OrbitMI has therefore collaborated with Maritime Data on a joint project to enhance the screening of AIS data providers so it can deliver the best quality data for clients. Orbit vessel performance platform “We are continuously striving to optimise data inputs for users of our newly upgraded Orbit vessel performance platform to improve business decision-making." "With this goal in mind, we engaged Maritime Data as a trustworthy partner to contribute its specialist expertise in data procurement for the industry,” says OrbitMI’s Chief Marketing Officer David Levy. Assuring the quality of data inputs Maritime Data supports companies in the maritime ecosystem from concept to contract Maritime Data is a UK-based start-up founded in 2022 by Co-Founders Rory Proud and James Littlejohn with a mission to address the difficulties in sourcing, evaluating, and buying maritime data by acting as a specialised intermediary between buyer and supplier. As a data broker, Maritime Data supports companies in the maritime ecosystem from concept to contract. This enables clients to quickly understand all available solutions relevant to their requirements, evaluate comparable options, and contract with their suppliers of choice. All to minimise the effort required and give time back to the people building solutions needed to tackle the industry's biggest challenges. Buying data is made easier. Accurate customer service Backed by more than 15 years of experience in the sector, Maritime Data has built up an extensive partner network of over 50 maritime intelligence suppliers and 200-plus product offerings in areas such as vessel tracking, emissions calculation, seaborne cargo flows, risk and compliance, port activity, trade statistics, weather, and vessel ownership. “The quality of data being inputted into any model, process, or technology will have a meaningful impact on output,” explains Maritime Data’s Co-Founder James Littlejohn. "It is therefore essential for maritime technology companies to meaningfully evaluate all of their data inputs to ensure their solution provides the most accurate service for their customers." Tackling sourcing challenges Real-time data generated by the AIS is considered the X-axis for any evaluation of vessel operations The joint project has focused on tackling the challenges of acquiring the right AIS data arising from discrepancies in datasets offered by various vendors that make assessment and evaluation difficult for data buyers. Real-time data generated by the Automatic Identification System (AIS) is considered the X-axis for any evaluation of vessel operations and is a fundamental data layer for performance monitoring as it shows position, course, and speed, which can be combined with weather data to optimise operations, according to James Littlejohn. However, AIS is extremely data-heavy with hundreds of millions of data points being generated by thousands of vessels across the globe every day, which requires commensurately massive computational resources to ingest and analyse this data. New vendor evaluation protocol Under the joint project, Maritime Data conducted a comparative assessment of four leading AIS data providers using a new, specially developed evaluation protocol to ascertain the quality of their respective offerings based on carefully designed criteria. Maritime Data was able to take samples of a week of AIS data from each of the four providers and measure each dataset against various benchmarks provided by OrbitMI to help determine the coverage, accuracy and frequency of the respective feeds. A segment of these samples was then taken and split out over 80 different geolocations that were visualised as polygons on a map to show geographical coverage. Heavyweight analytics Independent validation of the supplier selection process enabled this to be conducted more quickly James Littlejohn points out that conducting this process of comparison and evaluation with such vast amounts of data would entail a lot of time and resources for a maritime technology firm such as OrbitMI, causing opportunity cost, while it took Maritime Data about a month to complete the analysis and this time is likely to be shortened in future as the process becomes more efficient. He says that independent validation of the supplier selection process enabled this to be conducted more quickly and without bias in favour of any one data vendor. “The outcome of the process was exactly as we expected and piloting this tool with OrbitMI has given us a springboard for further development and application of the selection protocol. This enabled OrbitMI to proceed with a decision on AIS sourcing secure in the knowledge that the data would fulfill the needs of its customers,” James Littlejohn says. Selecting the ideal AIS data provider At the end of the process, OrbitMI selected Lloyd's List Intelligence as its AIS data provider. “Lloyd's List Intelligence has been a long-time and valued partner of ours,” says Ali Riaz, OrbitMI's CEO. “The quality and versatility of their data offerings, assurances of data accuracy, customer service, and commitment to collaboration compared to the other offerings were unbeatable.” This decision aligns with Lloyd's List Intelligence's strategic vision for the industry. A collaborative, connected approach Tom Richmond, Head of Software & Technology Sales at Lloyd's List Intelligence, elaborates, “Working with innovators like OrbitMI is part of our strategic plan to help the shipping industry move beyond siloed thinking and kick-start a more collaborative, connected approach to integrating seaborne trade in the global supply chain." "We’re happy to support innovation with high-quality products at a price point that stimulates collaboration in the sector.” AIS data quality assurance OrbitMI’s David Levy concludes, “This project demonstrates we are prioritising data quality for our clients by harnessing the power of partnership with a major player." "The AIS data quality assurance process piloted by OrbitMI with Maritime Data will benefit users of the new Orbit platform by ensuring optimised and reliable data inputs covering the global fleet.”
