Virus control

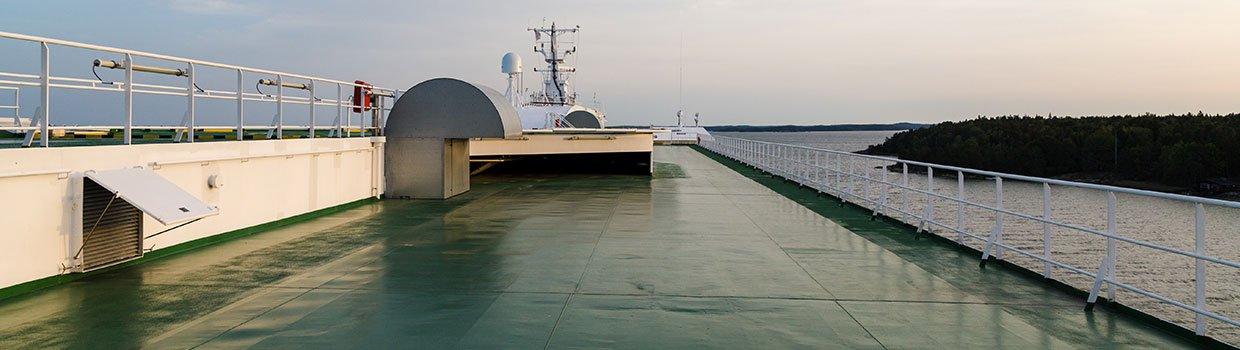
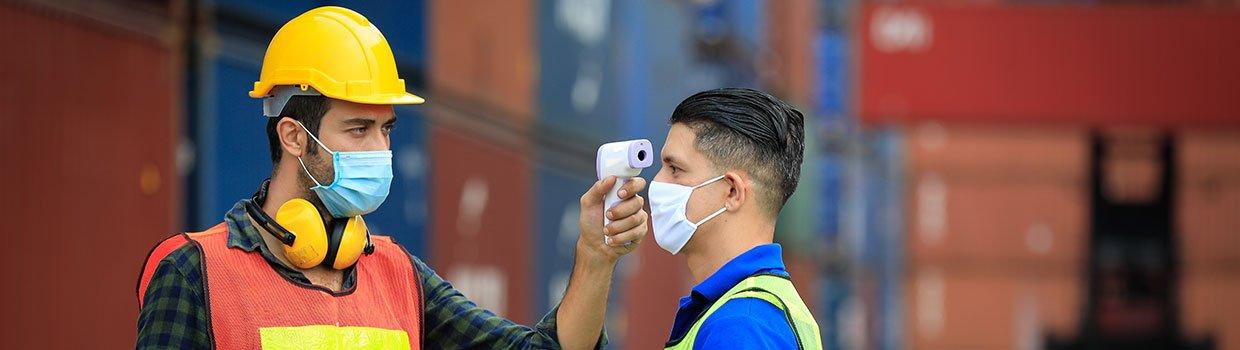


News
Marine Evacuation Systems (MES) served by liferafts is an efficient and widely used method for mass evacuation at sea. With passenger ship capacities increasing, the ability of MES to evacuate hundreds of people in a matter of has been tested exhaustively in Beaufort Sea State 6 conditions. MES and liferafts MES and liferafts – five things they need to know To be compliant, liferafts must be designed in accordance with SOLAS Chapter lll and the LSA Code. All VIKING liferafts are compliant with these standards and are fully approved for use with MES by the following authorities: EU Maritime Equipment Directive, Russian Maritime Register of Shipping, Canadian Coast Guard and Australian Maritime Safety Authority. MES is mostly deployed on passenger vessels as a supplement or replacement for lifeboats. Chutes and slides are the two most common technologies for getting evacuees from deck to sea level. MES solutions are also available for the offshore sector, where evacuation heights can go as high as 81m. Here, the liferafts are served by a zig-zag chute made from aramid. Liferafts are subjected to specific tests at intervals according to international regulations to ensure their readiness for use with the MES: Gas inflation stress test every 5 years using own CO2 cylinder; necessary additional pressure test at at 11 years, then annually; floor seam test to check seams of the internal floor conducted at 10 years, then annually. In addition to Factory Acceptance Tests, type approvals and performance verification at its dedicated shoreside facilities, VIKING’s Development Test and Verification (DTV) department undertakes sea trials in northern waters – typically at depths of 200-300 metres off the coasts of Norway, the Shetland Islands, the Faroe Islands and Iceland. While not addressed separately by the Polar Code, MES must be operational at the Polar Service Temperature (at least 10°C colder than the lowest Mean Day Low Temperature), be protected from ice and use enclosed survival craft. MES and VIKING – five things worth knowing VIKING has placed 1,500 marine evacuation systems in operation on passenger ships over a 30-year period and an additional 500+ SES-type systems for offshore assets. VIKING supplies Chute and Dual Chute Systems, Mini Chute Systems, Offshore Chute Systems, Slide Systems, Mini Slide Systems, and Direct boarding liferafts. In fact, a VIKING MES is available to meet the needs of everything from a superyacht or ferry to the largest cruise ships or offshore platforms in the world. VIKING offers MES solutions in versions designed to evacuate 51 persons to the highest capacity chute systems on the market, handling over 900 passengers in 30 minutes. For the offshore systems, the requirement followed is 10 minutes. Beyond SOLAS compliance, all VIKING offshore evacuation systems are constructed according to specifications outlined in the MODU Code, NORSOK, PSA (Petroleum Safety Authority Norway) regulations, NMA regulations, and more. Only VIKING can offer solutions for all offshore installation types, including wind farm substations. Each MES requires only 1-2 crew to deploy. Systems feature chutes with 1-4 inflatable liferafts attached in a stowage box launched from the evacuation deck to sea level. VIKING liferafts - five things it’s nice to know MES and all associated liferafts from VIKING are available under extended 30-month service period agreements. Fully approved according to SOLAS and HSC codes, VIKING ‘S30’ liferafts have been shown to reduce maintenance costs without compromising safety. VIKING’s range of throw-overboard and davit-launchable liferafts is available in standard versions and in automatically self-righting versions with stowage heights up to 60m. Due to restrictions placed on training facilities during COVID-19, VIKING developed a series of additional e-learning tools to reinforce safety messaging for MES serving crews. The life expectancy of liferafts from VIKING is 15-20 years. While IMO regulations envisage the average weight of persons abandoning ship as 82.5 kgs, VIKING is working on solutions based on scaling up equipment, seating and emergency kit contents to accommodate higher average weights up to 110 kg.
