Alfa Laval Marine Separators (13)
Browse Marine Separators
- Operating pressure
- 1.38
- 1.38 ~ 3.45
- 2 ~ 6
- Make
- Alfa Laval
- Other Alfa Laval products
- Alfa Laval Heat exchangers
- Alfa Laval Boilers
- Alfa Laval Inert gas systems
Separator products updated recently
Separators - Expert commentary
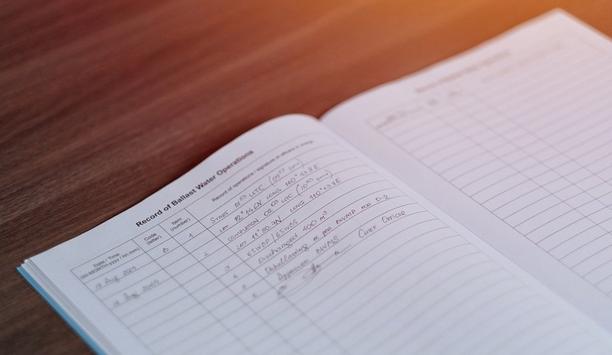
When the Ballast Water Management (BWM) Convention came into force in 2004, it was in response to a crisis we couldn’t afford to ignore—one where invasive aquatic speci...
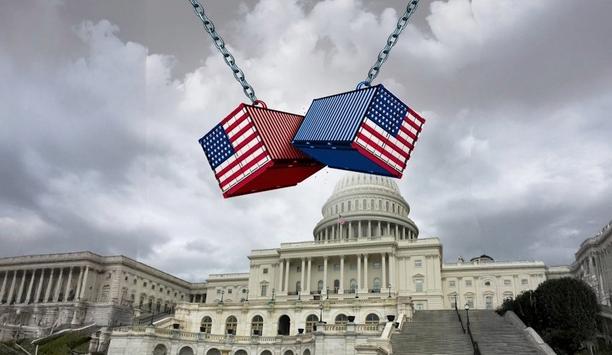
President Donald Trump has already made plenty of headlines since taking up his second term in the White House, including with the announcement of numerous new tariffs on imports....
Latest Alfa Laval Ltd news

Alfa Laval announces that Martijn Bergink has been appointed President of the Marine Division, effective 1 September 2025. This is in addition to his current roles as President of...
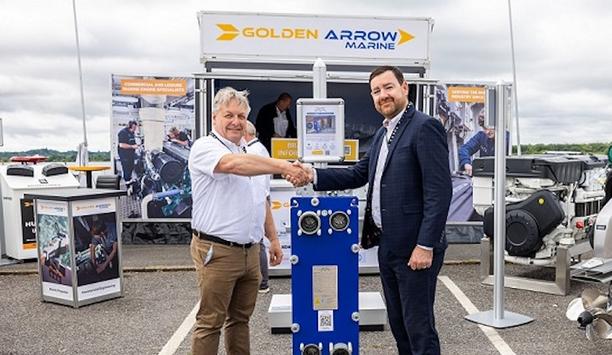
Golden Arrow Marine has been appointed as an official Channel Partner for Alfa Laval, marking a significant step in both companies’ commitment to delivering high-quality, sus...

Alfa Laval, a pioneer in heat transfer & centrifugal separation, is pleased to announce the appointment of ESI Process (UK) Ltd as its new distribution partner for the industri...
Trending topic articles
Watson Farley & Williams ("WFW") advised Pacific Basin Shipping ("Pacific Basin") on a US$250m sustainability-linked seven-year senior secured committed revolving credit facility. The facilit...
Alva Industries (Alva), a manufacturer of frameless motors and owner and creator of FiberPrinting technology, has announced the publication of a series of new white papers on FiberPrinted motors for h...
DNV has awarded a General Approval for Ship Application (GASA) certificate to Mitsui O.S.K. Lines, Ltd., (MOL), MISC Berhad (MISC), PETRONAS CCS Ventures Sdn. Bhd. (PCCSV), and Shanghai Merchant Ship...
ClassNK has released 'ClassNK Technical Journal No.11 2025 (Ⅰ)'. This issue features the title 'Latest Technological Trends for Protection of the Marine Environment', providing the particularly well-r...
RAD Propulsion, a globally renowned innovator in electric marine propulsion systems, announced the expansion of its international dealer network with new strategic partnerships in the Netherlands, Ind...
As maritime companies digitise, decarbonise, and expand across continents, standing out in the market has never been more challenging. Customers expect clarity. Talent is scarce. And lead generation t...