Strengthening trade relations and promoting collaboration between Valenciaport and China. This is the objective with which the Port Authority of València has traveled to China to participate in the 8th edition of the Maritime Silk Road Port International Cooperation Forum 2024, held from June 26 to 28, 2024 in Ningbo (China). The value proposition of the Valencian enclosure as a green, intelligent and innovative HUB of the Mediterranean has been the common thread of the presentation of the PAV in this forum. Advantages of Valenciaport as a strategic port Mar Chao has also described the strategic importance of Valenciaport for the Chinese market During the event, Mar Chao, President of the PAV, had the opportunity to present the competitive advantages of Valenciaport as a strategic port in the center of the Mediterranean (through which 40% of Spanish import/export is channeled) at the service of the business fabric of its area of influence and a link in the logistics chain. Mar Chao has also described the strategic importance of Valenciaport for the Chinese market as a key point of direct connection with Europe that promotes a green growth, market-oriented, with maximum efficiency in services and a complete logistic and multimodal integration. Commercial capacity of Valenciaport During her conference, the President also highlighted the commercial capacity of Valenciaport, with an area of influence of more than 2,000 kilometres that maintains a direct relationship with the main international ports. Cristina Rodríguez, Head of Containers of Valenciaport, accompanies Chao in the forum. Both have held business meetings with Asian companies and institutions, including the new president of the Port of Ningbo, Tao Chengbo. In the framework of this meeting, the representatives of Valenciaport and the Port of Ningbo have signed a memorandum of understanding (MOU) with the aim of strengthening their commercial collaboration. Silk Road Port and Maritime Cooperation Forum The Silk Road Port and Maritime Cooperation Forum of Ningbo (China) in which Valenciaport participates is a platform for open exchange and mutual learning in port development and maritime transport, within the framework of the Belt and Road Initiative. From a respect for the uniqueness of each participating port, the Forum is seen as a tool to foster collaboration in various fields to build bridges between supply and demand in business, investment, technology, talent, information, ports and cultural exchange.
GEM elettronica is proud to announce the conclusion of a strategic project to strengthen Lithuania’s defense capabilities, during which cutting-edge surveillance radars with airspace monitoring function were installed on four patrol ships of the Lithuanian Navy. The contract was executed successfully and within the agreed-upon timelines, thanks to the collaboration between the Italian defence companies Leonardo and GEM elettronica. Advanced radar system The heart of the system is the Columbus MK2 3D multi-mission radar developed and produced in house by GEM Elettronica, specially designed for coastal surveillance and naval applications, made with the latest technologies, which guarantee high detection performances for search and tracking of small and fast targets at both air and sea surface space, high reliability and availability with low maintenance and life cycle costs. It is a compact and lightweight advanced radar system for short- and medium-range detection performing all the functions of surveillance, self-defence, IFF capabilities and weapon designation. The new radar systems were installed on the Lithuanian Flyvefisken (Standard Flex 300) class offshore patrol vessels (OPVs) Žemaitis (P11), Dzūkas (P12), Aukštaitis (P14) and Sėlis (P15). Working effectively together The main role of the new equipment is to ensure the safety of ships when navigating in narrow passages The main role of the new equipment is to ensure the safety of ships when navigating in narrow passages (e.g., straits, port channels) and in the open sea, as well as in search and rescue missions. The systems will allow objects to be detected up to 100 kilometers away. The Commander of the Lithuanian Naval Forces Sea, Captain Giedrius Premeneckas underlined: “The successful implementation of this project represents a significant step in strengthening the capabilities of the Navy’s patrol vessels and significantly increasing our ability to carry out assigned tasks and work effectively together with NATO allies.” The President of GEM elettronica Ing. Antonio Bontempi answered “We are delighted to have successfully contributed to the realization of this strategic project. We are also proud of what achieved by our R&D and Production teams who worked together with passion and tenacity to ensure the project was achieved within the expected timescales.”
Höegh Autoliners has revolutionised maritime transport with its Aurora Class vessels, marking significant progress toward sustainable deep-sea shipping. These Pure Car and Truck Carriers (PCTCs) are designed to be the largest and most environmentally friendly in their class. Notably, the final four ships in this 12-vessel series are set to operate on sustainable ammonia, a zero-carbon fuel, upon their delivery in 2027. Aurora Class vessels Aurora Class vessels are initially running on LNG with the flexibility to transition to ammonia and methanol The Aurora Class vessels are initially running on liquefied natural gas (LNG) with the flexibility to transition to ammonia and methanol as these fuels become more accessible. This adaptability is emphasised by the ships’ receipt of DNV’s ammonia- and methanol-ready notations, a first in the PCTC segment. The final four vessels will feature MAN Energy Solutions’ two-stroke engines capable of being fuelled by ammonia, positioning them as pioneers in zero-GHG emission maritime transport. TGE Marine’s expertise A key enabler of this technological leap is TGE Marine, whose advanced tank designs and fuel gas handling solutions are at the core of the vessels’ ammonia propulsion capabilities. TGE Marine’s expertise in designing and engineering maritime gas systems has made them a global pioneer in gas containment and fuel supply technologies. Their tanks are specifically developed to safely store ammonia in maritime