While cruises are stuck in port for the next few months, the overall maritime mobility satellite market remains resilient, and increased bandwidth demand from shipping vessels offers a need that antenna companies can meet. Cruises seemed to be a key part of the pandemic’s spread around the world. A review by The Washington Post of cruise line statements, government announcements, and media reports found that the coronavirus infected passengers and crew on at least 55 ships, about a fifth of the total global fleet. The Centers for Disease Control in the United States has issued a No Sail Order, which at this point is in effect until July 24, 2020. Yet there are already signs of cruises moving back into operation, as Carnival Cruise Lines has recently announced plans to bring a few cruises back in August. Likely increase in bandwidth demand Report predicts that this year will see a 7% increase in bandwidth demand over 2019 figures NSR analyst Grady said that as cruise ships were sailing during the pandemic, they opened up Wi-Fi networks and removed pay barriers, and this factored into increased bandwidth requirements moving forward. NSR’s “Maritime SATCOM Markets, 8th Edition” report predicts that this year will see a 7% increase in bandwidth demand over 2019 figures, even while in-service units and retail revenues decrease. Many shipping vessels are increasing connectivity for crew welfare programs, and as cruises return, Grady says, the demand for connectivity will increase moving forward. Rising demand from commercial shipping Intellian executives validate that experience, and say the pandemic has cued a “significant” spike in bandwidth demand from the commercial shipping market, particularly for high-quality video streaming, as shipboard operations and crew welfare have increased their around-the-clock data demands. Harrison says access to a secure and dependable communications link is making a real difference keeping ships crew’s minds healthy during extended periods of downtime. Intellian CEO Eric Sung says the short-term is difficult, but in the long-term, the need for high-throughput data service for passenger ships will continue to increase, as Netflix and YouTube are becoming part of the de-facto service offering rather than traditional TV broadcasting in guest rooms. Customers’ demands “Customers may not choose a cruise or ferry that doesn’t have a home-grade connection. From the passenger ship business perspective, after lockdown, if they want to get customers back to cruise again, an attractive environment should be prepared to attract customers,” says Sung. “Having high throughput connectivity on-board will be a great marketing tool as well as an essential part of service,” Sung concludes. Effects of the pandemic For the shipping and oil and gas industries, satellite services have been key to monitoring, and engineering In addition, Intellian’s Harrison says that the remote operations situation caused by the pandemic has emphasized the operational and environmental benefits of smart shipping concepts. For the shipping and oil and gas industries, satellite services have been key to monitoring, and engineering and predictive maintenance of offshore assets has been ramped up. Adoption of VSAT connectivity NSR’s report says vessels are adopting Very Small Aperture Terminal (VSAT) connectivity and higher bandwidth provisioning rates. Retail revenues yield a cumulative $34.5 billion with broadband connectivity accounting for over 80%, capacity demand grows 24%, and the addressable market will expand to over 500,000 vessels by 2029. However, one challenge the maritime market will face this year is social distancing restrictions to onboard anything like satellite hardware on new vessels, Grady says. Shipping vessels, for example, may be restricted in terms of coming into port, or who can board.
Liferaft servicing is a necessity, not an option, but the currents shifting society from product to service-based are being felt even in this unexpected area. Back in 2016, a Danish politician caused a surprising stir by predicting in a World Economic Forum blog that - by 2030 - “I don’t own anything. I don’t own a car. I don’t own a house. I don’t own any appliances or any clothes.” Life-saving equipment quality Hi-jacked by conspiracists to portray the WEF as aligned with a theory that the UN ‘Agenda 21’ envisages a world order of totalitarian states hiring out consumer goods, the politician was moved to recalibrate the “all products will become services” prediction as a ‘starting point’ for discussion. Ownership still confers control - especially over hidden expenses - but it also brings obligations It is certainly a discussion worth having in a society already entirely comfortable with the continuous consumer goods upgrade, and where rental bikes and scooters are picked up and dropped off all over many major cities and music, movies and series consumed on platforms such as Spotify, Netflix and HBO. Ownership still confers control - especially over hidden expenses - but it also brings obligations. Used in life or death situations, life-saving equipment quality is of paramount importance, although the fact that products are designed, made and serviced to strict standards mean that compliant products from different suppliers will have much in common. However, key attributes remain a matter for preference. The value of exchange Dorte Hansen, Vice President Sales Regions, VIKING Life-Saving Equipment, says that liferafts have proved to be one high-quality VIKING product where customers increasingly choose rental over ownership. "In the past, owners very much viewed their liferafts as assets to be owned but, today, a large part of the liferafts we supply are subscription-based. This allows the owner to exchange liferafts when they need to ensure full compliance. Rather than having to unload the liferafts, get them to the service station and wait for service and redelivery, it’s a one step exchange," Dorte Hansen - Vice President Sales Regions. VIKING liferaft exchange VIKING has long offered liferaft exchange and the approach has become popular in the passenger VIKING has long offered liferaft exchange and the approach has become popular in the passenger and offshore sectors, and especially in the maritime cargo segment, says Dorte. “Sometimes, a client will have an exchange arrangement to deal with issues at a particular port but, increasingly, owners see liferaft exchange taking less time in most if not all ports. “The advantage has been reinforced over recent months, with port congestion such an issue during COVID-19.” But the shift to liferaft exchange is part of a broader pattern of change in servicing requirements for this most essential of life-saving appliances, with flexibility set as the number one priority for VIKING’s planning and service teams. Welcome to the matrix VIKING Agreements Team Lead Luise Dohn Holm describes a ‘matrix’ of options through which different customer liferaft service preferences are served. The matrix includes the exchange approach, but also fixed price VIKING Shipowner Agreements covering life saving equipment, whose purpose is to take the hassle out of safety equipment upkeep and deliver compliance as a service. The agreements allows the client to choose from a number of fixed price options, deploy either rented or owned liferafts, and select the liferaft exchange option for instant turnaround. Increasingly in the service mix are the digital technologies that support greater remote oversight of assets "The shipowner agreements have been very successful with customers, offering the type of transparency they seek to avoid hidden costs in their servicing arrangements," Luise Dohn Holm - Team Lead, VIKING Agreements Increasingly in the service mix are the digital technologies that support greater remote oversight of assets and ensure that the right equipment is in place at all times to uphold safety requirements, says Luise. For example, a digital portal in set up for onboarded clients to check on the compliance status of their equipment at all times and establish whether equipment coming up for recertification is booked in via VIKING’s central planning system. The extended service economy Another variable she identifies as increasing in significance has been growing owner preference for 30-month service intervals for liferaft, in line with class certification, which is acceptable to an increasing number of IMO flag states. VIKING supplies and services liferafts on both standard 12-month (S12) and extended 30-month (S30) service interval liferafts in all types and sizes. First formalised by IMO in 2009, the 30-month service provision remains a guideline for approval by individual administrations, with liferafts certified on an extended basis after they have been serviced at an approved servicing station. Real-time verification Dorte says the 30-month regime makes planning ahead simpler for the supplier, its service stations Initially, it is limited to the first 10 years of a liferaft’s time in service, although this may be extended if real-time verification justifies acceptance by the Administration. While some administrations continue with the previous regime, where the service interval is 12 months but extensions can be applied for, Dorte says the 30-month regime makes planning ahead simpler for the supplier, its service stations and the owner. The initial appetite for change came from the cruise and ferry sectors, she says, but all customer types are now making S30 liferafts part of their thinking. Liferaft’s sealed aluminium bag “Getting liferafts off offshore rigs is a cumbersome business, for example, so if the service interval can be increased to 30 months, it’s a maintenance gain,” says Dorte. Some clients prefer to maintain a mix of S30 and S12 units, and this is also fully accommodated within VIKING’s servicing regime. Upholding the 30-month service interval requires a supplementary annual liferaft inspection by certified crew members, she acknowledges. However, VIKING has also built simplicity into the check for CO2 and humidity within the liferaft’s sealed aluminium bag. A power-free, magnetic testing tool is inserted in the liferaft container’s transparent panel, which shows green - for compliant - or red. “Where delivering safety and continuous compliance as a service is concerned, every effort should be made to ensure that the user is encouraged towards greater vigilance and more frequent checking of liferaft readiness for action,” says Dorte.