Watson Farley & Williams advised ING Bank N.V., Singapore Branch—acting as arranger, lender and facility and security agent — on a term loan facility provided to Tank Container Investm...
LOOKOUT, the AI pioneer in marine safety, launched enhanced benefits to marine professionals through its preferred dealer and installer programme. The new resources help LOOKOUT dealers and installer...
The new version of KaizenWEG, developed with low-code technologies and artificial intelligence, strengthens participative management and drives a global culture of collaborative innovation. WEG has r...
Multi-party collaboration addresses serious threat to safety of navigation and visibility of high-value assets in degraded and compromised Global Positioning System (GPS) and Global Navigation Satelli...
ClassNK has granted its Innovation Endorsement for Products & Solutions to the maritime cybersecurity support solution, “CYTUR-MCTI” developed by CYTUR and its partner company Rakuten...
Econowind has received a repeat order from Terntank for the installation of eight VentoFoil units on two additional methanol-ready hybrid tankers. Following the initial order in May 2023 for three n...
Following the announcement by the Department for Transport (DfT) of a sixth round of the UK SHORE ‘Clean Maritime Demonstration Competition’ earlier this year, the winners have now been an...
2M Logistics Holding B.V. (NL) and the internationally operating Gallozzi Group (Italy) have entered into a strategic partnership. As business partners, both parties will collaborate closely on comme...
ClassNK has granted its Innovation Endorsement for Products & Solutions to the maritime cybersecurity support solution, ‘CYTUR-MCTI’ developed by CYTUR and its partner company - Rakute...
Watson Farley & Williams ("WFW") advised Pacific Basin Shipping ("Pacific Basin") on a US$250m sustainability-linked seven-year senior secured committed revolving credit facility. The facilit...
Alva Industries (Alva), a manufacturer of frameless motors and owner and creator of FiberPrinting technology, has announced the publication of a series of new white papers on FiberPrinted motors for h...
DNV has awarded a General Approval for Ship Application (GASA) certificate to Mitsui O.S.K. Lines, Ltd., (MOL), MISC Berhad (MISC), PETRONAS CCS Ventures Sdn. Bhd. (PCCSV), and Shanghai Merchant Ship...
ClassNK has released 'ClassNK Technical Journal No.11 2025 (Ⅰ)'. This issue features the title 'Latest Technological Trends for Protection of the Marine Environment', providing the particularly well-r...
RAD Propulsion, a globally renowned innovator in electric marine propulsion systems, announced the expansion of its international dealer network with new strategic partnerships in the Netherlands, Ind...
As maritime companies digitise, decarbonise, and expand across continents, standing out in the market has never been more challenging. Customers expect clarity. Talent is scarce. And lead generation t...
Watson Farley & Williams advised ING Bank N.V., Singapore Branch—acting as arranger, lender and facility and security agent — on a term loan facility provided to Tank Container Investm...
LOOKOUT, the AI pioneer in marine safety, launched enhanced benefits to marine professionals through its preferred dealer and installer programme. The new resources help LOOKOUT dealers and installer...
The new version of KaizenWEG, developed with low-code technologies and artificial intelligence, strengthens participative management and drives a global culture of collaborative innovation. WEG has r...
Multi-party collaboration addresses serious threat to safety of navigation and visibility of high-value assets in degraded and compromised Global Positioning System (GPS) and Global Navigation Satelli...
ClassNK has granted its Innovation Endorsement for Products & Solutions to the maritime cybersecurity support solution, “CYTUR-MCTI” developed by CYTUR and its partner company Rakuten...
Econowind has received a repeat order from Terntank for the installation of eight VentoFoil units on two additional methanol-ready hybrid tankers. Following the initial order in May 2023 for three n...
Following the announcement by the Department for Transport (DfT) of a sixth round of the UK SHORE ‘Clean Maritime Demonstration Competition’ earlier this year, the winners have now been an...
2M Logistics Holding B.V. (NL) and the internationally operating Gallozzi Group (Italy) have entered into a strategic partnership. As business partners, both parties will collaborate closely on comme...
ClassNK has granted its Innovation Endorsement for Products & Solutions to the maritime cybersecurity support solution, ‘CYTUR-MCTI’ developed by CYTUR and its partner company - Rakute...
Watson Farley & Williams ("WFW") advised Pacific Basin Shipping ("Pacific Basin") on a US$250m sustainability-linked seven-year senior secured committed revolving credit facility. The facilit...