conditions, while their fuel gas systems are among the most advanced in the industry ensuring reliable fuel management, safe operations, and seamless engine integration. These solutions exceed the stringent safety and performance standards required for ammonia as a marine fuel. New ammonia fuel supply system TGE Marine has already supplied tanks and fuel gas systems to the first eight Aurora class vessels TGE Marine has already supplied tanks and fuel gas systems to the first eight Aurora class vessels, and within the final four vessels, the fuel supply system is intended to handle ammonia fuel which allow for the vessels to be an engineering front runner in the industry. The new ammonia fuel supply system comes among others with a reliquefaction system, a gas combustion unit (GCU) and an ammonia release and mitigation systems (ARMS). Aspects of TGE Marine’s contribution The following expands on the specific aspects of TGE Marine’s contribution to the vessels: Fuel Supply System: The fuel supply system is streamlined to support the main engine operation in an optimum manner allowing a reliable and stable operation with ammonia as fuel. The design of the system is addressing the demand to increase ammonia integrity and to allow safe operation incl. maintenance. Key design features are the utilisation of sealless pumps, high integrity equipment and automation resp. remote operation. Boil-off Gas (BOG) Treatment: The heat ingress into the ammonia storage tank will lead to evapouration of ammonia. To keep the tank pressure within allowable limit the vapour, the BOG, is routed from the type-c tank’s vapour space to the BOG Treatment System. The BOG Treatment system consists of two fully independent methods to manage the tank pressure, i.e., the Reliquefaction System and the Gas Combustion Unit (GCU). Reliquefaction System: Onboard reliquefaction systems are engineered to recondense the ammonia vapour that results from heat ingress into the storage tanks and system operation. Gas Combustion Unit: As with all systems, TGE Marine also ensure that in an unlikely event that the reliquefaction system would fail, a secondary ‘back up’ system would kick in. The method chosen for this set up a gas combustion unit (GCU). This method burns the boil off gas, and this allows the tank temperature and tank pressure to remain within the limits. The gas combustion unit can support also the treatment of nitrogen ammonia mixtures and non-standard operations, such as gas-freeing of systems for maintenance preventing the release of ammonia to the atmosphere. Safety Systems: Key for operating a vessel with ammonia as fuel is the safe operation taking the toxicity of ammonia into consideration. TGE Marine has implemented safety systems and measures into the design of the system. Risk assessments accompany the design and execution of the project at every stage. Ammonia recovery: A key element of the safe operation is the handling of potential operational and emergency releases originating from the fuel supply system and engine purge operations. For this purpose, an ammonia recovery system is applied to reduce the ammonia quantities being routed to the ammonia release mitigation system. Ammonia Release Mitigation System: The ammonia release mitigation system developed by TGE Marine, is reducing the ammonia quantity released to the atmosphere and ensures that ammonia concentrations are below health and safety limits. Primary benefits of configuration To underline the benefits of the system, these following can be listed as primary benefits of using such configuration: Fuel Efficiency: By applying an efficient ammonia fuel supply system and ammonia engine Environmental Compliance: Minimising emissions of ammonia gas into the atmosphere reduces the vessel’s environmental footprint and helps comply with stringent emissions regulations Safety and Stability: The system ensures stable operation, reducing the risk to personnel and enhancing onboard safety Operational Flexibility: This technology supports extended voyages without fuel losses and allows better management of varying fuel demands during different operational profiles New standard for sustainability in maritime transport Beyond propulsion, the Aurora Class vessels incorporate several eco-friendly features, some include 1,500 square metres of solar panels and the capability to connect to electric shore power, enabling emissions-free port operations. With these advancements, Höegh Autoliners, together with key partners like TGE Marine, is not only reducing its carbon footprint but also setting a new standard for sustainability in maritime transport, steering the industry toward a greener future.
Team Electric rose to some special challenges in its successful completion of electrical installation and refit work during Royal Caribbean’s recent high profile drydocking and ‘amplification’ of Allure of the Seas. Despite heavy weather, tight deadlines, and complex coordination across multiple contractors and workstreams, Team Electric showcased its hallmark adaptability and technical expertise to deliver the full scope of work on schedule. Three turnkey suppliers With a total workforce of 60 skilled electricians on site, Team Electric was engaged separately by three turnkey suppliers — Almaco, Makinen, and LMG — to execute electrical works across hotel areas, galleys, and public spaces on board the cruise ship. The project marked a return to familiar territory for Team Electric, which was also involved in the original construction of Allure of the Seas in Turku Shipyard in 2009. Project highlights Team Electric delivered full electrical works for the new Mason Jar restaurant and bar Achievements included the installation of 121 kilometres of electrical cabling and 4,500 metres of cable trays, across a project involving key technical areas as well as substantial hotel work. Among tasks that extended to 600 individual material line items, Team Electric fitted nearly 2,000 lights. The company’s hotel-side scope covered 61 new cabins on decks 11, 12, and 14 that were built within a prefabricated aluminium block and craned onto the ship. These new spaces included corridors, AC rooms, and associated technical infrastructure. In addition, Team Electric delivered full electrical works for the new Mason Jar restaurant and bar, as well as several refurbished galley spaces and three public areas including a Crown Lounge and a teens’ gaming zone. On the technical side, Team Electric upgraded a substantial portion of the ship’s navigation and communication systems, including the full cabling of the bridge with 9 kilometres of new wiring. A turnkey delivery of Fugro’s OceanStar system included not just cabling but also installation, commissioning, and user training, led by certified Team Electric engineers. Rising to the challenge “The weather was brutal. 