Battery power and a clean environmental conscience go hand in hand, but the performance, availability and lower maintenance costs of E GES free-fall lifeboats are making a new and powerful safety case for all-electric propulsion. Part of a rig upgrade for the Equinor platform Njord A operating in the Norwegian North Sea initiated in 2017, three new 70-person VIKING Norsafe free-fall lifeboats have been an eye-opener for those seeking to extend the life of assets. Norsok R-002 performance standards The solution also meets the most recent risk-based DNV GL-ST E406 and Norsok R-002 performance standards The advanced boats are launched from a unique davit system that fits within the same space and weighs less than an obsolete predecessor that could launch only two. The solution also meets the most recent risk-based DNV GL-ST E406 and Norsok R-002 performance standards. “We were given a boundary box with just 19m of deck width and weight limits of 89 tons, based on platform stability,” says Joe Dawes, Senior Sales Manager for lifeboats and davits. "Kilo for kilo handled, we have delivered the lowest weight davit station ever made," Joe Dawes - Senior Sales Manager, Boats & Davits. Opportunity to shift to all-electric propulsion After VIKING Safety Academy undertook a ‘world record’ 30% overload test for a free-fall lifeboat from a height of 66.8m, installation on Njord A was completed in Spring 2020. In the diesel incarnation envisaged at the project’s outset, the ‘GES 52’ boat is already what Erik Mostert, R&D Manager, describes as a “marvelous innovation”, developed with Equinor to raise the bar on safety. By August 2018, Equinor had decided that Njord A’s new boats would also take the opportunity to shift to all-electric propulsion. VIKING Norsafe E-GES 52 “What became the VIKING Norsafe E-GES 52 wasn’t something that could be decided overnight,” Mostert explains. “It needed a Client Technology Qualification, supported by DNV GL, and a full investigation of the viability of 100% electrical power as a replacement, including 36 months to achieve SOLAS Novel Design Resolution A.520(13).” Marinised technology Mostert places particular emphasis on the safety case for the battery technology selected The resulting solution for each boat comprises of three 25kWh batteries - contained in robust, waterproof cases with their own fire monitoring extinguishing systems - providing power for an electric motor complete with its own gearbox and ventilation system. Given the duties E-GES 52 boats undertake, Mostert places particular emphasis on the safety case for the battery technology selected. "This is marinised battery technology that uses individual cells, in individually sealed and cooled metal cases operating inside a controlled environment: we have at least a triple barrier against any thermal incident. Other maritime stakeholders can draw safety lessons from the approach," Erik Mostert - R&D Manager, Boats & Davits. Smart and digital lifeboats The E-GES is equivalent in many aspects of operational performance to its diesel counterpart but, while many will focus on the ‘green’ dividends of electric propulsion, Georgios Nikoltsis, Manager Technical Department, VIKING emphasises several areas of superiority. “Significant long-term cost savings are achieved through reduced maintenance, and remote monitoring capabilities are also incredibly valuable for offshore operators,” he says. “The smart monitoring capability needed for reporting purposes is integrated in electric systems ‘as standard’, while they do not need anything like as much routine maintenance as conventional engines in the first place." Speaking about smart, digital technology, each of the boats on Njord A has its own email address: its self-diagnostics PLC system alerts shore-based maintenance teams of trend deviations on temperatures, charge or other variables, so that any anomalies can be corrected remotely, or as part of a routine or exceptional visit. Condition-based monitoring Dawes says cost savings could follow if all-electric freefall lifeboats were inspected every 30 months “Across the industry, there is also a move to reduce manning on platforms and, today, some are non-permanently manned,” adds Dawes. “That means you may not actually be able to fulfil SOLAS requirements to start the engines periodically as a safety precaution: with the E-GES you can perform all of the checks remotely from land to assure the availability of the boat.” Equinor has already predicted massive maintenance cost savings, suggesting that an all-electric lifeboat could expect to consume less than 5% of the physical maintenance hours needed for a diesel boat over a five-year period. While this estimate is based on projected, rather than actual figures, Dawes says cost savings could follow if all-electric freefall lifeboats were inspected every 30 months, compared to annual inspections needed by diesel boats. Faster to safety There are other benefits, which have a more direct impact of safety. “From the safety perspective, the launch phase of an evacuation can be executed at a higher sprint speed, so that evacuees can be moved more quickly away from the platform in an emergency,” says Dawes. “Other advantages include better onboard comfort due to the absence of the exhaust fumes, heat, noise and vibration.” In mid-2020, the E-GES concept was qualified by an Australian operator for use in higher temperatures Where offshore asset performance and safety is concerned, it is often observed that where Norway leads others eventually follow. It can be no coincidence that, after knowledge sharing involving DNV GL and Equinor, in mid-2020 the E-GES concept was qualified by an Australian operator for use in higher temperatures. “We’re definitely looking to the export market now, especially after the initial feedback from Njord A,” says Dawes. “Like everything else, COVID-19 has had a massive impact on projects but, when the restart comes, we can pick up on conversations that ranged from project-specific applications to the potential for universal adoption.” First mover and innovator in all-electric survival and rescue craft According to R&D Manager Erik Mostert, the VIKING Norsafe E-GES is far from the only electrically powered evacuation solution put to market by VIKING these years. “Electric propulsion is no longer a technology for the future – it is here now – and here to stay! For VIKING, the journey with electric propulsion and smart, digitalised technology in evacuation solutions and survival craft started a decade ago with the award-winning LifeCraft alternative survival craft and evacuation system that is bound to revolutionise evacuation off cruise ships and ferries.” “The next lines of all-electric evacuation solutions following in the footsteps of the VIKING Norsafe E-GES are racking up at the time of writing. For instance, electric powered conventional lifeboats (E-JYN) are included in planning for new projects and fast, high performance electrified craft (E-FRC) are considered for the defence and professional industry.”