30 days of torrential rain in a 40-day dry dock,” said Daniel Brown, Project Manager at Team Electric. “It had a knock-on effect on every trade, but we managed to push through and keep the program on track.” Meticulous planning and on-the-ground flexibility, Team Electric met all critical deadlines High winds frequently delayed crane operations and other key activities. Yet, through meticulous planning and on-the-ground flexibility, Team Electric met all critical deadlines. The project’s compressed dry dock period presented a further challenge. As Caj Persson, Technical Project Lead, explained: “They cut the dry dock time compared to the sister vessel Oasis of the Seas by over 10 days. That meant everything had to be done faster, with no compromise on quality.” Reliability pays Team Electric’s proven reputation in cruise ship refits was a key factor in securing the contract. “We’re well known in the industry for delivering complex and multi-faceted electrical refits, especially cabins and public areas,” said Daniel Brown. “We’re not always the cheapest, but clients know we get the job done on time and to the highest standards.” Fourth contractor with no onboard electrical team asked Team Electric to step in and support their work That reliability also paid off during the refit, when a fourth contractor with no onboard electrical team asked Team Electric to step in and support their work, sparking another relationship that is set to continue beyond this project. The working relationship with Royal Caribbean also proved crucial. “We know the fleet, we’ve been with them since these keels were laid,” said Persson. “That familiarity, and our long-standing relationship with partners like Foreship, made the coordination smoother, even under pressure.” Integrated installation Unlike newbuilds, refits present constantly shifting priorities and constraints. As Daniel Brown explained: “In public areas especially, we can’t even install light fittings until the ceiling is in. It takes extreme coordination. Every task affects the next.” From cabin design to bridge cabling, and from substations to galleys, the Allure of the Seas project exemplifies Team Electric’s full-spectrum capabilities. By blending technical know-how with practical execution, the company once again proved why it's the preferred electrical partner for cruise ship refits worldwide.
San Francisco-based maritime technology company - Sofar Ocean announces a partnership with the U.S. Naval Meteorology and Oceanography Command’s (CNMOC) Fleet Weather centres in Norfolk (FWC-N) and San Diego (FWC-SD). Wayfinder platform FWC-N and FWC-SD, the Navy’s two primary weather forecasting centres, are piloting Sofar’s Wayfinder platform to support the routing of naval vessels at sea. The FWCs are utilising Wayfinder to identify safe and efficient route options powered by real-time ocean weather data for Military Sealift Command (MSC) ships. Situational awareness Tim Janssen, Co-Dounder and CEO of Sofar, said, "Wayfinder will empower the Navy to enhance situational awareness at sea and leverage data-driven optimisation to continuously identify safe and efficient routing strategies." He adds, "Powered by our real-time ocean weather sensor network, Wayfinder will help the Navy scale its routing operations to support a heterogeneous fleet operating in conditions made more extreme by the effects of climate change." CRADA The platform displays real-time observational data from Sofar’s global network of Spotter buoys The Navy is evaluating Wayfinder under CNMOC and Sofar’s five-year Cooperative Research and Development Agreement (CRADA) signed in July 2023. Wayfinder reduces manual tasks for forecasters and routers by automatically generating a forecast along a vessel’s route. The platform displays real-time observational data from Sofar’s global network of Spotter buoys to reduce weather uncertainty for route optimisation, and predict unwanted vessel motions during a voyage. Real-time wave and weather observations The availability of accurate real-time wave and weather observations helps Captains and shoreside personnel validate forecast models and examine multiple route options more efficiently, streamlining a historically complex and arduous process. Lea Locke-Wynn, Undersea Warfare Technical Lead for CNMOC’s Future Capabilities Department, said, "A key focus area for the Naval Oceanography enterprise is fostering a culture of innovation through collaboration with our commercial partners." Vessel-specific guidance Lea Locke-Wynn adds, "Our ongoing CRADA with Sofar Ocean is a perfect example of how our partnerships can leverage the leading edge in industry to further Department of Defence operations." As the number of naval vessels at sea, including experimental and autonomous ships, continues to increase, forecasters and routers will have less time to spend manually producing vessel-specific guidance. Automated forecast-on-route guidance More efficient routing empowers FWC personnel to focus on challenging, mission-critical tasks Wayfinder helps fill this operational gap, enabling FWC-N and FWC-SD to more efficiently support a large fleet in real-time with automated forecast-on-route guidance. More efficient routing empowers FWC personnel to focus on challenging, mission-critical tasks that require their unique expertise. Streamlined decisions Captain Erin Ceschini, Commanding Officer, FWC-SD, stated, "By using Wayfinder, we’re able to better visualise our ships’ routes, and make safer and more streamlined decisions on route, speed, and heading." Captain Erin Ceschini adds, "Wayfinder has the potential to be a critical component of our day-to-day operations and a key driver of safe routing as we contend with an increasingly unpredictable weather landscape."
The accuracy of AIS data used to track ship movements is vital for the analysis of vessel performance in areas such as fuel consumption. OrbitMI has therefore collaborated with Maritime Data on a joint project to enhance the screening of AIS data providers so it can deliver the best quality data for clients. Orbit vessel performance platform “We are continuously striving to optimise data inputs for users of our newly upgraded Orbit vessel performance platform to improve business decision-making." "With this goal in mind, we engaged Maritime Data as a trustworthy partner to contribute its specialist expertise in data procurement for the industry,” says OrbitMI’s Chief Marketing Officer David Levy. Assuring the quality of data inputs Maritime Data supports companies in the maritime ecosystem from concept to contract Maritime Data is a UK-based start-up founded in 2022 by Co-Founders Rory Proud and James Littlejohn with a mission to address the difficulties in sourcing, evaluating, and buying maritime data by acting as a specialised intermediary between buyer and supplier. As a data broker, Maritime Data supports companies in the maritime ecosystem from concept to contract. This enables clients to quickly understand all available solutions relevant to their requirements, evaluate comparable options, and contract with their suppliers of choice. All to minimise the effort required and give time back to the people building solutions needed to tackle the industry's biggest challenges. Buying data is made easier. Accurate customer service Backed by more than 15 years of experience in the sector, Maritime Data has built up an extensive partner network of over 50 maritime intelligence suppliers and 200-plus product offerings in areas such as vessel tracking, emissions calculation, seaborne cargo flows, risk and compliance, port activity, trade statistics, weather, and vessel ownership. “The quality of data being inputted into any model, process, or technology will have a meaningful impact on output,” explains Maritime Data’s Co-Founder James Littlejohn. "It is therefore essential for maritime technology companies to meaningfully evaluate all of their data inputs to ensure their solution provides the most accurate service for their customers." Tackling sourcing challenges Real-time data generated by the AIS is considered the X-axis for any evaluation of vessel operations The joint project has focused on tackling the challenges of acquiring the right AIS data arising from discrepancies in datasets offered by various vendors that make assessment and evaluation difficult for data buyers. Real-time data generated by the Automatic Identification System (AIS) is considered the X-axis for any evaluation of vessel operations and is a fundamental data layer for performance monitoring as it shows position, course, and speed, which can be combined with weather data to optimise operations, according to James Littlejohn. However, AIS is extremely data-heavy with hundreds of millions of data points being generated by thousands of vessels across the globe every day, which requires commensurately massive computational resources to ingest and analyse this data. New vendor evaluation protocol Under the joint project, Maritime Data conducted a comparative assessment of four leading AIS data providers using a new, specially developed evaluation protocol to ascertain the quality of their respective offerings based on carefully designed criteria. Maritime Data was able to take samples of a week of AIS data from each of the four providers and measure each dataset against various benchmarks provided by OrbitMI to help determine the coverage, accuracy and frequency of the respective feeds. A segment of these samples was then taken and split out over 80 different geolocations that were visualised as polygons on a map to show geographical coverage. Heavyweight analytics Independent validation of the supplier selection process enabled this to be conducted more quickly James Littlejohn points out that conducting this process of comparison and evaluation with such vast amounts of data would entail a lot of time and resources for a maritime technology firm such as OrbitMI, causing opportunity cost, while it took Maritime Data about a month to complete the analysis and this time is likely to be shortened in future as the process becomes more efficient. He says that independent validation of the supplier selection process enabled this to be conducted more quickly and without bias in favour of any one data vendor. “The outcome of the process was exactly as we expected and piloting this tool with OrbitMI has given us a springboard for further development and application of the selection protocol. This enabled OrbitMI to proceed with a decision on AIS sourcing secure in the knowledge that the data would fulfill the needs of its customers,” James Littlejohn says. Selecting the ideal AIS data provider At the end of the process, OrbitMI selected Lloyd's List Intelligence as its AIS data provider. “Lloyd's List Intelligence has been a long-time and valued partner of ours,” says Ali Riaz, OrbitMI's CEO. “The quality and versatility of their data offerings, assurances of data accuracy, customer service, and commitment to collaboration compared to the other offerings were unbeatable.” This decision aligns with Lloyd's List Intelligence's strategic vision for the industry. A collaborative, connected approach Tom Richmond, Head of Software & Technology Sales at Lloyd's List Intelligence, elaborates, “Working with innovators like OrbitMI is part of our strategic plan to help the shipping industry move beyond siloed thinking and kick-start a more collaborative, connected approach to integrating seaborne trade in the global supply chain." "We’re happy to support innovation with high-quality products at a price point that stimulates collaboration in the sector.” AIS data quality assurance OrbitMI’s David Levy concludes, “This project demonstrates we are prioritising data quality for our clients by harnessing the power of partnership with a major player." "The AIS data quality assurance process piloted by OrbitMI with Maritime Data will benefit users of the new Orbit platform by ensuring optimised and reliable data inputs covering the global fleet.”