Expert commentary
Seafaring is often deemed a ‘risky occupation’ when it comes to both physical and mental health, involving highly demanding work alongside long working hours, often poor social support, and extended periods at sea. In the Sailors Society’s recent 2022 Cadet Report, they found 57% of Generation Z, those born between 1996-2010, cadets from around the world had submitted scores suggesting anxiety, and that most believed loneliness would be the main cause of any mental health issues they faced. 79.5% also said their choice of shipping company would depend on how it treats seafarers. Seafarer well-being The need for improved seafarer well-being has led to the UK government’s allocation of £2.4 million for projects supporting seafarers’ mental health, maritime skills, diversity, and careers. This investment has been made following the Maritime 2050 report, which highlights that the high incidence of mental health conditions is primarily due to the pressures, nature, and isolation of working at sea and suggests changing technology be utilised to improve sea connectivity. Is LEO services the solution? Satellites have been imperative for both operational and welfare services, in addition to positioning and navigation Satellites have enabled communications at sea for over 50 years. They have been imperative for both operational and welfare services, in addition to positioning and navigation. Generally, communications for major maritime platforms have been provided by Geosynchronous Orbit (GEO) satellites, delivering a “broadband” style service from a few Kbps to multiple Mbps. However, Low Earth Orbit (LEO) satellites are not a new proposition. Early LEO satellites, such as the Soviet Sputnik 1 launched in 1957, provided low single-digit Kbps, while more recent Iridium NEXT satellites provide hundreds of Kbps of resilient service. New services Thanks to significant investments in ‘broadband’ high throughput LEO satellites, new services offering ‘fibre-like’ high-speed low-latency connectivity of about 100 Mbps have become available. These services enable high throughput at a reasonable cost and, if configured as part of a hybrid solution, allow for operational and welfare services to be separated. This protects welfare services for seafarers, offering more access to services like messaging and video communications, streaming platforms, and gaming. The importance of on-board connectivity The surge in demand for LEO connectivity reflects growing expectations from seafarers, and better awareness from employers, around social well-being. With long periods of separation from families and friends and work that often involves high-risk situations, seafaring can lead to a combination of anxiety, stress, and isolation. A lack of access to mental health support services can contribute to depression and increases seafarers’ risk of unhealthy coping strategies resulting in serious personnel issues and retention difficulties. Addressing communication issue The survey highlighted that 63% would consider moving to another shipping company that offered better connectivity The seafarers’ trade union, Nautilus International, further demonstrated the importance of connectivity in 2017 when it published a survey showing that 80% of its members considered communications the second most important integral collective bargaining issue. It also highlighted that almost two-thirds (63%) would consider moving to another shipping company that offered better connectivity. Need for LEO services These demands have since been exacerbated. The COVID-19 pandemic saw many seafarers facing longer periods of isolation due to imposed restrictions and extended contracts, made worse for those unable to call or message their loved ones. Generation Z crews have also grown up accustomed to having instant access to connectivity and can be reluctant to accept a job that takes this away. Together, these forces have pushed the need for LEO services to the forefront of maritime considerations, as a viable solution that meets welfare and operational needs. The benefits of LEO services LEO services offer high throughput connectivity combined with low latency, allowing crew members to access Wi-Fi and download speeds similar to those provided by home broadband. This, in turn, provides numerous benefits for physical and mental well-being: Real-time communication: Personnel can stay in touch with their loved ones and support networks while at sea, helping to reduce feelings of isolation and loneliness. Mental health support: Improved access to support services allows crew members to connect with mental health professionals and receive support for conditions like depression, anxiety, and PTS. Enhanced safety: Better connectivity allows for real-time tracking and the monitoring of location, weather data, and emergency response services, which can help prevent accidents and ensure quick response times in the event of an emergency. Remote monitoring of seafarers' health and well-being through wearable technology can also be used to monitor vital signs and detect early indications of health issues. Training: LEO services provide potential for crews to engage in virtual training, which is especially useful in cases where members are at sea for extended periods. On-demand access to training resources allows crew members to develop their skills and knowledge at sea, encouraging career advancement. Virtual training also helps establish best practices that promote onboard safety. Overcome risks with a hybrid strategy The combination of LEO and VSAT services allows large quantities of data to be exchanged at broadband speeds Relying solely on LEO satellites is a risky strategy, putting operational priorities in conflict with crew welfare, as using data for one negatively impacts the data available to the other. To avoid this, LEO services can be paired with a guaranteed VSAT solution offering a committed information rate (CIR), to ensure mission-critical operations are not compromised and to protect the high-throughput connectivity most suited to provide well-being support services. The combination of LEO and VSAT services allows large quantities of data to be exchanged at broadband speeds, and enables real-time communications and remote monitoring for operational matters, all without affecting crew services. The key to choosing the right hybrid solution A vessel and the needs of its crew members must be considered before choosing a service. For instance, maritime operators need to consider whether they require a solution with built-in access to ports, as some network operators don’t manage regulatory access. Using such a solution in ports without pre-approval can lead to significant consequences. They also need to think about the operational conditions, ensuring their equipment has been built to withstand the environments it will be used in. Additionally, a CIR is crucial for most professional-grade operations, ensuring connectivity for operational and welfare purposes is never compromised. Resilience, support, and assurance Emerging LEO constellations provide new options for maritime operators that enable operational efficiencies When delivered with the right resilience, support, and assurance and fused with a network service that guarantees connectivity emerging LEO constellations provide new options for maritime operators that enable operational efficiencies, increased safety, and security, greatly improved on-board morale, and support longer-term retention. This means they can invest in both their crew and long-term planning. Safety and career advancement Officers and crew will be able to see that they are working for an employer that cares about their welfare. Contact with home will only be restricted when operational tasks dictate, rather than because the vessel doesn’t have the bandwidth. Seafarers will also have the ability to catch up on entertainment, access social media, video and voice calling, and remote training that promotes safety and career advancement.
Health and safety are key considerations for all maritime organisations, in particular, for those operating in remote locations or where extreme weather conditions may put workforces at greater risk. With COVID-19 here to stay for the foreseeable future, it is vital that shipping organisations consider both the short and long term safeguarding measures, which are required to protect their workers at sea. COVID-19 management plans Establishing safe working conditions and providing onboard expert medical care has always been of paramount importance but, now, effective COVID-19 management plans have also become essential in creating safe working environments and, importantly, in keeping them operational when personnel contract COVID-19. In these circumstances, controlling the spread of infection remains mission critical and for companies, like RMI In these circumstances, controlling the spread of infection remains mission critical and for companies, like Remote Medical International (RMI), which provides health and medical support to teams, operating in remote or hard to reach locations, the need for COVID testing services has resulted in rapid scale up and business diversification. Early on during the COVID-19 pandemic, the world learned that many symptoms presented by an individual had the potential to be a positive case. This knowledge was used to respond to clients’ needs, in order to get employees back to work safely, as quickly as possible. COVID pre-mobilisation testing The sharp rise in demand for testing has resulted in an upscale of COVID pre-mobilisation testing at ports and harbours, for teams heading offshore, on-site COVID-19 