Strengthening trade relations and promoting collaboration between Valenciaport and China. This is the objective with which the Port Authority of València has traveled to China to participate in the 8th edition of the Maritime Silk Road Port International Cooperation Forum 2024, held from June 26 to 28, 2024 in Ningbo (China). The value proposition of the Valencian enclosure as a green, intelligent and innovative HUB of the Mediterranean has been the common thread of the presentation of the PAV in this forum. Advantages of Valenciaport as a strategic port Mar Chao has also described the strategic importance of Valenciaport for the Chinese market During the event, Mar Chao, President of the PAV, had the opportunity to present the competitive advantages of Valenciaport as a strategic port in the center of the Mediterranean (through which 40% of Spanish import/export is channeled) at the service of the business fabric of its area of influence and a link in the logistics chain. Mar Chao has also described the strategic importance of Valenciaport for the Chinese market as a key point of direct connection with Europe that promotes a green growth, market-oriented, with maximum efficiency in services and a complete logistic and multimodal integration. Commercial capacity of Valenciaport During her conference, the President also highlighted the commercial capacity of Valenciaport, with an area of influence of more than 2,000 kilometres that maintains a direct relationship with the main international ports. Cristina Rodríguez, Head of Containers of Valenciaport, accompanies Chao in the forum. Both have held business meetings with Asian companies and institutions, including the new president of the Port of Ningbo, Tao Chengbo. In the framework of this meeting, the representatives of Valenciaport and the Port of Ningbo have signed a memorandum of understanding (MOU) with the aim of strengthening their commercial collaboration. Silk Road Port and Maritime Cooperation Forum The Silk Road Port and Maritime Cooperation Forum of Ningbo (China) in which Valenciaport participates is a platform for open exchange and mutual learning in port development and maritime transport, within the framework of the Belt and Road Initiative. From a respect for the uniqueness of each participating port, the Forum is seen as a tool to foster collaboration in various fields to build bridges between supply and demand in business, investment, technology, talent, information, ports and cultural exchange.
GEM elettronica is proud to announce the conclusion of a strategic project to strengthen Lithuania’s defense capabilities, during which cutting-edge surveillance radars with airspace monitoring function were installed on four patrol ships of the Lithuanian Navy. The contract was executed successfully and within the agreed-upon timelines, thanks to the collaboration between the Italian defence companies Leonardo and GEM elettronica. Advanced radar system The heart of the system is the Columbus MK2 3D multi-mission radar developed and produced in house by GEM Elettronica, specially designed for coastal surveillance and naval applications, made with the latest technologies, which guarantee high detection performances for search and tracking of small and fast targets at both air and sea surface space, high reliability and availability with low maintenance and life cycle costs. It is a compact and lightweight advanced radar system for short- and medium-range detection performing all the functions of surveillance, self-defence, IFF capabilities and weapon designation. The new radar systems were installed on the Lithuanian Flyvefisken (Standard Flex 300) class offshore patrol vessels (OPVs) Žemaitis (P11), Dzūkas (P12), Aukštaitis (P14) and Sėlis (P15). Working effectively together The main role of the new equipment is to ensure the safety of ships when navigating in narrow passages The main role of the new equipment is to ensure the safety of ships when navigating in narrow passages (e.g., straits, port channels) and in the open sea, as well as in search and rescue missions. The systems will allow objects to be detected up to 100 kilometers away. The Commander of the Lithuanian Naval Forces Sea, Captain Giedrius Premeneckas underlined: “The successful implementation of this project represents a significant step in strengthening the capabilities of the Navy’s patrol vessels and significantly increasing our ability to carry out assigned tasks and work effectively together with NATO allies.” The President of GEM elettronica Ing. Antonio Bontempi answered “We are delighted to have successfully contributed to the realization of this strategic project. We are also proud of what achieved by our R&D and Production teams who worked together with passion and tenacity to ensure the project was achieved within the expected timescales.”
Höegh Autoliners has revolutionised maritime transport with its Aurora Class vessels, marking significant progress toward sustainable deep-sea shipping. These Pure Car and Truck Carriers (PCTCs) are designed to be the largest and most environmentally friendly in their class. Notably, the final four ships in this 12-vessel series are set to operate on sustainable ammonia, a zero-carbon fuel, upon their delivery in 2027. Aurora Class vessels Aurora Class vessels are initially running on LNG with the flexibility to transition to ammonia and methanol The Aurora Class vessels are initially running on liquefied natural gas (LNG) with the flexibility to transition to ammonia and methanol as these fuels become more accessible. This adaptability is emphasised by the ships’ receipt of DNV’s ammonia- and methanol-ready notations, a first in the PCTC segment. The final four vessels will feature MAN Energy Solutions’ two-stroke engines capable of being fuelled by ammonia, positioning them as pioneers in zero-GHG emission maritime transport. TGE Marine’s expertise A key enabler of this technological leap is TGE Marine, whose advanced tank designs and fuel gas handling solutions are at the core of the vessels’ ammonia propulsion capabilities. TGE Marine’s expertise in designing and engineering maritime gas systems has made them a global pioneer in gas containment and fuel supply technologies. Their tanks are specifically developed to safely store ammonia in maritime conditions, while their fuel gas systems are among the most advanced in the industry ensuring reliable fuel management, safe operations, and seamless engine integration. These solutions exceed the stringent safety and performance standards required for ammonia as a marine fuel. New ammonia fuel supply system TGE Marine has already supplied tanks and fuel gas systems to the first eight Aurora class vessels TGE Marine has already supplied tanks and fuel gas systems to the first eight Aurora class vessels, and within the final four vessels, the fuel supply system is intended to handle ammonia fuel which allow for the vessels to be an engineering front runner in the industry. The new ammonia fuel supply system comes among others with a reliquefaction system, a gas combustion unit (GCU) and an ammonia release and mitigation systems (ARMS). Aspects of TGE Marine’s contribution The following expands on the specific aspects of TGE Marine’s contribution to the vessels: Fuel Supply System: The fuel supply system is streamlined to support the main engine operation in an optimum manner allowing a reliable and stable operation with ammonia as fuel. The design of the system is addressing the demand to increase ammonia integrity and to allow safe operation incl. maintenance. Key design features are the utilisation of sealless pumps, high integrity equipment and automation resp. remote operation. Boil-off Gas (BOG) Treatment: The heat ingress into the ammonia storage tank will lead to evapouration of ammonia. To keep the tank pressure within allowable limit the vapour, the BOG, is routed from the type-c tank’s vapour space to the BOG Treatment System. The BOG Treatment system consists of two fully independent methods to manage the tank pressure, i.e., the Reliquefaction System and the Gas Combustion Unit (GCU). Reliquefaction System: Onboard reliquefaction systems are engineered to recondense the ammonia vapour that results from heat ingress into the storage tanks and system operation. Gas Combustion Unit: As with all systems, TGE Marine also ensure that in an unlikely event that the reliquefaction system would fail, a secondary ‘back up’ system would kick in. The method chosen for this set up a gas combustion unit (GCU). This method burns the boil off gas, and this allows the tank temperature and tank pressure to remain within the limits. The gas combustion unit can support also the treatment of nitrogen ammonia mixtures and non-standard operations, such as gas-freeing of systems for maintenance preventing the release of ammonia to the atmosphere. Safety Systems: Key for operating a vessel with ammonia as fuel is the safe operation taking the toxicity of ammonia into consideration. TGE Marine has implemented safety systems and measures into the design of the system. Risk assessments accompany the design and execution of the project at every stage. Ammonia recovery: A key element of the safe operation is the handling of potential operational and emergency releases originating from the fuel supply system and engine purge operations. For this purpose, an ammonia recovery system is applied to reduce the ammonia quantities being routed to the ammonia release mitigation system. Ammonia Release Mitigation System: The ammonia release mitigation system developed by TGE Marine, is reducing the ammonia quantity released to the atmosphere and ensures that ammonia concentrations are below health and safety limits. Primary benefits of configuration To underline the benefits of the system, these following can be listed as primary benefits of using such configuration: Fuel Efficiency: By applying an efficient ammonia fuel supply system and ammonia engine Environmental Compliance: Minimising emissions of ammonia gas into the atmosphere reduces the vessel’s environmental footprint and helps comply with stringent emissions regulations Safety and Stability: The system ensures stable operation, reducing the risk to personnel and enhancing onboard safety Operational Flexibility: This technology supports extended voyages without fuel losses and allows better management of varying fuel demands during different operational profiles New standard for sustainability in maritime transport Beyond propulsion, the Aurora Class vessels incorporate several eco-friendly features, some include 1,500 square metres of solar panels and the capability to connect to electric shore power, enabling emissions-free port operations. With these advancements, Höegh Autoliners, together with key partners like TGE Marine, is not only reducing its carbon footprint but also setting a new standard for sustainability in maritime transport, steering the industry toward a greener future.
Team Electric rose to some special challenges in its successful completion of electrical installation and refit work during Royal Caribbean’s recent high profile drydocking and ‘amplification’ of Allure of the Seas. Despite heavy weather, tight deadlines, and complex coordination across multiple contractors and workstreams, Team Electric showcased its hallmark adaptability and technical expertise to deliver the full scope of work on schedule. Three turnkey suppliers With a total workforce of 60 skilled electricians on site, Team Electric was engaged separately by three turnkey suppliers — Almaco, Makinen, and LMG — to execute electrical works across hotel areas, galleys, and public spaces on board the cruise ship. The project marked a return to familiar territory for Team Electric, which was also involved in the original construction of Allure of the Seas in Turku Shipyard in 2009. Project highlights Team Electric delivered full electrical works for the new Mason Jar restaurant and bar Achievements included the installation of 121 kilometres of electrical cabling and 4,500 metres of cable trays, across a project involving key technical areas as well as substantial hotel work. Among tasks that extended to 600 individual material line items, Team Electric fitted nearly 2,000 lights. The company’s hotel-side scope covered 61 new cabins on decks 11, 12, and 14 that were built within a prefabricated aluminium block and craned onto the ship. These new spaces included corridors, AC rooms, and associated technical infrastructure. In addition, Team Electric delivered full electrical works for the new Mason Jar restaurant and bar, as well as several refurbished galley spaces and three public areas including a Crown Lounge and a teens’ gaming zone. On the technical side, Team Electric upgraded a substantial portion of the ship’s navigation and communication systems, including the full cabling of the bridge with 9 kilometres of new wiring. A turnkey delivery of Fugro’s OceanStar system included not just cabling but also installation, commissioning, and user training, led by certified Team Electric engineers. Rising to the challenge “The weather was brutal. 30 days of torrential rain in a 40-day dry dock,” said Daniel Brown, Project Manager at Team Electric. “It had a knock-on effect on every trade, but we managed to push through and keep the program on track.” Meticulous planning and on-the-ground flexibility, Team Electric met all critical deadlines High winds frequently delayed crane operations and other key activities. Yet, through meticulous planning and on-the-ground flexibility, Team Electric met all critical deadlines. The project’s compressed dry dock period presented a further challenge. As Caj Persson, Technical Project Lead, explained: “They cut the dry dock time compared to the sister vessel Oasis of the Seas by over 10 days. That meant everything had to be done faster, with no compromise on quality.” Reliability pays Team Electric’s proven reputation in cruise ship refits was a key factor in securing the contract. “We’re well known in the industry for delivering complex and multi-faceted electrical refits, especially cabins and public areas,” said Daniel Brown. “We’re not always the cheapest, but clients know we get the job done on time and to the highest standards.” Fourth contractor with no onboard electrical team asked Team Electric to step in and support their work That reliability also paid off during the refit, when a fourth contractor with no onboard electrical team asked Team Electric to step in and support their work, sparking another relationship that is set to continue beyond this project. The working relationship with Royal Caribbean also proved crucial. “We know the fleet, we’ve been with them since these keels were laid,” said Persson. “That familiarity, and our long-standing relationship with partners like Foreship, made the coordination smoother, even under pressure.” Integrated installation Unlike newbuilds, refits present constantly shifting priorities and constraints. As Daniel Brown explained: “In public areas especially, we can’t even install light fittings until the ceiling is in. It takes extreme coordination. Every task affects the next.” From cabin design to bridge cabling, and from substations to galleys, the Allure of the Seas project exemplifies Team Electric’s full-spectrum capabilities. By blending technical know-how with practical execution, the company once again proved why it's the preferred electrical partner for cruise ship refits worldwide.