audits, and virtual consultancy for remote teams. This shift in demand means that over 25% of the business is now COVID-19 related. Over two years, RMI’s medical experts have helped various shipping organisations on screening programmes that are tailored to their current needs. Their global presence and team of over 200 highly qualified medics, means they are well set to provide assistance services 24/7, with telemedicine support, case management and security services, adding to a one-stop-shop for all global medical and risk management requirements. One of the key concerns of shipping organisations has been how to manage a potential outbreak of COVID-19 offshore, and RMI has seen a variety of new demands imposed on personnel, who await embarkment at UK ports, for activities in the North Sea. In 2020, RMI began to work closely with a leading independent oil and gas company, to mitigate the spread of COVID-19 offshore. Ad-hoc testing for personnel embarking and travelling offshore Initially, RMI issued ad-hoc testing to personnel, who were due to embark and travel offshore Initially, RMI issued ad-hoc testing to personnel, who were due to embark and travel offshore. Crews were ranked by risk and then tested as a matter of priority: personnel would stay in a local hotel, awaiting the results of their test and if negative, would soon travel offshore. However, very quickly, the need for ad-hoc testing progressed into the requirement for regular daily testing, not made any easier by the complications of sending thousands of staff offshore weekly during a pandemic. RMI medics and shipping staff combine The hotel facilities were, therefore, expanded and in total, over 18,695 personnel were tested. RMI’s medics, already highly trained and qualified, had to adapt quickly to the novel protocols required, when providing a rapid point of care PCR test, delivering 80 to 90 tests a day within an eight-hour window meant that there was no room for error. In this way, the collaboration of RMI’s medics with shipping staff under increasingly challenging conditions ultimately protected lives and ensured smooth running of shipping operations. Rise in demand for COVID-19 risk audits As the COVID-19 pandemic progresses and with undoubtedly more variants to come, there is an increase in demand for COVID-19 risk audits, which can really help shipping companies to ensure their operations, stay on track. For example, RMI conducted a robust risk assessment on the impact of COVID-19 on employees living at sea and working offshore in Equatorial Guinea. COVID-19 has made it very challenging to find good medical staff for work – the demand has been far higher than the supply at times, during the past year. RMI sets a very high bar and is committed to only employing the very best, as they have a reputation to protect, as well as the lives of the people that their medics are there to support. This role particularly suits ex-combat medics, who are looking to use their skills in a different setting and in this case, RMI selected and sent out only the very best to Equatorial Guinea. Their experienced medical auditor, who had just returned from working in Afghanistan, was deployed to document the potential risks at the airport, during their 10-day quarantine in-country, and throughout their assignment offshore. RMI’s audits designed to cover all bases Remote Medical International’s audits are designed to ensure that all bases are covered Remote Medical International’s audits are designed to ensure that all bases are covered. For this project, each location was broken down by levels of risk and included recommendations on how to prevent a possible COVID-19 infection. Each assessment included the level of probability for infection, as well as how to best prevent it, such as always wearing a mask, or limiting access to certain communal areas. Following the audit, our recommendations consisted of overarching actions that would ultimately prioritise the health and safety of the offshore employees. This included the implementation of a COVID-19 surveillance testing program for facility workers at the quarantine site, establishing a more structured COVID-19 testing programme, creating a training programme to support service staff, and the safest ways to provide services to employees onboard. RMI delivers critical support in vital and diverse ways It really is the case that no matter how remote the location or vessel, RMI can deliver critical support in vital and diverse ways. One of their recent operations has seen them provide emergency medical advice to US government owned and operated ships and units, located throughout the world, via the company’s topside assistance service, meaning that no crew is ever alone. The medical providers onboard could contact the Global Coordination Centre, at any time and be connected to a physician for medical advice within mere minutes. This type of remote support is what can enable crucial operations to continue all year round, despite the COVID-19 pandemic and RMI hopes to support many more, as they navigate these turbulent times.
The cruise industry has received a vital lifeline in its bid to safely set sail once again. Several pioneering Finnish businesses and organisations have developed new, innovative safety approaches for the sector to adopt, in response to new post-pandemic measures. These new initiatives and research projects are set to bring the industry back from the brink and ensure a safer and successful cruise experience for all. Undertaking health and safety measures Expectations surrounding cruises today have changed beyond all recognition in the wake of the COVID-19 pandemic. Whilst the safety and wellbeing of passengers and staff has always been a top priority for the industry, its recovery depends on taking health and safety measures to a new level, to drive stability and sustainability in the challenging years ahead. Since the onset of the COVID pandemic, Finnish research organisations and companies have led the charge in responding to the industry’s call for new solutions to support its resurgence. With viable options showing what is possible, the future of the industry looks bright and secure. Healthy Travel project Researchers collaborated with cruise companies to find ways of improving health and safety on cruise ships The Healthy Travel project[i] is one such initiative: researchers collaborated with cruise companies, shipyards, and subcontractors to find ways of improving health and safety on cruise ships and in terminal buildings. Researchers in cell biology and industrial management created models to analyse passenger flows on vessels of different sizes and developed processes and procedures to minimize infection risks. To further understand the role of breathing, coughing, and sneezing in spreading COVID-19, researchers from Tampere University, VTT Technology Research Centre of Finland, and the Finnish Institute for Health and Welfare created a robot head [ii] prototype as part of the AIRCO research project. Air purification techniques The initial aim of the robot was to support the design and planning of all kinds of indoor spaces, including ships and terminals, and to measure the effectiveness of masks, ventilation, and air filtration and purification solutions in preventing the spread of viruses. Ensuring indoor air quality (IAQ) is also a crucial factor for minimising infections among passengers and crew. To support the need for better air purification techniques, interior accommodation provider ALMACO partnered with Genano [iii] to provide the marine and offshore industry with advanced air decontamination technology that removes airborne impurities of all sizes, including microbes and the novel coronavirus. Developing solutions for material flow on ships KONE researched with several cruise line companies to develop solutions for people and material flows on ships In addition to air quality, the flow of people and material can have a huge impact on the transmission of airborne viruses. KONE [iv], a global pioneer for marine elevators and escalators, conducted intensive research in partnership with several cruise line companies to develop new solutions for people and material flows on ships while improving health and safety on board and in the terminals. This involved collecting data with sensors installed on ships, timing activities, and conducting interviews with passengers and crew members. In the same vein, an IoT platform from Hypercell[v] uses Bluetooth signal sensors to collect data on people volumes, dwell times, and flows in indoor and outdoor locations. Innovation is key Innovative approaches are the way forward for the industry to get back on its feet, but with so much at stake, these next steps are crucial to get right. Accurate data, insight, and new techniques will play a key role in moving forward, as Timo Pakarinen, managing director for KONE’s marine business explains, “Any changes on cruise ships must be fact-based and commercially viable solutions because the investments required are so large.” Supporting cruise industry recovery “Collaborative research projects such as these, which have been initiated and funded by Business Finland, will continue to produce innovations and technologies to support the recovery and future viability of the cruise industry for many years to come.” “Finland now offers leading technologies and solutions focusing on indoor air quality, passenger flows, safety protocols, and touchless solutions. The insights gained from this vital research are also contributing to the design of new cruise ships,” says Ulla Lainio, Head of Marine & Ports Global Industry Team at Business Finland.