San Francisco-based maritime technology company - Sofar Ocean announces a partnership with the U.S. Naval Meteorology and Oceanography Command’s (CNMOC) Fleet Weather centres in Norfolk (FWC-N) and San Diego (FWC-SD). Wayfinder platform FWC-N and FWC-SD, the Navy’s two primary weather forecasting centres, are piloting Sofar’s Wayfinder platform to support the routing of naval vessels at sea. The FWCs are utilising Wayfinder to identify safe and efficient route options powered by real-time ocean weather data for Military Sealift Command (MSC) ships. Situational awareness Tim Janssen, Co-Dounder and CEO of Sofar, said, "Wayfinder will empower the Navy to enhance situational awareness at sea and leverage data-driven optimisation to continuously identify safe and efficient routing strategies." He adds, "Powered by our real-time ocean weather sensor network, Wayfinder will help the Navy scale its routing operations to support a heterogeneous fleet operating in conditions made more extreme by the effects of climate change." CRADA The platform displays real-time observational data from Sofar’s global network of Spotter buoys The Navy is evaluating Wayfinder under CNMOC and Sofar’s five-year Cooperative Research and Development Agreement (CRADA) signed in July 2023. Wayfinder reduces manual tasks for forecasters and routers by automatically generating a forecast along a vessel’s route. The platform displays real-time observational data from Sofar’s global network of Spotter buoys to reduce weather uncertainty for route optimisation, and predict unwanted vessel motions during a voyage. Real-time wave and weather observations The availability of accurate real-time wave and weather observations helps Captains and shoreside personnel validate forecast models and examine multiple route options more efficiently, streamlining a historically complex and arduous process. Lea Locke-Wynn, Undersea Warfare Technical Lead for CNMOC’s Future Capabilities Department, said, "A key focus area for the Naval Oceanography enterprise is fostering a culture of innovation through collaboration with our commercial partners." Vessel-specific guidance Lea Locke-Wynn adds, "Our ongoing CRADA with Sofar Ocean is a perfect example of how our partnerships can leverage the leading edge in industry to further Department of Defence operations." As the number of naval vessels at sea, including experimental and autonomous ships, continues to increase, forecasters and routers will have less time to spend manually producing vessel-specific guidance. Automated forecast-on-route guidance More efficient routing empowers FWC personnel to focus on challenging, mission-critical tasks Wayfinder helps fill this operational gap, enabling FWC-N and FWC-SD to more efficiently support a large fleet in real-time with automated forecast-on-route guidance. More efficient routing empowers FWC personnel to focus on challenging, mission-critical tasks that require their unique expertise. Streamlined decisions Captain Erin Ceschini, Commanding Officer, FWC-SD, stated, "By using Wayfinder, we’re able to better visualise our ships’ routes, and make safer and more streamlined decisions on route, speed, and heading." Captain Erin Ceschini adds, "Wayfinder has the potential to be a critical component of our day-to-day operations and a key driver of safe routing as we contend with an increasingly unpredictable weather landscape."


Round table discussion
Given the diverse stakeholders in the maritime industry, it is understandable that collaboration is a challenge. However, the interconnected ecosystem of maritime makes collaboration essential. From ship owners and operators to port authorities, from shippers to shipbuilders, from classification societies to marine service providers and others, there are vast opportunities to work together and cooperate. To gain insight, we asked our Expert Panel Roundtable: How can the maritime industry increase collaboration, and what are the benefits?
Achieving optimal return on investment (ROI) for a maritime company involves a strategic combination of operational efficiency, revenue enhancement, cost control, careful financial management, attention to sustainability and regulatory compliance, and other factors. Given all the variables in play, profitability can be elusive, but our Expert Panel Roundtable has some ideas. We asked: How can maritime companies maximise return on investment (ROI)?
Products