Harbour insights
Even in the waning days of the COVID pandemic, infectious diseases aboard cruise ships continue to be a cause for concern. Aggravating the challenge is a combination of crowded conditions, vulnerable (i.e., older) passengers, and the need for a fast turnaround once a ship is docked (thus providing limited time for sanitation protocols). While passengers tend to originate from affluent countries, where infection rates are low and vaccinations are common, crew members may come from developing companies where higher rates of infection are common and vaccinations are not. Disease exposure and transmission Disease exposure and transmission are worsened by the dense population and closed-in environment of cruise ships, and by shared activities among international passengers and crew. A specific risk is that a person may catch an infectious disease during a cruise voyage and then spread it to a vulnerable community upon their return (e.g., nursing homes). At the risk of infection are the 9 million or so passengers who board cruise ships from North American ports, about half of which embark from a Florida port. Healthcare quality Although there are some accepted guidelines and best practices, how they are implemented can vary In its post-pandemic revival, the cruise industry is seeing higher capacity; the average cruise ship carries 3,000 passengers and 1,500 crew members. The quality of healthcare on cruise ships varies widely, and there are no international regulations that ensure high-quality care. Although there are some accepted guidelines and best practices, how they are implemented can vary from one cruise line to the next. Compliance standards and guidelines The Cruise Line International Association (CLIA) sets compliance standards among its member cruise lines, urging members to follow the “Health Care Guidelines for Cruise Ship Medical Facilities” developed by the American College of Emergency Physicians (ACEP) Section on Cruise Ship and Maritime Medicine. The guidelines address issues such as medical facility design, staff qualifications, diagnostic equipment, and availability of medicines. The guidelines address emergency care, not primary care or preventative services for crew members. Sanitation requirements International Health Regulations address sanitation requirements. In the United States, the U.S. Coast Guard enforces maritime safety requirements, and the U.S. Centers for Disease Control and Prevention (CDC) regulate sanitation and public health on cruise ships. The Public Health Service Act authorises the U.S. Public Health Service to take action to prevent introducing, transmitting or spreading communicable diseases into the United States from a foreign country. Vessel Sanitation Program CDC requires carriers to report death and certain illnesses in arriving passengers and crew As the lead agency relating to communicable disease control at international ports of entry, the CDC requires carriers to report death and certain illnesses in arriving passengers and crew. The CDC established the Vessel Sanitation Program in 1976, surveilling gastrointestinal illnesses and investigating outbreaks on cruise ships. They also handle sanitation inspections in partnership with the cruise lines. Track and prevent communicable diseases Historically, efforts to track communicable diseases in cruise ship environments have yielded early warnings of illness clusters that might otherwise have gone unnoticed. Examples include influenza, measles, rubella, varicella, meningococcal meningitis, hepatitis A, Legionnaire’s Disease, and respiratory and gastrointestinal illnesses. Although most authority regarding the regulation of international travel rests with the federal government, states can also help by providing recommendations and guidelines to improve communication and collaboration with the CDC and the cruise ship industry to strengthen prevention programmes.
Liquid natural gas (LNG) can avoid concerns about global warming in the maritime industry – to a point. LNG is a carbon-based fuel but yields lower emissions than current fuels used in the maritime industry, thus enabling compliance with International Maritime Organization (IMO) goals to address greenhouse gas emissions. LNG offers an attractive transition route until even more environmentally friendly approaches become practical, although costs to transition existing vessels to LNG are cost-prohibitive. LNG is gaining more favour among dual-fuel new building contracts, using either LNG or conventional liquid marine fuels. Pre-liquefaction process When natural gas is cooled to minus 162 degrees C (minus 259 degrees F), it turns it into a liquid. Liquefaction reduces the volume to 1/600 of that of gas. Emissions from LNG are drastically lower than those of traditional heavy fuel oil. LNG removes sulphur in the pre-liquefaction process, so it emits almost no sulphur oxides (SOx) or particulate matter (PM) when burned, and it emits 90% less nitrogen oxide (NOx), and about a fourth less carbon dioxide (CO2). Emissions from LNG are drastically lower than those of traditional heavy fuel oil LNG is also relatively safe because its specific gravity is lighter than air, it is easy to diffuse, and there is less risk of explosion. One concern for transitioning to LNG is bunkering, in effect, the need for more supply infrastructure at port facilities to serve LNG-powered ships. Currently, the bunkering infrastructure can deliver LNG to 96 ports, with an additional 55 ports in the process of transitioning. There has also been an increase in ship-to-ship bunkering. Reducing CO2 emissions Although transitioning older ships to LNG is expensive, so are the alternatives, such as scrubbers and very low sulphur fuel oil (VLSFO). Because VLSFO does not affect CO2 emissions, the fuel is inadequate to achieve the IMO goal of reducing CO2 emissions by more than 40% in 2030 compared to 2008. The Poseidon Principles are a framework for integrating climate consideration into lending decisions to promote decarbonisation. The framework is prompting some lenders to favour financing of LNG-powered vessels over those using traditional fuel oil. Transitioning to LNG can help fill the gap until new decarbonisation technologies come online and become more practical, including hydrogen, ammonia, rotor sail/batteries and methanol. Deep-sea shipping LNG is the only alternative to traditional marine fuel oils that is commercially variable for deep-sea shipping Since the first LNG-fuelled vessel came into service in 2000, the number of vessels using LNG has grown 20% to 40% per year. In 2020, there were 175 LNG-fuelled ships in operation, and another 200 on order. These numbers are in addition to the 600 or so LNG carriers, which use boil-off gas in their propulsion systems. By investing in LNG-fuelled vessels now, ship owners can realise immediate greenhouse gas (GHG) benefits – up to 28% on a tank-to-wake basis, including the impact of methane emissions, says SEA-LNG, a multi-sector industry coalition seeking to accelerate the adoption of liquefied natural gas. LNG is the only alternative to traditional marine fuel oils that is commercially variable for deep-sea shipping, says SEA-LNG. Worldwide gas consumption LNG is a widely available global commodity with 21 countries exporting to 42 importers and accounting for approximately 11% of worldwide gas consumption. Currently, LNG is a tight market, as strong power and gas demand in Asia has pulled LNG away from Europe. Combining to tighten the market is a 2021 post-COVID economic recovery and a cold winter in 2021. LNG buyers seeking to avoid shortages in the winter of 2022 triggered a price rally. Drought in South America has further limited hydroelectric output and pulled volume from the Atlantic’s LNG supply. Also, several LNG facilities experienced outages that decreased supply.
Backlogged ports, a shortage of shipping containers and not enough workers are among the factors contributing to supply chain disruptions that have led to shortages of various goods and are likely to impact availability of merchandise, during the upcoming holiday season. Demand is growing rapidly as the impacts of the COVID-19 global pandemic have diminished. However, lingering consequences of the pandemic are continuing to impact the container shipping market. With each element in the system tightly intertwined, any changes tend to ripple with additional repercussions. Slow circulatory movement of containers A direct upshot of the COVID-19 pandemic was to slow the circulatory movement of containers globally. To increase productivity and save time, some vessels began making their return journeys empty, in effect leaving more empty containers at the delivery destination and fewer at the source of shipments. The varied timing of the pandemic in Asia and the West compounded the problem At one point, Asian containers could not be sent back to Asia, because of COVID-19 restrictions in place. The varied timing of the pandemic in Asia and the West compounded the problem. With empty containers stacking up in the West and a shortage in the East, slower circulation of containers and higher demand have led to sharp increases in costs. Millions of TEU dry container units added A lack of new equipment is not the problem. Last year, the industry added about 2.8 million twenty-foot equivalent (TEU) units of dry containers, in line with the 10-year average. Congestion at ports has been going on for months and still continues. Recently, in the San Pedro Bay region, near the Port of Long Beach, in California, there were 144 ships, including 85 ships that were waiting to unload. In Savannah, Georgia, more than 20 container ships were waiting to dock. Ports in the US states of New Jersey, New York and Texas have also seen record backlogs. Majority of influential global ports face backlogs According to one report, 77% of the most influential ports in the world reported above-average wait times this year. The turn-around time for a container in ports has nearly doubled in 2021, in comparison to 2019. A worker shortage at the ports is aggravating the problem and container ships now carry about 30% more goods, which require more labour to unload. Ports are also doing the additional work with fewer people. There is also reduced labour productivity at warehouses and marine terminals. Investment in workforce training to counter bottlenecks Some port bosses expect the bottlenecks to last through the summer of 2022. To address the problem, some ports are investing in workforce training and scheduling night-time appointments to pick up goods. Although a lot of attention is focused on the ports, they are just one element in the troubled supply chain. Even if the ports could increase their capacity, downstream processes would also have to increase their labour force, to accommodate the higher volume. Difficult to absorb impact of global supply chain disruptions In the best of times, the global supply chain operates like a well-oiled machine In the best of times, the global supply chain operates like a well-oiled machine, despite its complexity and the inter-relatedness of various stakeholders. However, the sheer size of the system makes it difficult to absorb the impact of any disruptions. Turning the system around takes time, and a burgeoning global demand for goods, in the aftermath of a global pandemic, makes recovery even more difficult. The Biden Administration in the U.S. has established a Supply Chain Disruptions Task Force, to monitor and address short-term supply issues. This task force is convening meetings of stakeholders in industries with urgent supply-chain problems, such as construction and semiconductors, to identify the immediate bottlenecks, as well as potential solutions. Role of global supply chain more critical now There have been supply chain disruption and staff shortages in several countries, including the United Kingdom (UK), Germany and New Zealand, according to business surveys. As the economy recovered and demand increased, businesses have not yet been able to bring inventories fully back to pre-pandemic levels, causing inventory-to-sales ratios to fall. The role of the global supply chain has never been more critical.
Case studies
Ocean transport of Sian Flower’s produce helped the company overcome the pandemic-induced volatility in air freight rates while helping it achieve its sustainability goals. Sian Flowers is a Kenyan producer of high-quality roses and summer flowers, exporting their blooms to Europe, the United States, the UAE, and Australia. The company has won regional and international recognition for pursuing rigorous sustainable practices, including limiting the use of pesticides and the conservation and treatment of water. In addition, Sian is Fair Trade Certified, paying great attention to the welfare of workers and the community. Environmentally sustainable practices When the COVID-19 pandemic hit, Sian Flowers’ supply chains, especially to Europe, were impacted, as it was for other players in the industry. Fewer flights were operating to western markets, and space on board was limited, making it difficult to secure space for Sian’s entire cargo, which resulted in wastage of produce. Air freight rates had also become prohibitively expensive, which had an impact on margins. Air freight rates had also become prohibitively expensive, which had an impact on margins Everyday challenges were disrupting the seamless movement of their sensitive flowers too – multiple touchpoints between the farm and port jeopardised the vase life of their cut flowers. These issues notwithstanding, Sian was committed to environmentally sustainable practices and believed they needed to find ways to reduce their carbon footprint. Cold chain solution Maersk’s team in Kenya devised an end-to-end cold chain solution that facilitated the easy movement of the cut flowers from Mombasa to Rotterdam by ship instead of plane. These included: A cold room facility in Nairobi. Cold storage of loose cartons in cages. Palletisation, stuffing, and booking services. Trucking from Alpha to Mombasa. Customs brokerage at Mombasa and Rotterdam. Trucking from Rotterdam port to Aalsmeer. Deconsolidation services in the Netherlands (de-stuffing, sorting, and storage). Maersk shipping vessels transport the refrigerated cargo to Rotterdam Operating twice a week from Mombasa, Maersk shipping vessels transport the refrigerated cargo to Rotterdam in Controlled Atmosphere (CA) containers providing Sian with control over gas levels in the container while their flowers are in transit on the ship. Long-term freight rates Captain Peter, Maersk’s proprietary digital visibility assistant, offers Sian remote monitoring of the temperature and humidity levels in the container along the journey, enabling them to act to maintain the CA containers’ conditions intact. One of the most important aspects of the ocean solution and conducive to maintaining the freshness of the flowers on arrival at destination is the reliability of our ocean schedule times, which they guarantee, as well as the offer of long-term freight rates that could lend stability to Sian’s finances in a volatile environment. Captain Peter offers Sian remote monitoring of the temperature and humidity levels in the container Sian’s delicate flowers have been traveling seamlessly and reliably across Kenya, thanks to fewer touchpoints and a single point of contact. All their cargo is allocated space on board Maersk’s Ocean vessels, which has become a viable alternative to air freight. Greenhouse gas emissions The flowers continuously arrive fresh to the Netherlands, where logistics is efficiently coordinated ensuring the flowers reach markets on time and enjoy a good vase life. Sian has also been able to achieve a near-90% reduction in greenhouse gas emissions with ocean transport. “Maersk being the biggest shipping line in the world, one of the biggest logistics companies in the world, had the capability to not only guarantee the delivery of our flowers in good time, they also gave us the capability to monitor, and really keep an eye on the product as it travelled for weeks by sea,” said Christopher Kulei, Director, Sian Flowers Group of Farms.
The military force for the Kingdom of Bahrain has purchased an innovative self-propelled workboat, WorkFloat, to support its growing naval fleet. Once afloat, their 12m x 6m WorkFloat will provide a useful work platform for a range of support tasks in their Naval Port. WorkFloat The WorkFloat’s equipment includes a 10tm crane that can lift just under half a ton at 13m, a deck load capacity of over 10t, a 2t deck winch that can be used for mooring work, a central moon pool for drilling or GI work, full electrics and navigation, bow loading ramps for military vehicles, spud cans for 10m spud legs, a retractable bow thruster and 2 x 70hp Yamaha high thrust outboards that give an impressive 7 knots and 1.2t of bollard pull. It is also built to the MCA workboat code and complies with relevant class standards for lifting and stability. While the spec-sheet of the WorkFloat is not as impressive as a larger multi-cat or workboat, it is its unique ability to fold up (including all equipment) and fit into a standard 40’ shipping container that makes it such an impressive package, with mob or demob taking under a day and benefiting from ease and low cost shipping around the globe. ‘The Spirit of Innovation’ award winner WorkFloat, a Cornish based company, was established in 2019 to develop the concept WorkFloat, a Cornish based company, was established in 2019 to develop the concept, and after winning the main industry award ‘The Spirit of Innovation’, at the European Commercial Marine Awards, at Seawork, they have received a growing interest from organisations, both in the United Kingdom (UK) and abroad. Toby Budd, the Managing Director and Founder of WorkFloat, said ‘’It is a massive milestone for the business to design, build, deliver and then commission this WorkFloat for the BDF. They have been a fantastic client, extremely hospitable to us, while we are here in Bahrain and very understanding of some delays caused by COVID-19. I can see how useful it will be for them and look forward to working with them on other projects in the future.’’ WF1200 modular system WorkFloat is now designing the next evolution of the system. Called WF1200, it is a modular system that continues to utilise the benefits of a space frame structure with plastic floats. It has a higher payload capacity, much bigger crane options, larger engines, can scale to sizes 24m plus and critically can be jacked up out the water. When asked about the future, Toby Budd, Founder and Managing Director at WorkFloat, said “Interest in WorkFloat has been significant since we put the video on social media. We are now costing the new WF1200 system so we can provide quotes to all the enquiries we have had.” ScaffFloat Toby Budd adds, “The new design builds upon what we built for the BDF. It’s really simple and being modular, it moves closer in concept to our other product, ScaffFloat that has become so popular due to its simplicity, low cost and versatility. And, of course, we hope to have something to show at Seawork in just under 100 days.” The ability to ‘jack up’ has been driven by demand from existing geotechnical, civil and diving clients. Being so light and easy to mob, the WF1200 system from WorkFloat will be able to provide the benefits of a jack up barge on inland waterways, under bridges, landlocked lakes and lochs, and other sites traditional larger jack up barges can’t access.
Jay Jay Textiles’ journey towards business expansion with lifestyle logistics solutions is stitched to perfection. Established over 50 years ago, Jay Jay Textiles has a strong presence in India, Sri Lanka and Bangladesh, as a vertically integrated manufacturer of cotton knitwear for children’s apparel and home products. In the past few years, Jay Jay Textiles has branched out to Ethiopia, starting with three factories in the Bole Lemi Industrial Park, located in nation’s capital of Addis Ababa, which caters to reputed brands and retailers based in the United States of America (USA) and the European Union (EU). Jay Jay Textiles were facing several challenges that disrupted their operations and supply chains. There were gaps in communication and several uncoordinated handovers, since they were working with multiple forwarding agents for their imports and exports. Challenges included frequent delays and high costs There were also frequent delays and higher costs, due to cargo rolling in the congested Salalah Port, in Oman There were also frequent delays and higher costs, due to cargo rolling in the congested Salalah Port, in Oman, for two to three weeks on their import leg from Tuticorin, in India. What further added to the existing delays was the cumbersome customs clearance processes. Moreover, at the start of the fertiliser season in Ethiopia, truckers were diverted to transport fertilisers, in order to progress the agricultural industry in the country. During this time, Jay Jay Textiles’ customers struggled to secure truckers to transport their manufactured goods out of Ethiopia to Djibouti, for shipping to the US. Hot Box Connection solution Jay Jay Textiles’ expansion plans and existing challenges required a customised solution that addressed most of their issues. To solve their cargo-rolling challenge out of Tuticorin and Salalah Port, A.P. Moller – Maersk (Maersk) offered the customer their renowned Hot Box Connection solution. This assured equipment availability and vessel space allocation for their raw material imports into Ethiopia. With 70 trucks, Maersk was able to cater to Jay Jay Textiles’ entire inland transport requirement and ensure unhindered movement. Being their single point of contact for coordinating everything behind the scenes, Maersk eliminated the risks of delays that occurred in the past, while working with multiple providers. Maersk’s logistics solution helped in business expansion The logistics solutions made things fall into place for Jay Jay Textiles, helping them achieve their ultimate goal of expanding their operations, while reducing cost inefficiencies. Jay Jay Textiles is now working with 6 US fashion retailers, as opposed to just 3 in 2019 Jay Jay Textiles is now working with 6 US fashion retailers, as opposed to just 3 in 2019. Until the end of last year, they operated out of 5 sheds/factories in the Addis Ababa Industrial Park, in Bole Lemi, Ethiopia. Currently, they have 7 factories to fulfill the growing demand from their buyers in the US. Single logistics provider for inland services Despite the significantly challenging impact of the COVID-19 pandemic on the global apparel and textiles industry, Jay Jay Textiles’ volumes increased by 149% in 2020, in comparison to 2019. Their 2021 half-year volumes are at 69% of 2020, indicating that their growth curve will continue till the end of 2021. Having a single logistics provider for inland services and customs clearance helped Jay Jay Textiles to reduce their operational costs and time. This added visibility within their supply chain and minimised the delays associated with multiple handovers. Working towards a more connected future Currently, the Ethiopia team is working on making consolidation facilities operational in the country. This will help European and North American buyers with their purchase orders from Jay Jay Textiles and other apparel manufacturers in Ethiopia. The endeavour aims at spearheading a connected and simplified end-to-end supply chain solution for apparel manufacturers in Ethiopia.
As supply chain disruptions continue to wreak havoc on global economies, Oosto is helping to ease port security and landside operations, which are burdened with increased security challenges, operational risks, and tightening regulations, through the use of the company’s renowned visual AI-driven access control solution. Facial recognition technology Group 207, a globally renowned leading-edge maritime logistics operator in the Port of Ashdod, Israel, recently implemented Oosto’s facial recognition technology for video surveillance for all of its cargo-handling activities. Oosto’s solution instantly recognised authorised individuals, which led to a substantial amount of manpower saved The company’s cutting-edge, 70,000 square-metre facility, which saw almost immediate results upon implementation of OnAccess for security-screening authentication of cargo and ground-handling personnel. Oosto’s solution instantly recognised authorised individuals, which led to a substantial amount of manpower saved, increased operational transparency, and a rapid return on investment. In fact, Oosto calculated waiting time reductions that totaled 15 to 20 minutes per driver on average. OnAccess access control solution Prior to implementing Oosto’s OnAccess access control solution on their premises, Group 207 was challenged with a manual check-in, credentialing, and identification authorisation process of its cargo handlers, which resulted in long lines, inefficiencies, and frustration among contracted drivers. “Before we implemented Oosto’s facial recognition solution, we had a problem with identification, which required a truck driver to provide his paperwork to a receptionist, who would then work to identify the driver and certify that the paperwork was correct,” said Ofer Margules, the Chief Operating Officer (COO) of Group 207. Oosto – Group 207 partnership Ofer Margules adds, “Now, we don’t need the paperwork, we don’t need the receptionist. The truck driver just goes to a kiosk, the system recognises the driver and he can access the cargo he came for. Today, if you ask any driver at this port, where the most convenient place to get logistics services in terminals is, they will definitely tell you it’s Group 207.” “We are thrilled that Group 207 has chosen to partner with Oosto on this top-priority endeavour,” said Ofer Schmidt, Oosto’s Sales Director for Central Europe and Israel. Real-time facial recognition aids logistics service providers Logistics providers are increasingly exploring new approaches to unlock efficiencies in port operations Ofer Schmidt adds, “This demonstrates the value that real-time facial recognition can offer logistics service providers in today’s capacity-constrained supply chain environment. We can accurately measure the man-hours saved, both on the part of the drivers and in terms of Group 207’s own manpower, and deliver a rapid return on investment.” Logistics providers are increasingly exploring new approaches to unlock efficiencies in port operations, to help combat customs clearance delays and traffic bottlenecks, docking and unloading delays of cargo containers, protect goods from cargo pilferage, and meet security clearances. Efficient, rapid door-to-door cargo Efficient and rapid door-to-door cargo transport is critical, as the volume of goods transported by global container fleets has nearly doubled in recent years and cargo pile ups at ports have reached crisis levels, especially during the global COVID-19 pandemic spread. According to the Organisation for Economic Co-operation and Development (OECD), 90% of the world’s goods are currently shipped by sea, with maritime shipping volumes projected to triple by the year - 2050. Opportunities and challenges for logistics providers This growth brings both opportunities and challenges to logistics providers and transportation companies in the near future, and associated operational burdens on port security measures and procedures to safeguard people, ports and cargo will only intensify the necessity and adoption of biometric technologies as a result.